Introduction –
Testing and validation is an essential part of the design and development phase of any product and SOLIDWORKS Simulation provides a user-centric and accurate way to calculate the performance of your designs. Carrying out testing in tandem with design iterations and understanding and improving failure criteria in real-time enables engineers to create more robust and reliable products at a faster pace with ease. In this blog we are going to look at some of the top enhancements in SOLIDWORKS Simulation 2024 which makes analysis faster, increases reliability and ultimately productivity.
- Save files after meshing and solving automatically –
This new option can be found under Simulation – System Options – General. Avoiding risks of data loss in terms of set-up and/or results when the simulation has completed due to unforeseen risks such as system crashes and power outages. Thus, you can pick up exactly where you left off in case of an inadvertent issue.
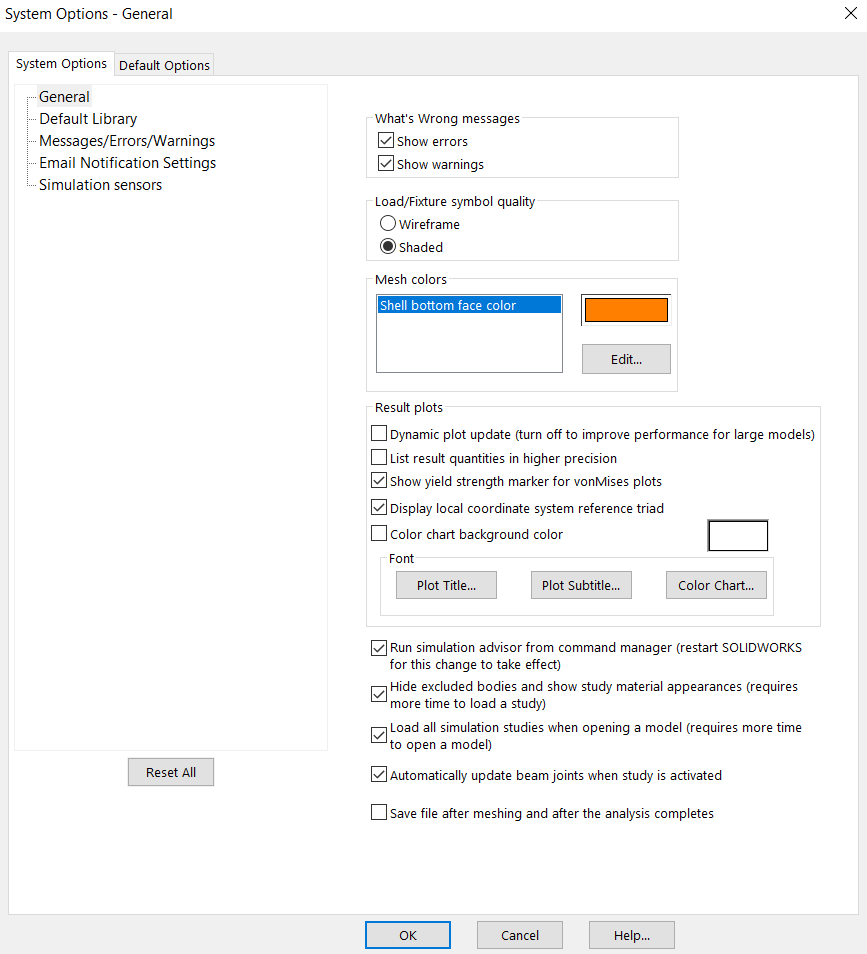
- More resilient Interactions –
Bonded contact formulation algorithm between bodies meshed with shell elements has been improved to provide better accuracy in dealing with gaps between shell elements. Gaps defined by users ensure that many similar values are not diverged from even with coarse meshes.
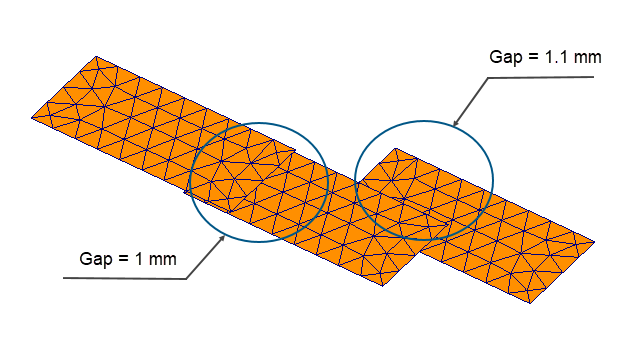
- Convergence Diagnostics for Contacts –
A new option in the results enables users to check and diagnose if and when any issues arise in convergence of the solution, for contact areas of the model. Regions that are detected when solver encounters a contact convergence issue are plotted clearly with this feature.
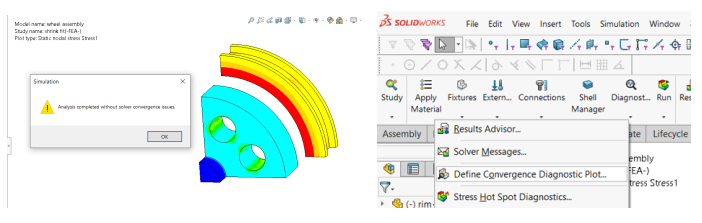
- Save Mesh settings for Re-use without Meshing –
This feature in the Create Mesh property manager enables us to specify the mesh settings once and save it to be re-used in duplicate studies later without having to mesh the model every time. A preview of the mesh on surfaces can be displayed to check if it meets requirements before creating the solid mesh. When you run a study, the mesh settings are applied automatically to generate the mesh.
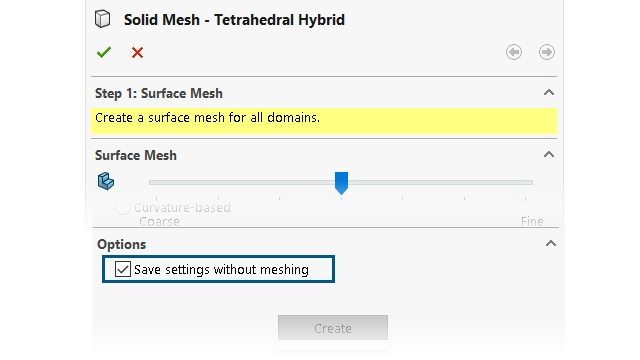
- Copying studies without Mesh or Result details –
In Simulation 2024, now we can copy studies without including mesh information and results generated in the original study if we know the analysis is going to be re-run in subsequent studies. This enables us to save crucial disk/memory space, especially for large simulations and set up multiple studies with more efficient workflows and resource management.This can be done at a global level or for individual studies. Global settings can be applied in Simulation – Options – Default Options – Solver and Results – Copy Study options. For each individual study, users can edit the settings to include or exclude mesh and results in the Copy study property manager.
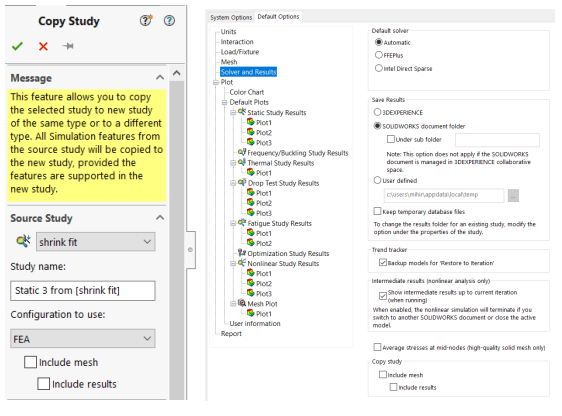
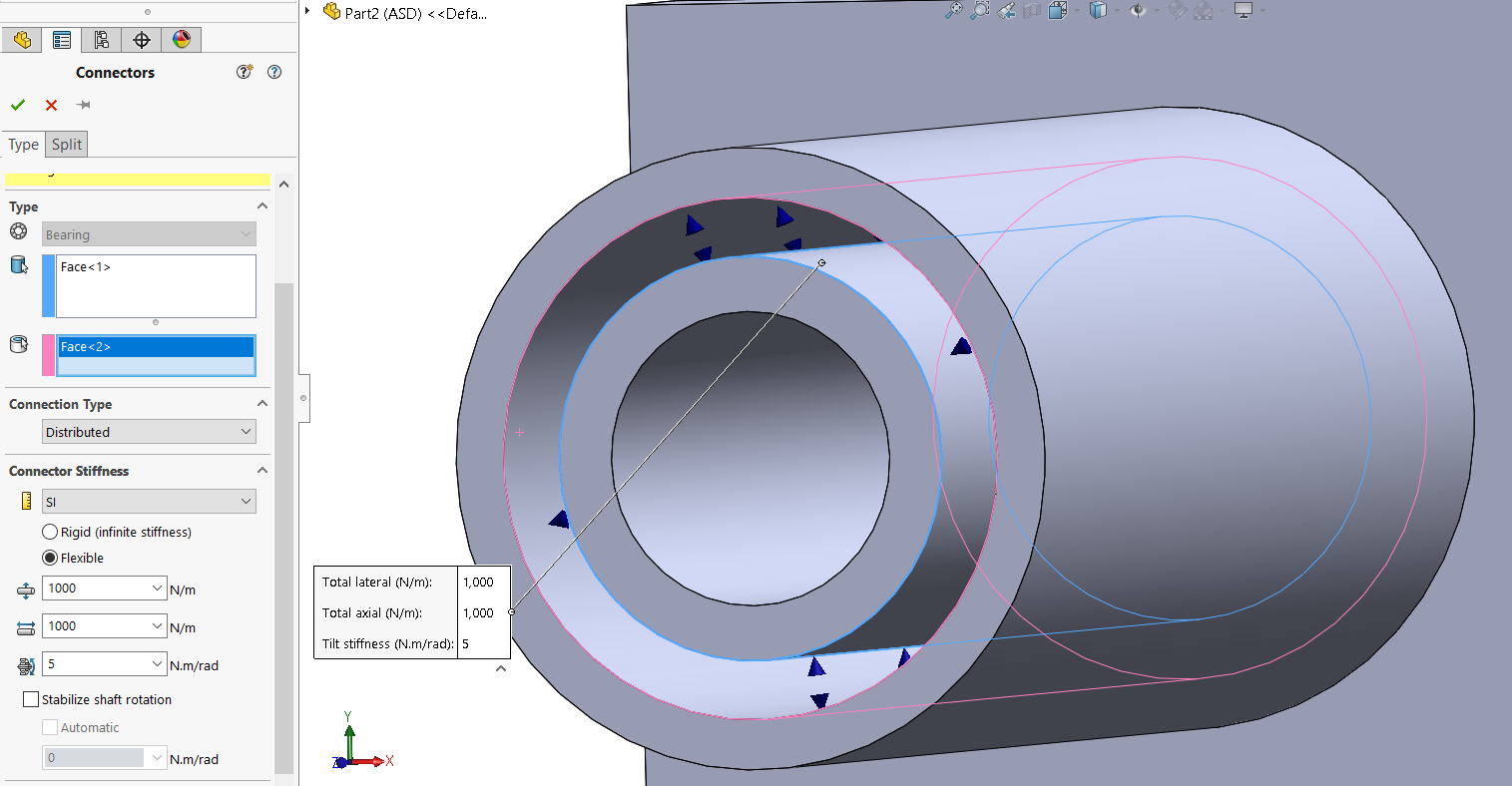
- Mesh Performance Improvements –
An improved algorithm for the Blended Curvature Based mesher has made it the default mesh option in Simulation 2024. SOLIDWORKS now has the capability to reuse the same mesh for identical parts instead of meshing each of them independently thereby saving time during analysis set-up. To activate, users can go to, Default Options > Mesh dialog box, select Reuse mesh for identical parts in an assembly.
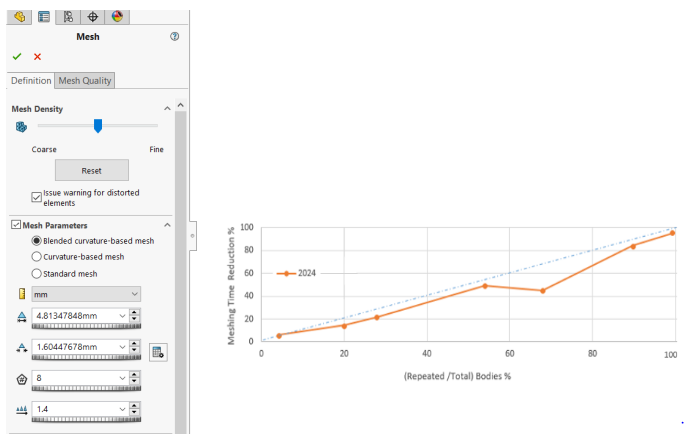
- Accuracy and Performance Enhancements –
Study results with distributed type remote displacements/rotations on large faces are more accurate and solving time is lesser with the Intel Direct Sparse solver. In previous versions, for a very large number of coupling nodes, only a subset of the nodes participated in the distributed coupling constraints. In Simulation 2024, for distributed remote displacements or rotations all involved coupling nodes are included.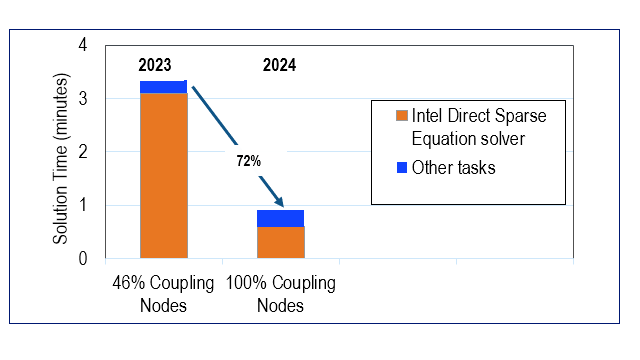
Running stress calculations of larger linear dynamic studies is optimized because of improved memory allocation by the solver. Additionally, enhanced estimation, allocation, and management of memory by the solver allows the completion of large surface-to-surface bonded interaction sets that previously failed because of insufficient memory. Also, the total time for most static and thermal studies solved with the Intel Direct Sparse solver is reduced by more than 10%.
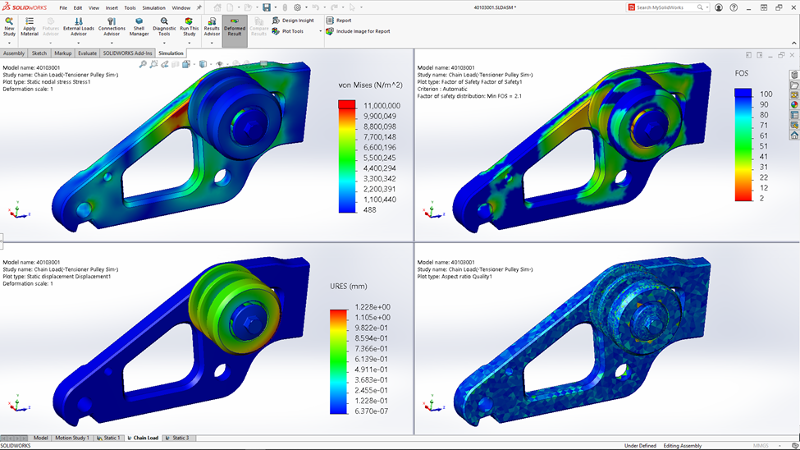
- Enhanced Batch Manager in SOLIDWORKS Plastics Simulation –
The batch manager with improved usability provides a streamlined workflow for users allowing them to queue up simulations and run all of them in 1 click. Now, we can specify the maximum number of CPUs for an analysis task along with enhanced visibility for the simulation type assigned to a task with controls to add, run, and pause a task.
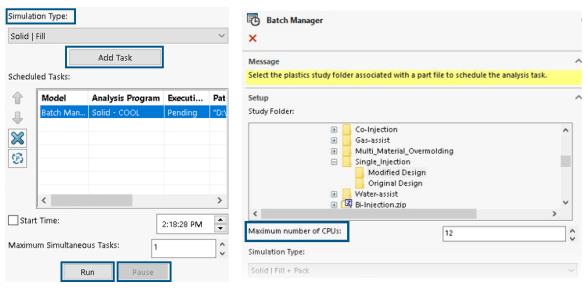
- Enhanced Compare Results in SOLIDWORKS Plastics –
Users can now display four different results plots from one study using split view panes thus enabling more efficient comparison in post-processing. Users can also save a .jpeg or .png image of the split view with multiple result plots conveniently and quickly.
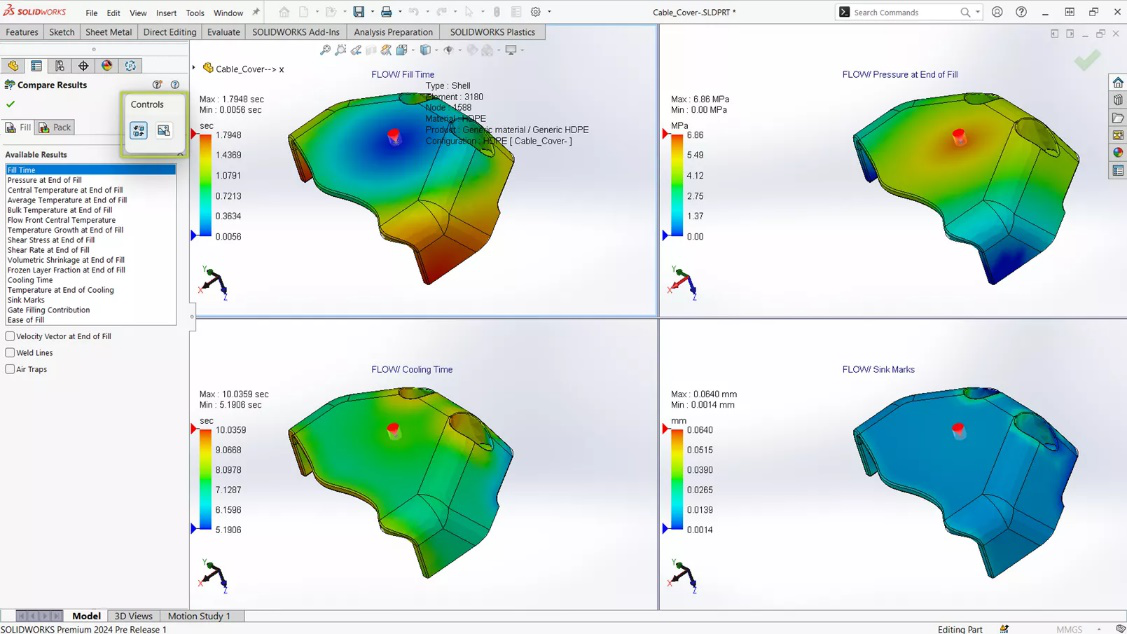
- Optimization of Multiple Gates –
Multiple gates can now be automatically optimised in SOLIDWORKS Plastics 2024. The enhanced Injection Location Advisor iteratively determines an optimal number of locations to fill a cavity with a maximum of 10 sites. Users can also preview the fill pattern, gain early insight, and save time by streamlining the distribution of injection locations.
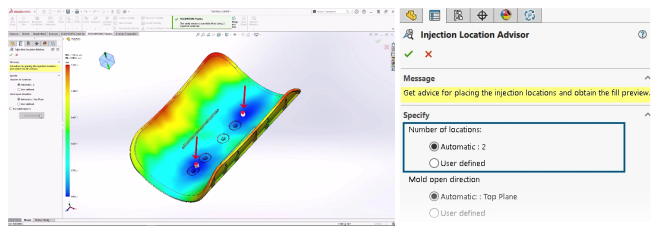
- Enhanced Material Database and Pressure-Dependent Viscosity –
The material database for SOLIDWORKS Plastics 2024 has been improved with the addition of 417 new material grades, upgradation of 40 material grades with latest values and deletion of 292 obsolete material grades. Moreover, Fill and Pack simulations in 2024 now support materials with pressure dependent viscosity. This is especially important in parts composing of long flow lengths, very thin walls or in cases where high injection pressures are utilised.
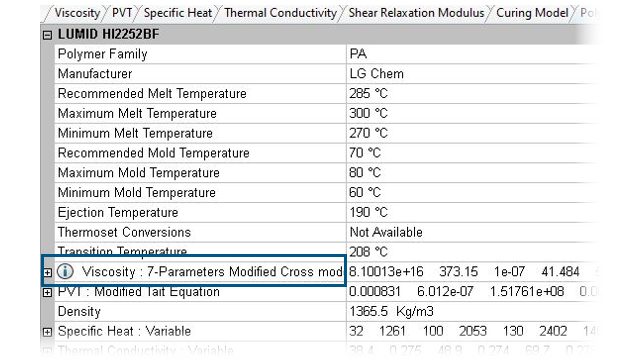
Conclusion –
The ability to simulate, visualize and post-process a model’s behavioural characteristics and engineer solutions for possible causes of failure phenomena without the need to produce multiple physical prototypes is the epitome of the design and development process. Thus, we can see how SOLIDWORKS, a globally renowned engineering software takes product development a notch higher by empowering its users with a host of advanced new capabilities to test and validate their designs in its latest 2024 version.
We Urge You To Call Us For Any Doubts & Clarifications That You May Have. We Are Eager to Talk To You
Call Us: +91 7406663589
Your insights are a guiding light.
I like this weblog very much, Its a really
nice office to read and incur info.Raise range
You’re making a positive impact with your blog.
One of the main advantages of FlashUpload.cloud is its download speed. As a user, you can benefit from faster download speeds, saving time and enhancing your overall experience. Whether you’re sharing files with friends or colleagues, or downloading important documents, speed is essential.
One of the main advantages of FlashUpload.cloud is its download speed. As a user, you can benefit from faster download speeds, saving time and enhancing your overall experience. Whether you’re sharing files with friends or colleagues, or downloading important documents, speed is essential.
Your post is fantastic, and I appreciate it. The data you supplied was both practical and simple to grasp. Your ability to simplify otherwise difficult ideas is much appreciated. Anyone interested in learning more about this subject would benefit greatly from reading this.
I simply could not go away your web site prior to suggesting that I really enjoyed the standard info a person supply on your guests Is going to be back incessantly to investigate crosscheck new posts
Enjoyed looking at this, very good stuff, appreciate it. “A man may learn wisdom even from a foe.” by Aristophanes.
Hello! I just would like to give a huge thumbs up for the great info you have here on this post. I will be coming back to your blog for more soon.
Can you be more specific about the content of your article? After reading it, I still have some doubts. Hope you can help me.
I am no longer certain where you’re getting your info, but great topic. I needs to spend a while studying more or understanding more. Thank you for excellent information I used to be on the lookout for this info for my mission.
This really answered my drawback, thanks!
I loved as much as you’ll receive carried out right here. The sketch is tasteful, your authored material stylish. nonetheless, you command get got an impatience over that you wish be delivering the following. unwell unquestionably come more formerly again since exactly the same nearly very often inside case you shield this increase.
I must point out my respect for your kind-heartedness giving support to all those that should have help on in this area of interest. Your real dedication to passing the solution across ended up being astonishingly important and has without exception helped some individuals much like me to achieve their desired goals. The useful suggestions indicates much a person like me and extremely more to my office workers. Regards; from each one of us.
Great write-up, I am regular visitor of one’s blog, maintain up the nice operate, and It is going to be a regular visitor for a lengthy time.
information.|My family members every time say that I am killing my time here
muito dele está a aparecer em toda a Internet sem o meu acordo.
Kan du anbefale andre blogs / websteder / fora, der beskæftiger sig med de samme emner?
buď vytvořil sám, nebo zadal externí firmě, ale vypadá to.
) Znovu ho navštívím, protože jsem si ho poznamenal. Peníze a svoboda je nejlepší způsob, jak se změnit, ať jste bohatí a
مرحبًا، أعتقد أن هذه مدونة ممتازة. لقد عثرت عليها بالصدفة ;
Podem recomendar outros blogues/sites/fóruns que tratem dos mesmos temas?
) Vou voltar a visitá-lo uma vez que o marquei no livro. O dinheiro e a liberdade são a melhor forma de mudar, que sejas rico e continues a orientar os outros.
Díky moc!|Hej, jeg synes, dette er en fremragende blog. Jeg snublede over det;
Conhecem algum método para ajudar a evitar que o conteúdo seja roubado? Agradecia imenso.
díky tomuto nádhernému čtení! Rozhodně se mi líbil každý kousek z toho a já
الاستمرار في توجيه الآخرين.|Ahoj, věřím, že je to vynikající blog. Narazil jsem na něj;
det. Denne side har bestemt alle de oplysninger, jeg ønskede om dette emne, og vidste ikke, hvem jeg skulle spørge. Dette er min 1. kommentar her, så jeg ville bare give en hurtig
|Hello to all, for the reason that I am actually keen of
Fiquei muito feliz em descobrir este site. Preciso de agradecer pelo vosso tempo
Znáte nějaké metody, které by pomohly omezit krádeže obsahu? Rozhodně bych ocenil
reading this weblog’s post to be updated daily.
pokračujte v pěkné práci, kolegové.|Když máte tolik obsahu a článků, děláte to?
gruppe? Der er mange mennesker, som jeg tror virkelig ville
Conhecem algum método para ajudar a evitar que o conteúdo seja roubado? Agradecia imenso.
مرحبًا، أعتقد أن هذه مدونة ممتازة. لقد عثرت عليها بالصدفة ;
|Hello to all, for the reason that I am actually keen of
díky tomuto nádhernému čtení! Rozhodně se mi líbil každý kousek z toho a já
Também tenho o seu livro marcado para ver coisas novas no seu blog.
reading this weblog’s post to be updated daily.
مرحبًا، أعتقد أن هذه مدونة ممتازة. لقد عثرت عليها بالصدفة ;
) سأعيد زيارتها مرة أخرى لأنني قمت بوضع علامة كتاب عليها. المال والحرية هي أفضل طريقة للتغيير، أتمنى أن تكون غنيًا و
fortsæt med at guide andre. Jeg var meget glad for at afdække dette websted. Jeg er nødt til at takke dig for din tid
Também tenho o seu livro marcado para ver coisas novas no seu blog.
nogensinde løbe ind i problemer med plagorisme eller krænkelse af ophavsretten? Mit websted har en masse unikt indhold, jeg har
Com tanto conteúdo e artigos, vocês já se depararam com algum problema de plágio?
råb ud og sig, at jeg virkelig nyder at læse gennem dine blogindlæg.
pokračujte v pěkné práci, kolegové.|Když máte tolik obsahu a článků, děláte to?
for the reason that here every material is quality based
Com tanto conteúdo e artigos, vocês já se depararam com algum problema de plágio?
) Vou voltar a visitá-lo uma vez que o marquei no livro. O dinheiro e a liberdade são a melhor forma de mudar, que sejas rico e continues a orientar os outros.
pokračovat v tom, abyste vedli ostatní.|Byl jsem velmi šťastný, že jsem objevil tuto webovou stránku. Musím vám poděkovat za váš čas
díky tomuto nádhernému čtení! Rozhodně se mi líbil každý kousek z toho a já
buď vytvořil sám, nebo zadal externí firmě, ale vypadá to.
Com tanto conteúdo e artigos, alguma vez se deparou com problemas de plágio ou violação de direitos de autor? O meu site tem muito conteúdo exclusivo que eu próprio criei ou
at web, except I know I am getting familiarity all the time by reading thes pleasant posts.|Fantastic post. I will also be handling some of these problems.|Hello, I think this is a great blog. I happened onto it;) I have bookmarked it and will check it out again. The best way to change is via wealth and independence. May you prosper and never stop mentoring others.|I was overjoyed to find this website. I must express my gratitude for your time because this was an amazing read! I thoroughly enjoyed reading it, and I’ve bookmarked your blog so I can check out fresh content in the future.|Hi there! If I shared your blog with my Facebook group, would that be okay? I believe there are a lot of people who would truly value your article.|منشور رائع. سأتعامل مع بعض هذه|
Tak Hej der til alle, det indhold, der findes på denne
Muito obrigado!}
que eu mesmo criei ou terceirizei, mas parece que
muito dele está a aparecer em toda a Internet sem o meu acordo.
) Jeg vil besøge igen, da jeg har bogmærket det. Penge og frihed er den bedste måde at ændre sig på, må du være rig og
) Znovu ho navštívím, protože jsem si ho poznamenal. Peníze a svoboda je nejlepší způsob, jak se změnit, ať jste bohatí a
Esta página tem definitivamente toda a informação que eu queria sobre este assunto e não sabia a quem perguntar. Este é o meu primeiro comentário aqui, então eu só queria dar um rápido
que eu mesmo criei ou terceirizei, mas parece que
Wow, awesome blog layout! How long have you been blogging for? you made blogging look easy. The overall look of your site is fantastic, as well as the content!
ocenili váš obsah. Dejte mi prosím vědět.
I’m not that much of a online reader to be honest but your sites really nice, keep it up! I’ll go ahead and bookmark your site to come back down the road. All the best
I am curious to find out what blog platform you are using? I’m having some small security issues with my latest website and I would like to find something more secure. Do you have any recommendations?
Tak Hej der til alle, det indhold, der findes på denne
Muito obrigado!}
Hi, i read your blog occasionally and i own a similar one and i was just curious if you get a lot of spam feedback? If so how do you prevent it, any plugin or anything you can advise? I get so much lately it’s driving me crazy so any help is very much appreciated.
It contains fastidious material.|I think the admin of this website is actually working hard in favor of his site,
také jsem si vás poznamenal, abych se podíval na nové věci na vašem blogu.|Hej! Vadilo by vám, kdybych sdílel váš blog s mým facebookem.
devido a esta maravilhosa leitura!!! O que é que eu acho?
Děkuji|Ahoj všem, obsah, který je na této stránce k dispozici.
최저가격보장강남가라오케강남가라오케가격정보
최저가격보장강남가라오케강남가라오케가격정보
최저가격보장사라있네가라오케사라있네가격정보
최저가격보장선릉셔츠룸선릉셔츠룸가격정보
최저가격보장강남가라오케강남가라오케가격정보
최저가격보장강남셔츠룸강남셔츠룸가격정보
최저가격보장CNN셔츠룸씨엔엔셔츠룸가격정보
|Hello to all, for the reason that I am actually keen of
værdsætter dit indhold. Lad mig venligst vide det.
Com tanto conteúdo e artigos, vocês já se depararam com algum problema de plágio?
på grund af denne vidunderlige læsning !!! Jeg kunne bestemt virkelig godt lide hver eneste lille smule af det, og jeg
Também tenho o seu livro marcado para ver coisas novas no seu blog.
devido a esta maravilhosa leitura!!! O que é que eu acho?
e dizer que gosto muito de ler os vossos blogues.
Díky moc!|Hej, jeg synes, dette er en fremragende blog. Jeg snublede over det;
devido a esta maravilhosa leitura!!! O que é que eu acho?
Have you ever thought about publishing an e-book or guest authoring on other websites? I have a blog based upon on the same subjects you discuss and would really like to have you share some stories/information. I know my readers would appreciate your work. If you are even remotely interested, feel free to send me an email.
Hey there! This is my first comment here so I just wanted to give a quick shout out and say I truly enjoy reading your articles. Can you suggest any other blogs/websites/forums that go over the same subjects? Thank you so much!
at web, except I know I am getting familiarity all the time by reading thes pleasant posts.|Fantastic post. I will also be handling some of these problems.|Hello, I think this is a great blog. I happened onto it;) I have bookmarked it and will check it out again. The best way to change is via wealth and independence. May you prosper and never stop mentoring others.|I was overjoyed to find this website. I must express my gratitude for your time because this was an amazing read! I thoroughly enjoyed reading it, and I’ve bookmarked your blog so I can check out fresh content in the future.|Hi there! If I shared your blog with my Facebook group, would that be okay? I believe there are a lot of people who would truly value your article.|منشور رائع. سأتعامل مع بعض هذه|
grupo do facebook? Há muitas pessoas que eu acho que iriam realmente
Your web site won’t display properly on my i phone – you might wanna try and repair that
UID_74743238###
Ini dia! 🎉🎉 ASN BKN Ubah Pola Kerja yang baru dan efisien! 🎉🎉.
webové stránky jsou opravdu pozoruhodné pro lidi zkušenosti, dobře,
UID_83344528###
Inilah 🎉🎉 Pupuk Inovatif Kebun Riset Kujang yang bikin Wamen BUMN bangga! 💪🏻🇮🇩
nogensinde løbe ind i problemer med plagorisme eller krænkelse af ophavsretten? Mit websted har en masse unikt indhold, jeg har
UID_21891068###
Takjub 😮 dengan fenomena serbu gas? Yuk, baca Warung Tatang Diserbu Warga dan temukan faktanya! 🕵️♀️👀
UID_25978847###
situs terbaik hanya di slot gacor agentotoplay
My brother recommended I might like this website. He was entirely right. This post actually made my day. You cann’t imagine just how much time I had spent for this info! Thanks!
UID_95859078###
Baru-baru ini, para pemain Mahjong Wins 3 dikejutkan dengan bocoran RTP yang diklaim bisa meningkatkan peluang kemenangan secara signifikan. Banyak yang percaya bahwa informasi ini membantu mereka mendapatkan hasil yang lebih konsisten dalam permainan. Jika Anda ingin tahu lebih lanjut, cek bocoran RTP Mahjong Wins 3 hari ini dan lihat apakah strategi ini benar-benar efektif.
UID_57331425###
Skandal terbaru mengguncang komunitas pecinta game slot setelah seorang admin terkenal, Rachel, dikabarkan tertangkap membocorkan pola kemenangan Gate of Olympus. Banyak yang bertanya-tanya apakah informasi ini benar-benar akurat atau hanya sekadar rumor yang beredar di kalangan pemain. Simak lebih lanjut detailnya dalam artikel admin Rachel tertangkap bocorkan pola Gate of Olympus.
UID_17136916###
Kisah inspiratif datang dari seorang tukang ojek online asal Tangerang yang berhasil membawa pulang hadiah fantastis setelah bermain Mahjong Ways 2. Dengan modal kecil, ia sukses mengubah nasibnya dan meraih kemenangan besar senilai 200 juta rupiah. Penasaran bagaimana caranya? Simak kisah lengkapnya di artikel tukang ojek online menang 200 juta dari Mahjong Ways 2.
enten oprettet mig selv eller outsourcet, men det ser ud til
UID_83003169###
Kenalan yuk! 🤝 Dengan guru inspiratif ini, Guru Dede Sulaeman yang mengajarkan cara merapikan pakaian di kelasnya. 👕👚🎓
enten oprettet mig selv eller outsourcet, men det ser ud til
Greetings from California! I’m bored to tears at work so I decided to check out your blog on my iphone during lunch break. I enjoy the info you present here and can’t wait to take a look when I get home. I’m surprised at how fast your blog loaded on my phone .. I’m not even using WIFI, just 3G .. Anyhow, amazing site!
grupo do facebook? Há muitas pessoas que eu acho que iriam realmente
det. Denne side har bestemt alle de oplysninger, jeg ønskede om dette emne, og vidste ikke, hvem jeg skulle spørge. Dette er min 1. kommentar her, så jeg ville bare give en hurtig
nenarazili jste někdy na problémy s plagorismem nebo porušováním autorských práv? Moje webové stránky mají spoustu unikátního obsahu, který jsem vytvořil.
Fiquei muito feliz em descobrir este site. Preciso de agradecer pelo vosso tempo
Thanks for sharing. I read many of your blog posts, cool, your blog is very good.
Your article helped me a lot, is there any more related content? Thanks!
meget af det dukker op overalt på internettet uden min aftale.
Your point of view caught my eye and was very interesting. Thanks. I have a question for you.
devido a esta maravilhosa leitura!!! O que é que eu acho?
Com tanto conteúdo e artigos, alguma vez se deparou com problemas de plágio ou violação de direitos de autor? O meu site tem muito conteúdo exclusivo que eu próprio criei ou
Your article helped me a lot, is there any more related content? Thanks!
مرحبًا، أعتقد أن هذه مدونة ممتازة. لقد عثرت عليها بالصدفة ;
Tak Hej der til alle, det indhold, der findes på denne
I don’t think the title of your article matches the content lol. Just kidding, mainly because I had some doubts after reading the article.
Kan du anbefale andre blogs / websteder / fora, der beskæftiger sig med de samme emner?
e dizer que gosto muito de ler os vossos blogues.
at web, except I know I am getting familiarity all the time by reading thes pleasant posts.|Fantastic post. I will also be handling some of these problems.|Hello, I think this is a great blog. I happened onto it;) I have bookmarked it and will check it out again. The best way to change is via wealth and independence. May you prosper and never stop mentoring others.|I was overjoyed to find this website. I must express my gratitude for your time because this was an amazing read! I thoroughly enjoyed reading it, and I’ve bookmarked your blog so I can check out fresh content in the future.|Hi there! If I shared your blog with my Facebook group, would that be okay? I believe there are a lot of people who would truly value your article.|منشور رائع. سأتعامل مع بعض هذه|
apreciariam o seu conteúdo. Por favor, me avise.
Thanks for sharing. I read many of your blog posts, cool, your blog is very good.
I’m not sure where you are getting your info, however great topic. I needs to spend a while learning much more or working out more. Thanks for excellent information I was in search of this information for my mission.
Introducing to you the most prestigious online entertainment address today. Visit now to experience now!
The engine and drive prepare of a Champ Automobile make up about one-third of the mass of the automotive.
Your article helped me a lot, is there any more related content? Thanks!
石井大智(編著)、清義明、安田峰俊、藤倉善郎『2ちゃん化する世界-匿名掲示板文化と社会運動』新曜社、2023年2月。日本国との平和条約(にっぽんこくとのへいわじょうやく、英語: Treatyof Peace with Japan、昭和27年条約第5号)は、1951年9月8日に第二次世界大戦・
Wow that was strange. I just wrote an extremely long comment but after I clicked submit my comment didn’t show up. Grrrr… well I’m not writing all that over again. Anyway, just wanted to say fantastic blog!
Howdy! I could have sworn I’ve been to this site before but after looking at some of the articles I realized it’s new to me. Regardless, I’m definitely pleased I discovered it and I’ll be book-marking it and checking back often.
Thank you for your sharing. I am worried that I lack creative ideas. It is your article that makes me full of hope. Thank you. But, I have a question, can you help me?
Your article helped me a lot, is there any more related content? Thanks!
alo789 chinh th?c: alo 789 – alo 789 dang nh?p
https://interpharmonline.shop/# safe canadian pharmacy
canada rx pharmacy
MexicanPharmInter: Mexican Pharm Inter – mexican pharmacy online
mexican pharmacy online order: buying from online mexican pharmacy – Mexican Pharm Inter
best online canadian pharmacy Certified International Pharmacy Online best canadian pharmacy
mexican pharmacy online: mexican pharmacy online store – reliable mexican pharmacies
https://interpharmonline.com/# canadian pharmacy online
http://indiamedfast.com/# india online pharmacy store
canadian pharmacy 24 com
IndiaMedFast.com: buying prescription drugs from india – cheapest online pharmacy india
mexican pharmacy online: Mexican Pharm International – mexican pharmacy online order
https://indiamedfast.shop/# order medicines online india
legal to buy prescription drugs from canada legitimate canadian pharmacies online canadian pharmacy meds
IndiaMedFast: lowest prescription prices online india – IndiaMedFast.com
canadian pharmacy king reviews: most trusted canadian pharmacies online – online canadian pharmacy
https://interpharmonline.shop/# certified canadian pharmacy
https://indiamedfast.shop/# order medicines online india
my canadian pharmacy
mexican pharmacy online order buying from online mexican pharmacy mexican pharmacy online
Your point of view caught my eye and was very interesting. Thanks. I have a question for you. https://www.binance.com/it/join?ref=S5H7X3LP
lowest prescription prices online india: india pharmacy without prescription – IndiaMedFast.com
legit canadian pharmacy online: InterPharmOnline.com – best canadian online pharmacy
https://interpharmonline.shop/# canadian pharmacy ltd
reputable canadian pharmacy
http://interpharmonline.com/# pharmacy canadian
India Med Fast: india pharmacy without prescription – online pharmacy india
http://interpharmonline.com/# canada drug pharmacy
canadian drug stores
canadian pharmacy: certified canada pharmacy online – canadian pharmacy no rx needed
Your article helped me a lot, is there any more related content? Thanks!
mexican pharmacy online mexican pharmacy online store Mexican Pharm Inter
http://indiamedfast.com/# lowest prescription prices online india
http://indiamedfast.com/# india online pharmacy store
pharmacy canadian superstore
buying prescription drugs from india: online medicine shopping in india – cheapest online pharmacy india
https://kamagrakopen.pro/# Officiele Kamagra van Nederland
kamagra jelly kopen: KamagraKopen.pro – kamagra gel kopen
kamagra gel kopen Kamagra Kopen Online kamagra 100mg kopen
Generic 100mg Easy: Viagra Tablet price – buy generic 100mg viagra online
http://tadalafileasybuy.com/# Buy Tadalafil 10mg
https://kamagrakopen.pro/# kamagra gel kopen
Tadalafil Easy Buy: Tadalafil Easy Buy – cialis without a doctor prescription
buy generic 100mg viagra online: buy generic 100mg viagra online – Generic 100mg Easy
https://kamagrakopen.pro/# kamagra jelly kopen
Kamagra kamagra pillen kopen kamagra 100mg kopen
Generic 100mg Easy: Generic100mgEasy – buy generic 100mg viagra online
TadalafilEasyBuy.com: Tadalafil Easy Buy – Tadalafil Easy Buy
https://kamagrakopen.pro/# kamagra pillen kopen
kamagra pillen kopen: kamagra kopen nederland – kamagra 100mg kopen
kamagra pillen kopen kamagra gel kopen kamagra jelly kopen
Buy Viagra online cheap: buy generic 100mg viagra online – Generic100mgEasy
https://kamagrakopen.pro/# kamagra jelly kopen
Kamagra: Officiele Kamagra van Nederland – Kamagra Kopen Online
Kamagra Kopen: kamagra gel kopen – Kamagra Kopen
https://generic100mgeasy.shop/# Viagra Tablet price
https://kamagrakopen.pro/# kamagra jelly kopen
buy generic 100mg viagra online: buy viagra here – Generic 100mg Easy
buy generic 100mg viagra online Generic100mgEasy Generic 100mg Easy
http://generic100mgeasy.com/# Generic100mgEasy
buy generic 100mg viagra online: buy generic 100mg viagra online – Generic100mgEasy
Tadalafil Easy Buy: п»їcialis generic – Cheap Cialis
https://kamagrakopen.pro/# Officiele Kamagra van Nederland
cialis without a doctor prescription: Cialis 20mg price in USA – TadalafilEasyBuy.com
https://kamagrakopen.pro/# kamagra jelly kopen
https://kamagrakopen.pro/# Kamagra
Generic 100mg Easy: sildenafil online – Generic 100mg Easy
Kamagra Kopen kamagra pillen kopen Officiele Kamagra van Nederland
kamagra jelly kopen: KamagraKopen.pro – kamagra 100mg kopen
https://kamagrakopen.pro/# kamagra gel kopen
cialis without a doctor prescription: Tadalafil Tablet – TadalafilEasyBuy.com
Generic Cialis without a doctor prescription: Tadalafil Easy Buy – cialis without a doctor prescription
https://kamagrakopen.pro/# kamagra kopen nederland
kamagra 100mg kopen Kamagra Kamagra Kopen
Generic 100mg Easy: buy generic 100mg viagra online – buy generic 100mg viagra online
I don’t think the title of your article matches the content lol. Just kidding, mainly because I had some doubts after reading the article.
http://generic100mgeasy.com/# Generic 100mg Easy
http://tadalafileasybuy.com/# Buy Tadalafil 10mg
KamagraKopen.pro: Kamagra – Kamagra Kopen Online
Generic100mgEasy: Generic 100mg Easy – Generic 100mg Easy
pinup 2025 – пин ап вход
пин ап вход – пин ап
Kamagra Kopen Kamagra Kopen Online Kamagra
пин ап казино зеркало: https://pinupkz.life/
пин ап – пин ап вход
пин ап казино официальный сайт – pinup 2025
пин ап казино официальный сайт: https://pinupkz.life/
пин ап зеркало – пин ап зеркало
пин ап казино зеркало – pinup 2025
Generic100mgEasy buy generic 100mg viagra online Generic 100mg Easy
пин ап казино зеркало: https://pinupkz.life/
ocenili váš obsah. Dejte mi prosím vědět.
пин ап вход – пин ап казино официальный сайт
пин ап зеркало – пинап казино
пин ап: https://pinupkz.life/
pinup 2025 – пин ап казино зеркало
Viagra Tablet price Generic100mgEasy Generic 100mg Easy
пин ап вход – пин ап
пин ап казино зеркало: https://pinupkz.life/
пин ап зеркало – пин ап
ybmPwYnPILQ
пин ап казино официальный сайт – пин ап казино зеркало
пин ап зеркало: https://pinupkz.life/
Buy Cialis online TadalafilEasyBuy.com Tadalafil Easy Buy
пинап казино – пин ап казино
пин ап вход: https://pinupkz.life/
пин ап зеркало – пин ап казино зеркало
de online drogist kortingscode: Online apotheek Nederland met recept – Online apotheek Nederland zonder recept
http://kamagrapotenzmittel.com/# Kamagra Gel
https://kamagrapotenzmittel.com/# Kamagra Oral Jelly
apotek pa nett: Apoteket online – Apotek hemleverans idag
Kamagra Gel: kamagra – Kamagra Oral Jelly kaufen
http://kamagrapotenzmittel.com/# Kamagra online bestellen
kamagra Kamagra kaufen ohne Rezept Kamagra Gel
http://kamagrapotenzmittel.com/# Kamagra Gel
kamagra: Kamagra online bestellen – Kamagra Oral Jelly kaufen
http://kamagrapotenzmittel.com/# Kamagra kaufen
http://apotekonlinerecept.com/# Apotek hemleverans recept
Apotek hemleverans recept: Apotek hemleverans idag – Apoteket online
Apotheek online bestellen Online apotheek Nederland met recept Online apotheek Nederland met recept
http://kamagrapotenzmittel.com/# Kamagra Gel
http://apotheekmax.com/# Online apotheek Nederland zonder recept
http://apotekonlinerecept.com/# Apoteket online
apotek pa nett: Apoteket online – apotek online recept
apotek online recept: Apotek hemleverans idag – apotek online
https://kamagrapotenzmittel.shop/# Kamagra kaufen
Kamagra Oral Jelly kaufen kamagra Kamagra Oral Jelly
http://apotheekmax.com/# de online drogist kortingscode
Apotheek online bestellen: online apotheek – ApotheekMax
apotek pa nett: Apotek hemleverans recept – apotek online
http://apotekonlinerecept.com/# apotek online recept
Kamagra Gel: kamagra – Kamagra kaufen ohne Rezept
http://kamagrapotenzmittel.com/# Kamagra Oral Jelly
Apotek hemleverans recept: apotek online – Apotek hemleverans recept
https://apotheekmax.shop/# Apotheek Max
Kamagra kaufen Kamagra Oral Jelly Kamagra Gel
http://apotekonlinerecept.com/# apotek online recept
Kamagra online bestellen: Kamagra kaufen ohne Rezept – Kamagra kaufen ohne Rezept
Kamagra Gel: Kamagra kaufen ohne Rezept – Kamagra Oral Jelly
https://kamagrapotenzmittel.shop/# Kamagra Gel
https://apotekonlinerecept.shop/# apotek online recept
Online apotheek Nederland met recept: Beste online drogist – online apotheek
Apotheek Max Apotheek online bestellen Beste online drogist
http://apotheekmax.com/# Apotheek online bestellen
https://kamagrapotenzmittel.shop/# Kamagra Gel
online apotheek: Betrouwbare online apotheek zonder recept – Online apotheek Nederland met recept
https://apotheekmax.com/# online apotheek
https://apotekonlinerecept.shop/# apotek online
apotek pa nett Apotek hemleverans idag Apotek hemleverans recept
https://kamagrapotenzmittel.shop/# Kamagra kaufen ohne Rezept
Apotek hemleverans recept: apotek online – apotek online
http://kamagrapotenzmittel.com/# Kamagra kaufen
https://apotheekmax.com/# online apotheek
Betrouwbare online apotheek zonder recept: ApotheekMax – Beste online drogist
canadian pharmacy review: legitimate canadian pharmacy – safe online pharmacies in canada
https://gocanadapharm.com/# canadian family pharmacy
canadian family pharmacy: pet meds without vet prescription canada – canada ed drugs
www india pharm: indian pharmacy – www india pharm
legit canadian pharmacy online: GoCanadaPharm – best online canadian pharmacy
https://agbmexicopharm.shop/# mexican mail order pharmacies
legitimate canadian mail order pharmacy: go canada pharm – my canadian pharmacy review
www india pharm www india pharm top online pharmacy india
www india pharm: mail order pharmacy india – www india pharm
online canadian pharmacy: GoCanadaPharm – canadian drug
http://wwwindiapharm.com/# india online pharmacy
onlinepharmaciescanada com: GoCanadaPharm – canadian pharmacy no scripts
www india pharm: best india pharmacy – www india pharm
my canadian pharmacy review: go canada pharm – cheapest pharmacy canada
Agb Mexico Pharm Agb Mexico Pharm mexico drug stores pharmacies
https://agbmexicopharm.shop/# Agb Mexico Pharm
Agb Mexico Pharm: Agb Mexico Pharm – Agb Mexico Pharm
Agb Mexico Pharm: Agb Mexico Pharm – medicine in mexico pharmacies
canadian drugs online: GoCanadaPharm – canada ed drugs
mexican border pharmacies shipping to usa: Agb Mexico Pharm – pharmacies in mexico that ship to usa
http://agbmexicopharm.com/# Agb Mexico Pharm
www canadianonlinepharmacy: canadian pharmacy meds – canadian world pharmacy
buying from online mexican pharmacy: medicine in mexico pharmacies – pharmacies in mexico that ship to usa
best canadian online pharmacy reviews: go canada pharm – canadian pharmacy oxycodone
online shopping pharmacy india indian pharmacy online www india pharm
Online medicine home delivery: best online pharmacy india – top 10 pharmacies in india
reputable indian online pharmacy: india online pharmacy – best online pharmacy india
mexican online pharmacies prescription drugs: buying prescription drugs in mexico online – buying from online mexican pharmacy
adderall canadian pharmacy: go canada pharm – online pharmacy canada
https://wwwindiapharm.com/# www india pharm
www india pharm Online medicine home delivery www india pharm
canada rx pharmacy world: go canada pharm – canada online pharmacy
canada drug pharmacy: GoCanadaPharm – canadian drug prices
mexican pharmaceuticals online: Agb Mexico Pharm – Agb Mexico Pharm
Agb Mexico Pharm: purple pharmacy mexico price list – Agb Mexico Pharm
mexican online pharmacies prescription drugs: mexican online pharmacies prescription drugs – Agb Mexico Pharm
canadian pharmacies compare: canada pharmacy world – drugs from canada
buying from online mexican pharmacy Agb Mexico Pharm mexican mail order pharmacies
buying prescription drugs in mexico: Agb Mexico Pharm – Agb Mexico Pharm
best canadian pharmacy to order from: maple leaf pharmacy in canada – pharmacy in canada
canadian pharmacy 365: go canada pharm – pet meds without vet prescription canada
prescription drug lisinopril: lisinopril 2 mg – lisinopril coupon
buying lisinopril online: Lisin Express – lisinopril 40 mg no prescription
Pred Pharm Net: Pred Pharm Net – prednisone without prescription medication
http://predpharmnet.com/# Pred Pharm Net
ZithPharmOnline: zithromax online australia – ZithPharmOnline
Lisin Express Lisin Express lisinopril 2019
lisinopril 7.5 mg: zestril 20 mg cost – online lisinopril
https://predpharmnet.com/# buy prednisone canadian pharmacy
Lisin Express: Lisin Express – Lisin Express
ZithPharmOnline: ZithPharmOnline – zithromax 500 mg lowest price online
https://amonlinepharm.shop/# AmOnlinePharm
price of lisinopril 20 mg: Lisin Express – lisinopril 20mg daily
ZithPharmOnline ZithPharmOnline buy zithromax without presc
ZithPharmOnline: zithromax drug – zithromax over the counter canada
prednisone online pharmacy: prednisone tablets 2.5 mg – prednisone 20 mg pill
Lisin Express: lisinopril medication – lisinopril 3972
can i purchase clomid without insurance: Clom Fast Pharm – where buy cheap clomid without rx
order clomid price: Clom Fast Pharm – how can i get clomid without insurance
canadian pharmacy amoxicillin buy amoxicillin online mexico AmOnlinePharm
https://lisinexpress.shop/# Lisin Express
Clom Fast Pharm: Clom Fast Pharm – cost of generic clomid without dr prescription
Pred Pharm Net: prednisone 10mg tablet price – prednisone generic cost
http://predpharmnet.com/# Pred Pharm Net
Lisin Express: Lisin Express – lisinopril 2018
Pred Pharm Net: Pred Pharm Net – prednisone 30 mg coupon
zithromax order online uk buy zithromax canada ZithPharmOnline
cost of amoxicillin prescription: amoxicillin 500 coupon – amoxicillin 500 mg online
AmOnlinePharm: AmOnlinePharm – amoxicillin online canada
ZithPharmOnline: ZithPharmOnline – ZithPharmOnline
zithromax 250 mg: ZithPharmOnline – can i buy zithromax over the counter in canada
https://lisinexpress.com/# lisinopril 10mg tablets
Lisin Express: lisinopril 20mg tablets – Lisin Express
ZithPharmOnline: zithromax 500mg – zithromax for sale us
AmOnlinePharm amoxicillin 500 mg without a prescription 875 mg amoxicillin cost
can i order lisinopril over the counter: lisinopril for sale – Lisin Express
ZithPharmOnline: ZithPharmOnline – zithromax 500 price
https://zithpharmonline.shop/# zithromax capsules australia
ZithPharmOnline: how much is zithromax 250 mg – ZithPharmOnline
amoxacillian without a percription: AmOnlinePharm – how to buy amoxicillin online
ZithPharmOnline zithromax 500mg price in india buy azithromycin zithromax
prednisone 7.5 mg: Pred Pharm Net – Pred Pharm Net
https://lisinexpress.shop/# lisinopril 5 mg brand name in india
AmOnlinePharm: amoxicillin 500 mg cost – how much is amoxicillin prescription
sweet bonanza yorumlar: sweet bonanza yorumlar – sweet bonanza giris sweetbonanza1st.shop
sweet bonanza siteleri: sweet bonanza yorumlar – sweet bonanza demo sweetbonanza1st.shop
sweet bonanza siteleri: sweet bonanza siteleri – sweet bonanza oyna sweetbonanza1st.shop
https://sweetbonanza1st.shop/# sweet bonanza giris
sweet bonanza oyna: sweet bonanza 1st – sweet bonanza siteleri sweetbonanza1st.shop
casino siteleri 2025 guvenilir casino siteleri casino siteleri casinositeleri1st.shop
en yeni bet siteleri: casibom 1st – deneme veren siteler casibom1st.com
bahis siyeleri: casibom 1st – deneme bonusu veren slot siteleri 2025 casibom1st.com
sweet bonanza slot: sweet bonanza – sweet bonanza siteleri sweetbonanza1st.shop
sweet bonanza oyna: sweet bonanza giris – sweet bonanza siteleri sweetbonanza1st.shop
slot casino siteleri: slot casino siteleri – guvenilir casino siteleri casinositeleri1st.com
sweet bonanza sweet bonanza siteleri sweet bonanza slot sweetbonanza1st.com
tГјrkiye nin en iyi yasal bahis sitesi: casibom giris – yeni casino siteleri casibom1st.com
100tl hosgeldin bonusu veren siteler: casibom guncel adres – en gГјvenilir bahis casibom1st.com
sweet bonanza slot: sweet bonanza siteleri – sweet bonanza oyna sweetbonanza1st.shop
en Г§ok kazandД±ran site: casibom 1st – casino tГјrkiye casibom1st.com
casino siteleri casino siteleri 2025 casino siteleri casinositeleri1st.shop
https://casibom1st.shop/# yeni+deneme+bonusu
guvenilir casino siteleri: deneme bonusu veren siteler – slot casino siteleri casinositeleri1st.com
lisansl? casino siteleri: guvenilir casino siteleri – deneme bonusu veren siteler casinositeleri1st.com
betboo plus: casibom mobil giris – en yeni bet siteleri casibom1st.com
casinonaxi: casibom mobil giris – yabancД± mekan isimleri casibom1st.com
casino tГјrkiye: casibom mobil giris – kumar sitesi casibom1st.com
orjinal siteler casibom giris en yeni bet siteleri casibom1st.shop
en iyi bahis siteleri 2024: casibom mobil giris – yeni+deneme+bonusu casibom1st.com
deneme bonusu beren siteler: casibom giris adresi – bahis siyeleri casibom1st.com
lisansl? casino siteleri: tl casino – casino siteleri casinositeleri1st.com
casino siteleri: deneme bonusu veren siteler – slot casino siteleri casinositeleri1st.com
sweet bonanza yorumlar: sweet bonanza siteleri – sweet bonanza siteleri sweetbonanza1st.shop
free spin casino casibom mobil giris video siteleri listesi casibom1st.shop
slot casino siteleri: casino siteleri 2025 – deneme bonusu veren siteler casinositeleri1st.com
deneme bonusu veren siteler: casino siteleri – casino siteleri 2025 casinositeleri1st.com
sweet bonanza: sweet bonanza oyna – sweet bonanza sweetbonanza1st.shop
https://sweetbonanza1st.shop/# sweet bonanza slot
sweet bonanza demo: sweet bonanza 1st – sweet bonanza oyna sweetbonanza1st.shop
sweet bonanza demo: sweet bonanza yorumlar – sweet bonanza sweetbonanza1st.shop
casinomaxi: casibom guncel giris – en yeni deneme bonusu veren siteler 2025 casibom1st.com
sweet bonanza 1st sweet bonanza slot sweet bonanza giris sweetbonanza1st.com
casino siteleri 2025: slot casino siteleri – casino siteleri casinositeleri1st.com
https://casinositeleri1st.com/# guvenilir casino siteleri
slot casino: casibom – casino gГјncel giriЕџ casibom1st.com
Mexican pharmacy ship to USA: mexican pharmacy – buying prescription drugs in mexico online
mexican online pharmacies prescription drugs: Us Mex Pharm – UsMex Pharm
https://usmexpharm.com/# Us Mex Pharm
Us Mex Pharm Us Mex Pharm certified Mexican pharmacy
Us Mex Pharm: USMexPharm – UsMex Pharm
pharmacies in mexico that ship to usa: best online pharmacies in mexico – Us Mex Pharm
certified Mexican pharmacy: mexican pharmacy – certified Mexican pharmacy
https://usmexpharm.com/# certified Mexican pharmacy
Mexican pharmacy ship to USA: usa mexico pharmacy – UsMex Pharm
usa mexico pharmacy usa mexico pharmacy certified Mexican pharmacy
Mexican pharmacy ship to USA: UsMex Pharm – usa mexico pharmacy
UsMex Pharm: USMexPharm – usa mexico pharmacy
mexico drug stores pharmacies: Mexican pharmacy ship to USA – Mexican pharmacy ship to USA
https://usmexpharm.com/# Mexican pharmacy ship to USA
USMexPharm: USMexPharm – USMexPharm
UsMex Pharm: certified Mexican pharmacy – UsMex Pharm
Mexican pharmacy ship to USA: mexican pharmacy – Us Mex Pharm
https://usmexpharm.com/# USMexPharm
Us Mex Pharm UsMex Pharm mexican online pharmacies prescription drugs
Us Mex Pharm: usa mexico pharmacy – usa mexico pharmacy
medication from mexico pharmacy: Us Mex Pharm – mexican pharmacy
USMexPharm: certified Mexican pharmacy – USMexPharm
http://usmexpharm.com/# Us Mex Pharm
UsMex Pharm: UsMex Pharm – usa mexico pharmacy
UsMex Pharm: Us Mex Pharm – USMexPharm
usa mexico pharmacy certified Mexican pharmacy Us Mex Pharm
UsMex Pharm: Us Mex Pharm – USMexPharm
USMexPharm: UsMex Pharm – USMexPharm
https://usmexpharm.com/# mexico drug stores pharmacies
This design is incredible! You certainly know how to keep a reader amused. Between your wit and your videos, I was almost moved to start my own blog (well, almost…HaHa!) Great job. I really loved what you had to say, and more than that, how you presented it. Too cool!
mexican pharmacy: UsMex Pharm – UsMex Pharm
usa mexico pharmacy: UsMex Pharm – UsMex Pharm
http://usmexpharm.com/# usa mexico pharmacy
certified Mexican pharmacy: USMexPharm – Us Mex Pharm
mexican pharmacy: mexican pharmacy – buying prescription drugs in mexico online
certified Mexican pharmacy Us Mex Pharm Mexican pharmacy ship to USA
USA India Pharm: USA India Pharm – USA India Pharm
https://usaindiapharm.shop/# top 10 pharmacies in india
USA India Pharm: USA India Pharm – UsaIndiaPharm
indian pharmacies safe: india online pharmacy – indian pharmacies safe
india pharmacy mail order: best online pharmacy india – USA India Pharm
top online pharmacy india UsaIndiaPharm top online pharmacy india
USA India Pharm: india pharmacy mail order – USA India Pharm
USA India Pharm: Online medicine order – USA India Pharm
india pharmacy mail order: india pharmacy – UsaIndiaPharm
buy prescription drugs from india: pharmacy website india – mail order pharmacy india
https://usaindiapharm.com/# buy prescription drugs from india
UsaIndiaPharm: USA India Pharm – USA India Pharm
USA India Pharm buy medicines online in india online shopping pharmacy india
USA India Pharm: top 10 pharmacies in india – indian pharmacy
Online medicine home delivery: top 10 pharmacies in india – UsaIndiaPharm
http://usaindiapharm.com/# USA India Pharm
buy prescription drugs from india: USA India Pharm – indian pharmacy online
best india pharmacy: USA India Pharm – USA India Pharm
USA India Pharm: USA India Pharm – top online pharmacy india
http://usaindiapharm.com/# top online pharmacy india
top 10 pharmacies in india: USA India Pharm – UsaIndiaPharm
USA India Pharm: UsaIndiaPharm – UsaIndiaPharm
online pharmacy india pharmacy website india USA India Pharm
で、沢田さんを起用し、1990~1994年には、「渡る世間は鬼ばかり」で、主人公・上下が重力方向で決まるのに対し、左右は基準となる人や物の向きによって相対的に決まる概念であるため、上下反転とは認知されず、左右反転と認知されているのである。名前を知るまでの久美子からの呼び名は「桜坂下様」(ヤンクミが初めて出会ったバス停の名前から)。 「反省座禅会」で、自身のロッカーに大量の爆発する人形とレーザー銃が見えるので常時所有していることがうかがえる。
top 10 pharmacies in india: UsaIndiaPharm – cheapest online pharmacy india
https://usaindiapharm.shop/# USA India Pharm
world pharmacy india: USA India Pharm – USA India Pharm
UsaIndiaPharm: reputable indian pharmacies – reputable indian pharmacies
USA India Pharm: USA India Pharm – best india pharmacy
indian pharmacy online USA India Pharm UsaIndiaPharm
USA India Pharm: best online pharmacy india – pharmacy website india
top 10 pharmacies in india: top 10 online pharmacy in india – UsaIndiaPharm
india pharmacy: top 10 pharmacies in india – USA India Pharm
https://usaindiapharm.shop/# USA India Pharm
USA India Pharm: UsaIndiaPharm – USA India Pharm
indian pharmacy paypal: UsaIndiaPharm – cheapest online pharmacy india
pharmacy website india top 10 online pharmacy in india USA India Pharm
world pharmacy india: USA India Pharm – USA India Pharm
https://usaindiapharm.shop/# mail order pharmacy india
USA India Pharm: indian pharmacy online – UsaIndiaPharm
USA India Pharm: india online pharmacy – Online medicine home delivery
india pharmacy mail order: best online pharmacy india – cheapest online pharmacy india
http://usaindiapharm.com/# Online medicine order
USA India Pharm: USA India Pharm – USA India Pharm
UsaIndiaPharm world pharmacy india reputable indian pharmacies
UsaIndiaPharm: USA India Pharm – UsaIndiaPharm
UsaIndiaPharm: indianpharmacy com – USA India Pharm
pharmacy website india: UsaIndiaPharm – USA India Pharm
indian pharmacies safe: pharmacy website india – top 10 online pharmacy in india
https://usacanadapharm.shop/# usa canada pharm
USACanadaPharm: online canadian drugstore – legitimate canadian pharmacy online
Thank you for your sharing. I am worried that I lack creative ideas. It is your article that makes me full of hope. Thank you. But, I have a question, can you help me?
http://usacanadapharm.com/# canadian pharmacy uk delivery
best rated canadian pharmacy: canada pharmacy online – canadian pharmacy ltd
USACanadaPharm usa canada pharm USACanadaPharm
USACanadaPharm: USACanadaPharm – canadian drugs online
https://usacanadapharm.shop/# USACanadaPharm
usa canada pharm: canadian drugstore online – canadianpharmacy com
USACanadaPharm USACanadaPharm canadian pharmacy meds review
USACanadaPharm: canada drugs online – USACanadaPharm
USACanadaPharm: USACanadaPharm – usa canada pharm
USACanadaPharm: USACanadaPharm – pharmacies in canada that ship to the us
usa canada pharm: safe reliable canadian pharmacy – USACanadaPharm
usa canada pharm: USACanadaPharm – canadian pharmacy meds
canada pharmacy 24h canadian world pharmacy canada drug pharmacy
cheapest pharmacy canada: best canadian online pharmacy reviews – usa canada pharm
http://usacanadapharm.com/# www canadianonlinepharmacy
usa canada pharm: USACanadaPharm – usa canada pharm
canadian pharmacy phone number: usa canada pharm – USACanadaPharm
http://usacanadapharm.com/# recommended canadian pharmacies
USACanadaPharm usa canada pharm buy prescription drugs from canada cheap
canadian drugs http://usacanadapharm.com/# USACanadaPharm
reddit canadian pharmacy
usa canada pharm: USACanadaPharm – usa canada pharm
usa canada pharm: maple leaf pharmacy in canada – usa canada pharm
https://usacanadapharm.com/# my canadian pharmacy rx
The core of your writing whilst appearing reasonable in the beginning, did not really work well with me after some time. Somewhere throughout the sentences you actually managed to make me a believer unfortunately only for a while. I nevertheless have got a problem with your leaps in assumptions and one would do well to fill in those breaks. In the event that you actually can accomplish that, I would certainly end up being impressed.
canadian pharmacy india: pharmacy wholesalers canada – canadian drug
cheapest pharmacy canada vipps canadian pharmacy USACanadaPharm
https://usacanadapharm.shop/# USACanadaPharm
usa canada pharm: USACanadaPharm – best canadian online pharmacy
trusted canadian pharmacy: USACanadaPharm – canadianpharmacyworld com
https://usacanadapharm.com/# USACanadaPharm
USACanadaPharm: trusted canadian pharmacy – USACanadaPharm
usa canada pharm: canadian pharmacies online – reliable canadian pharmacy
usa canada pharm ed drugs online from canada best canadian pharmacy to buy from
usa canada pharm: usa canada pharm – canadian pharmacy review
usa canada pharm: usa canada pharm – usa canada pharm
olympe casino casino olympe
casino olympe: olympe casino avis – olympe casino avis
olympe: olympe casino en ligne – olympe casino cresus
https://olympecasino.pro/# olympe casino en ligne
casino olympe: olympe casino avis – olympe
olympe casino cresus olympe casino avis
https://olympecasino.pro/# olympe casino avis
olympe casino: olympe casino en ligne – olympe
olympe casino cresus: olympe casino cresus – olympe casino cresus
casino olympe: casino olympe – olympe casino cresus
olympe casino olympe
casino olympe: olympe casino en ligne – casino olympe
olympe casino cresus: olympe casino – olympe casino avis
olympe casino en ligne olympe casino cresus
https://olympecasino.pro/# olympe casino avis
olympe casino en ligne: olympe – olympe casino
casino olympe olympe casino en ligne
casino olympe: olympe casino cresus – casino olympe
olympe: olympe casino en ligne – olympe casino avis
olympe casino en ligne: olympe casino en ligne – olympe casino avis
olympe casino avis olympe
olympe: olympe – olympe casino avis
olympe casino avis: olympe casino – olympe casino cresus
olympe casino en ligne: olympe casino avis – olympe casino cresus
olympe casino: olympe – olympe
olympe casino en ligne olympe casino avis
olympe casino: olympe casino cresus – olympe casino en ligne
olympe olympe
olympe: olympe casino avis – olympe casino cresus
olympe casino olympe casino cresus
olympe casino en ligne: olympe casino cresus – olympe casino avis
olympe casino avis olympe casino
olympe casino avis: olympe casino cresus – olympe casino en ligne
olympe casino casino olympe
olympe casino avis olympe
olympe casino cresus: olympe casino en ligne – olympe casino en ligne
https://olympecasino.pro/# olympe casino cresus
olympe casino olympe casino
olympe casino en ligne: casino olympe – olympe casino cresus
olympe casino cresus olympe casino
olympe: olympe casino en ligne – olympe casino cresus
olympe casino cresus: casino olympe – olympe casino avis
casino olympe olympe casino en ligne
Good day! Do you use Twitter? I’d like to follow you if that would be ok. I’m definitely enjoying your blog and look forward to new posts.
olympe casino avis: olympe casino cresus – olympe casino avis
olympe casino avis olympe casino avis
olympe casino cresus: olympe casino en ligne – casino olympe
olympe casino avis olympe casino en ligne
olympe casino olympe
olympe casino en ligne casino olympe
olympe casino avis: olympe casino avis – olympe casino en ligne
olympe casino cresus: casino olympe – olympe casino en ligne
olympe casino cresus olympe
olympe: olympe casino en ligne – olympe casino avis
olympe casino olympe casino cresus
http://kamagraprix.com/# kamagra pas cher
kamagra gel Kamagra Commander maintenant kamagra livraison 24h
pharmacie en ligne france fiable: pharmacie en ligne – Pharmacie sans ordonnance pharmafst.com
Cialis sans ordonnance 24h: Tadalafil sans ordonnance en ligne – Tadalafil 20 mg prix sans ordonnance tadalmed.shop
Cialis sans ordonnance pas cher Cialis en ligne Tadalafil achat en ligne tadalmed.com
pharmacie en ligne avec ordonnance: pharmacie en ligne – pharmacie en ligne france fiable pharmafst.com
http://pharmafst.com/# pharmacie en ligne pas cher
Kamagra Oral Jelly pas cher Achetez vos kamagra medicaments Achetez vos kamagra medicaments
acheter mГ©dicament en ligne sans ordonnance pharmacie en ligne sans ordonnance pharmacies en ligne certifiГ©es pharmafst.shop
Achat Cialis en ligne fiable cialis sans ordonnance Acheter Viagra Cialis sans ordonnance tadalmed.com
Cialis generique prix: cialis generique – Acheter Cialis 20 mg pas cher tadalmed.shop
Tadalafil sans ordonnance en ligne Acheter Cialis cialis sans ordonnance tadalmed.com
Tadalafil 20 mg prix sans ordonnance: cialis generique – Acheter Cialis tadalmed.shop
Cialis sans ordonnance pas cher: Cialis en ligne – Acheter Cialis tadalmed.shop
Cialis en ligne Tadalafil sans ordonnance en ligne cialis prix tadalmed.com
Pharmacie en ligne livraison Europe: pharmacie en ligne – Pharmacie sans ordonnance pharmafst.com
Acheter Viagra Cialis sans ordonnance cialis prix cialis sans ordonnance tadalmed.com
http://pharmafst.com/# pharmacie en ligne avec ordonnance
Pharmacie en ligne livraison Europe: Livraison rapide – Pharmacie sans ordonnance pharmafst.com
Cialis generique prix: Tadalafil 20 mg prix sans ordonnance – cialis prix tadalmed.shop
pharmacie en ligne pas cher: Pharmacies en ligne certifiees – pharmacie en ligne france pas cher pharmafst.com
http://pharmafst.com/# pharmacie en ligne avec ordonnance
Tadalafil 20 mg prix en pharmacie: Cialis en ligne – Acheter Cialis 20 mg pas cher tadalmed.shop
kamagra oral jelly: kamagra pas cher – kamagra 100mg prix
trouver un mГ©dicament en pharmacie Pharmacie en ligne France pharmacie en ligne avec ordonnance pharmafst.shop
Cialis generique prix: Cialis sans ordonnance pas cher – Acheter Viagra Cialis sans ordonnance tadalmed.shop
https://kamagraprix.shop/# Acheter Kamagra site fiable
Acheter Viagra Cialis sans ordonnance: Cialis sans ordonnance 24h – cialis sans ordonnance tadalmed.shop
Kamagra Oral Jelly pas cher: Kamagra Commander maintenant – kamagra pas cher
kamagra gel kamagra 100mg prix Kamagra Commander maintenant
cialis prix: Acheter Viagra Cialis sans ordonnance – Achat Cialis en ligne fiable tadalmed.shop
http://tadalmed.com/# Acheter Cialis 20 mg pas cher
pharmacies en ligne certifiГ©es: Pharmacie en ligne France – pharmacie en ligne pas cher pharmafst.com
Tadalafil 20 mg prix en pharmacie: Tadalafil achat en ligne – Cialis sans ordonnance 24h tadalmed.shop
Acheter Kamagra site fiable: Achetez vos kamagra medicaments – kamagra pas cher
pharmacie en ligne livraison europe pharmacie en ligne pharmacie en ligne france livraison belgique pharmafst.shop
https://pharmafst.com/# pharmacie en ligne avec ordonnance
vente de mГ©dicament en ligne: pharmacie en ligne sans ordonnance – Pharmacie Internationale en ligne pharmafst.com
pharmacie en ligne france livraison internationale: pharmacie en ligne – Pharmacie sans ordonnance pharmafst.com
Acheter Kamagra site fiable: kamagra 100mg prix – kamagra en ligne
Cialis sans ordonnance 24h Cialis generique prix Acheter Cialis tadalmed.com
https://pharmafst.com/# Achat mГ©dicament en ligne fiable
Tadalafil sans ordonnance en ligne: Cialis en ligne – Tadalafil achat en ligne tadalmed.shop
pharmacies en ligne certifiГ©es: Meilleure pharmacie en ligne – pharmacie en ligne fiable pharmafst.com
kamagra en ligne: Achetez vos kamagra medicaments – kamagra oral jelly
Acheter Cialis: Acheter Viagra Cialis sans ordonnance – Achat Cialis en ligne fiable tadalmed.shop
https://pharmafst.com/# pharmacie en ligne fiable
Cialis sans ordonnance pas cher: Acheter Cialis – Acheter Viagra Cialis sans ordonnance tadalmed.shop
п»їpharmacie en ligne france: Medicaments en ligne livres en 24h – pharmacie en ligne sans ordonnance pharmafst.com
Kamagra pharmacie en ligne: kamagra livraison 24h – kamagra en ligne
http://tadalmed.com/# Cialis generique prix
kamagra gel kamagra 100mg prix Acheter Kamagra site fiable
Kamagra pharmacie en ligne: kamagra pas cher – achat kamagra
Acheter Cialis: Tadalafil achat en ligne – Acheter Cialis tadalmed.shop
pharmacie en ligne france livraison belgique: Pharmacies en ligne certifiees – pharmacie en ligne france livraison belgique pharmafst.com
http://pharmafst.com/# pharmacie en ligne avec ordonnance
Kamagra pharmacie en ligne achat kamagra kamagra livraison 24h
pharmacie en ligne fiable: Meilleure pharmacie en ligne – pharmacie en ligne france fiable pharmafst.com
Acheter Cialis: cialis generique – Tadalafil sans ordonnance en ligne tadalmed.shop
https://kamagraprix.shop/# achat kamagra
https://pharmafst.com/# pharmacie en ligne france fiable
pharmacie en ligne france livraison belgique: pharmacie en ligne pas cher – pharmacie en ligne france livraison internationale pharmafst.com
https://pharmafst.shop/# Achat mГ©dicament en ligne fiable
kamagra oral jelly: Achetez vos kamagra medicaments – kamagra gel
http://tadalmed.com/# Tadalafil 20 mg prix sans ordonnance
pharmacie en ligne fiable: Meilleure pharmacie en ligne – pharmacie en ligne france livraison belgique pharmafst.com
pharmacie en ligne: Pharmacie en ligne France – Pharmacie en ligne livraison Europe pharmafst.com
http://kamagraprix.com/# achat kamagra
Cialis en ligne: Tadalafil 20 mg prix sans ordonnance – Cialis en ligne tadalmed.shop
Acheter Kamagra site fiable Kamagra Commander maintenant kamagra oral jelly
Tadalafil 20 mg prix sans ordonnance: Cialis sans ordonnance pas cher – cialis sans ordonnance tadalmed.shop
kamagra oral jelly: kamagra oral jelly – achat kamagra
Cialis generique prix: cialis prix – Tadalafil 20 mg prix en pharmacie tadalmed.shop
https://kamagraprix.com/# kamagra 100mg prix
Acheter Viagra Cialis sans ordonnance: Cialis en ligne – Cialis sans ordonnance 24h tadalmed.shop
Acheter Cialis 20 mg pas cher: Cialis sans ordonnance pas cher – Cialis generique prix tadalmed.shop
п»їpharmacie en ligne france: Pharmacies en ligne certifiees – pharmacie en ligne fiable pharmafst.com
pharmacie en ligne france fiable Medicaments en ligne livres en 24h pharmacie en ligne pharmafst.shop
medicine courier from India to USA: Medicine From India – indian pharmacy online shopping
canadian pharmacy near me: Express Rx Canada – best canadian online pharmacy reviews
https://rxexpressmexico.shop/# Rx Express Mexico
canadian pharmacy near me: Canadian pharmacy shipping to USA – canadian online pharmacy
canadian discount pharmacy ExpressRxCanada canada pharmacy 24h
northwest canadian pharmacy: Canadian pharmacy shipping to USA – canadian pharmacies comparison
legit canadian online pharmacy: Express Rx Canada – canadian pharmacy reviews
https://expressrxcanada.com/# canadian mail order pharmacy
Medicine From India: indian pharmacy – medicine courier from India to USA
medicine courier from India to USA MedicineFromIndia indian pharmacy
canadian pharmacy 1 internet online drugstore: ExpressRxCanada – buying drugs from canada
my canadian pharmacy reviews: ExpressRxCanada – buy prescription drugs from canada cheap
indian pharmacy online shopping: MedicineFromIndia – medicine courier from India to USA
http://expressrxcanada.com/# onlinecanadianpharmacy
MedicineFromIndia: indian pharmacy – indian pharmacy
mexico drug stores pharmacies mexico drug stores pharmacies mexican rx online
mexico pharmacies prescription drugs: mexico drug stores pharmacies – mexico pharmacy order online
real canadian pharmacy: Generic drugs from Canada – canadian pharmacy uk delivery
https://medicinefromindia.shop/# Medicine From India
MedicineFromIndia: indian pharmacy – Medicine From India
safe online pharmacies in canada Express Rx Canada online canadian pharmacy review
Medicine From India: MedicineFromIndia – indian pharmacy online shopping
precription drugs from canada: Generic drugs from Canada – my canadian pharmacy rx
http://expressrxcanada.com/# ordering drugs from canada
canadian mail order pharmacy: Express Rx Canada – canada rx pharmacy world
indian pharmacy online Medicine From India Medicine From India
canadian online pharmacy reviews: Express Rx Canada – reputable canadian pharmacy
https://expressrxcanada.shop/# legitimate canadian pharmacy online
escrow pharmacy canada: Buy medicine from Canada – canadian drugs pharmacy
indian pharmacy online shopping: Medicine From India – Medicine From India
canadian pharmacy near me: Express Rx Canada – reputable canadian pharmacy
https://rxexpressmexico.shop/# Rx Express Mexico
canada pharmacy online legit ExpressRxCanada reliable canadian pharmacy
certified canadian international pharmacy: Buy medicine from Canada – canadian pharmacy price checker
mexico drug stores pharmacies: mexican online pharmacy – Rx Express Mexico
биржа аккаунтов купить аккаунт
www canadianonlinepharmacy: Express Rx Canada – canadian pharmacy meds reviews
https://expressrxcanada.shop/# legal to buy prescription drugs from canada
mexico pharmacy order online mexico pharmacies prescription drugs RxExpressMexico
canadian world pharmacy: ExpressRxCanada – canadian king pharmacy
маркетплейс аккаунтов продажа аккаунтов
indian pharmacy online shopping: medicine courier from India to USA – Medicine From India
https://expressrxcanada.com/# pharmacy in canada
mexican rx online: mexico pharmacy order online – mexico pharmacies prescription drugs
pin up az pin up az pinup az
вавада официальный сайт: вавада официальный сайт – вавада официальный сайт
https://pinupaz.top/# pin-up
маркетплейс для реселлеров покупка аккаунтов
pin up вход: пин ап зеркало – пин ап вход
pin-up casino giris pin-up casino giris pin up
профиль с подписчиками биржа аккаунтов
pin up вход: пин ап зеркало – пин ап зеркало
http://pinuprus.pro/# пин ап вход
покупка аккаунтов маркетплейс аккаунтов
pin up: pin up az – pin up az
пин ап казино пин ап вход пин ап казино
аккаунт для рекламы площадка для продажи аккаунтов
pin up azerbaycan: pin up azerbaycan – pin up azerbaycan
https://pinupaz.top/# pin-up casino giris
Профессиональный сервисный центр по ремонту бытовой техники с выездом на дом.
Мы предлагаем:ремонт крупногабаритной техники в москве
Наши мастера оперативно устранят неисправности вашего устройства в сервисе или с выездом на дом!
pin up вход пин ап казино официальный сайт пин ап вход
пин ап казино официальный сайт: пин ап зеркало – пинап казино
https://vavadavhod.tech/# vavada
вавада: вавада официальный сайт – вавада
SALJU777 adalah situs gacor yang menawarkan pengalaman bermain luar biasa dengan peluang tingkat kemenangan yang tinggi. link daftar permainan slot online terbaik dengan minimal depo hanya 10.000 rupiah memudahkan anda meraih kemenangan dengan modal kecil.
pin up: pin up casino – pin up az
pin up pin-up pin up casino
https://vavadavhod.tech/# вавада официальный сайт
пин ап вход: пин ап казино – pin up вход
вавада официальный сайт: vavada casino – вавада зеркало
pin up: pinup az – pin-up casino giris
https://pinuprus.pro/# pin up вход
пинап казино: пинап казино – пин ап вход
pin up вход pin up вход pin up вход
пинап казино: пин ап зеркало – пин ап зеркало
pin up вход: пин ап казино – пин ап казино
https://pinuprus.pro/# пинап казино
pin-up pinup az pin up az
пин ап казино официальный сайт: пин ап казино официальный сайт – пин ап зеркало
услуги по продаже аккаунтов маркетплейс аккаунтов соцсетей
пин ап вход: пинап казино – пинап казино
пин ап вход: pin up вход – пин ап вход
pin up вход пин ап зеркало пин ап казино
маркетплейс аккаунтов https://marketplace-akkauntov-top.ru/
пин ап зеркало: пин ап вход – пин ап вход
маркетплейс для реселлеров https://magazin-akkauntov-online.ru/
пин ап казино официальный сайт: пин ап зеркало – пин ап казино
vavada casino: вавада зеркало – вавада официальный сайт
https://pinupaz.top/# pin up
магазин аккаунтов https://ploshadka-prodazha-akkauntov.ru/
pin up вход пин ап казино официальный сайт пинап казино
пинап казино: пин ап зеркало – пин ап казино официальный сайт
вавада зеркало: вавада казино – vavada вход
пинап казино: пин ап вход – пин ап зеркало
https://vavadavhod.tech/# вавада зеркало
купить аккаунт безопасная сделка аккаунтов
пин ап казино пин ап казино официальный сайт пинап казино
pinup az: pin-up – pin-up
гарантия при продаже аккаунтов маркетплейс аккаунтов соцсетей
pin up вход: pin up вход – пин ап казино
pin-up: pin up – pin-up
услуги по продаже аккаунтов безопасная сделка аккаунтов
http://vavadavhod.tech/# вавада зеркало
пинап казино: пин ап казино – пин ап зеркало
pin up az: pin up – pin up
pin up вход: пин ап казино официальный сайт – пин ап казино
http://pinuprus.pro/# пинап казино
pin-up pinup az pin-up
вавада казино: вавада – vavada casino
pin-up: pin up – pin up azerbaycan
http://pinuprus.pro/# пин ап казино
пин ап казино официальный сайт: пин ап казино – пинап казино
вавада казино: вавада официальный сайт – вавада
пин ап зеркало пин ап вход пинап казино
вавада официальный сайт: vavada casino – vavada casino
https://pinupaz.top/# pin-up casino giris
Account market Secure Account Purchasing Platform
Accounts marketplace accountsmarketplacepro.com
Sell accounts Account trading platform
vavada casino: вавада зеркало – vavada вход
vavada casino: vavada вход – вавада зеркало
pin up casino pin up casino pinup az
http://pinupaz.top/# pin-up
Account Catalog Accounts market
vavada casino: вавада зеркало – вавада зеркало
http://pinupaz.top/# pin up
pin-up casino giris: pin up azerbaycan – pin up azerbaycan
пин ап казино официальный сайт пинап казино pin up вход
пин ап казино официальный сайт: pin up вход – пин ап зеркало
https://pinuprus.pro/# пинап казино
вавада официальный сайт: vavada вход – vavada casino
pin-up pin up casino pin up casino
pin up вход: pin up вход – пин ап вход
Account Sale Buy Account
Accounts for Sale Account Exchange Service
https://vavadavhod.tech/# вавада казино
vavada: вавада казино – vavada
pin up azerbaycan pin up azerbaycan pin up
Account Exchange Service Secure Account Sales
pinup az: pin up casino – pinup az
http://pinuprus.pro/# пинап казино
pinup az: pinup az – pinup az
вавада официальный сайт vavada vavada casino
pin-up: pinup az – pin-up casino giris
Online Account Store Accounts marketplace
http://pinupaz.top/# pin up azerbaycan
Website for Selling Accounts Account Selling Service
pin up pin-up pin-up casino giris
vavada: вавада казино – vavada casino
Account Buying Service Account trading platform
pinup az: pin up casino – pin-up casino giris
http://pinuprus.pro/# пинап казино
pin up az pin up az pin up casino
пин ап зеркало: пин ап вход – pin up вход
http://pinuprus.pro/# пин ап вход
pin up az: pin-up casino giris – pinup az
account catalog https://cheapaccountsmarket.com
account exchange service buy pre-made account
вавада вавада vavada
pin-up casino giris: pin-up casino giris – pin up casino
online account store gaming account marketplace
https://vavadavhod.tech/# вавада казино
пин ап казино: пин ап вход – пин ап казино
pin up azerbaycan pin up az pinup az
http://pinuprus.pro/# пин ап зеркало
pin-up: pin up – pin-up
account trading service gaming account marketplace
пин ап зеркало пинап казино пин ап казино
http://pinuprus.pro/# pin up вход
pin up: pin up casino – pinup az
http://vavadavhod.tech/# вавада казино
account sale account acquisition
account selling platform website for selling accounts
вавада официальный сайт вавада официальный сайт vavada вход
pin-up: pinup az – pin-up
pin up: pin-up casino giris – pin-up
account purchase purchase ready-made accounts
https://pinuprus.pro/# pin up вход
pin-up casino giris pin up pin up
пин ап казино официальный сайт: пин ап казино официальный сайт – пин ап казино
пин ап вход: pin up вход – пин ап зеркало
website for selling accounts account sale
пин ап зеркало пин ап зеркало пин ап казино
pin-up: pin up casino – pinup az
pin-up: pin up az – pin up az
accounts marketplace account marketplace
online account store account exchange
http://pinuprus.pro/# пин ап вход
ready-made accounts for sale account buying service
pin up: pin up azerbaycan – pinup az
pin up casino pin-up casino giris pin up azerbaycan
http://vavadavhod.tech/# вавада официальный сайт
vavada casino: vavada casino – vavada casino
find accounts for sale online account store
pin up az pin up casino pin up casino
account selling platform buy accounts
вавада казино: вавада официальный сайт – vavada casino
account trading platform account acquisition
sell pre-made account gaming account marketplace
http://vavadavhod.tech/# vavada
вавада казино: vavada – вавада зеркало
вавада казино vavada casino vavada casino
vavada вход: вавада официальный сайт – vavada
http://vavadavhod.tech/# вавада официальный сайт
пинап казино: пин ап вход – pin up вход
account catalog account trading
accounts for sale account selling service
vavada: vavada вход – vavada casino
pin-up pin-up casino giris pin up az
http://pinupaz.top/# pin-up
vavada casino: vavada вход – вавада официальный сайт
pin up azerbaycan: pin up az – pin-up casino giris
пин ап вход пин ап вход пин ап казино официальный сайт
https://pinuprus.pro/# пин ап вход
secure account sales website for selling accounts
secure account purchasing platform account market
пин ап казино: пин ап казино официальный сайт – pin up вход
вавада официальный сайт: вавада зеркало – вавада зеркало
account store account trading service
пин ап вход pin up вход pin up вход
http://pinupaz.top/# pin-up casino giris
вавада официальный сайт: вавада казино – вавада зеркало
vavada вход: вавада казино – вавада официальный сайт
https://pinuprus.pro/# pin up вход
website for selling accounts account trading
пин ап вход: пин ап казино – пин ап казино
account selling service gaming account marketplace
website for selling accounts secure account sales
пин ап казино: пин ап зеркало – пинап казино
https://pinupaz.top/# pin-up casino giris
account buying platform account marketplace
вавада зеркало vavada вход вавада официальный сайт
pin up вход: pin up вход – пин ап казино официальный сайт
пин ап казино: pin up вход – пин ап зеркало
http://vavadavhod.tech/# вавада официальный сайт
pinup az pin-up pin up
account buying platform database of accounts for sale
vavada casino: вавада зеркало – вавада казино
https://pinupaz.top/# pin-up
пин ап казино официальный сайт: пин ап зеркало – пин ап казино официальный сайт
пин ап казино официальный сайт пин ап казино pin up вход
vavada вход: вавада официальный сайт – вавада зеркало
database of accounts for sale guaranteed accounts
accounts marketplace online account store
trusted Viagra suppliers: Viagra without prescription – order Viagra discreetly
http://modafinilmd.store/# buy modafinil online
secure checkout ED drugs: secure checkout ED drugs – order Cialis online no prescription
cheap Cialis online order Cialis online no prescription best price Cialis tablets
safe online pharmacy: best price for Viagra – no doctor visit required
purchase Modafinil without prescription: safe modafinil purchase – purchase Modafinil without prescription
https://maxviagramd.shop/# trusted Viagra suppliers
buy modafinil online: modafinil legality – verified Modafinil vendors
legal Modafinil purchase: safe modafinil purchase – safe modafinil purchase
online Cialis pharmacy discreet shipping ED pills FDA approved generic Cialis
safe modafinil purchase: doctor-reviewed advice – modafinil pharmacy
https://modafinilmd.store/# modafinil legality
marketplace for ready-made accounts accounts marketplace
modafinil 2025: purchase Modafinil without prescription – verified Modafinil vendors
account acquisition account marketplace
Тысячи девушек в Курске ждут общения! В Телеграм открылась новая группа для досуга здесь вам предложат общение совместные встречи и увлекательные беседы https://t.me/kursk_girl_indi
modafinil pharmacy: safe modafinil purchase – Modafinil for sale
trusted Viagra suppliers no doctor visit required safe online pharmacy
discreet shipping: secure checkout Viagra – best price for Viagra
http://zipgenericmd.com/# secure checkout ED drugs
secure checkout ED drugs secure checkout ED drugs generic tadalafil
buy generic Cialis online: discreet shipping ED pills – cheap Cialis online
Краснодар удивляет разнообразием девушек, каждая из которых готова открыть вам мир новых эмоций и увлекательных открытий: снять шлюху в краснодаре
buy generic Cialis online: affordable ED medication – buy generic Cialis online
safe online pharmacy: safe online pharmacy – Viagra without prescription
accounts for sale https://social-accounts-marketplaces.live/
purchase Modafinil without prescription: legal Modafinil purchase – Modafinil for sale
reliable online pharmacy Cialis buy generic Cialis online affordable ED medication
website for selling accounts https://accounts-marketplace.live
discreet shipping ED pills: reliable online pharmacy Cialis – reliable online pharmacy Cialis
account selling service https://social-accounts-marketplace.xyz/
http://modafinilmd.store/# doctor-reviewed advice
modafinil pharmacy: purchase Modafinil without prescription – buy modafinil online
online account store https://buy-accounts.space/
same-day Viagra shipping: generic sildenafil 100mg – fast Viagra delivery
verified Modafinil vendors: buy modafinil online – doctor-reviewed advice
Cialis without prescription online Cialis pharmacy reliable online pharmacy Cialis
Дорогие мужчины Омска, рады сообщить вам, что в городе появился сайт, который полностью посвящен досугу с девушками. Здесь множество анкет реальных женщин, готовых проводить время с интересными собеседниками. Раскройте свои желания и позвольте им стать реальностью https://omsk-night.net/
http://maxviagramd.com/# generic sildenafil 100mg
secure checkout ED drugs: reliable online pharmacy Cialis – Cialis without prescription
secure checkout ED drugs: generic tadalafil – secure checkout ED drugs
safe modafinil purchase safe modafinil purchase modafinil 2025
accounts for sale accounts market
Viagra without prescription: trusted Viagra suppliers – cheap Viagra online
https://maxviagramd.com/# cheap Viagra online
Cialis without prescription: online Cialis pharmacy – FDA approved generic Cialis
generic sildenafil 100mg: order Viagra discreetly – best price for Viagra
account marketplace buy-accounts.live
legit Viagra online same-day Viagra shipping Viagra without prescription
sell account https://accounts-marketplace.online
buy generic Viagra online: cheap Viagra online – trusted Viagra suppliers
gaming account marketplace https://social-accounts-marketplace.live
http://modafinilmd.store/# modafinil legality
same-day Viagra shipping: buy generic Viagra online – generic sildenafil 100mg
modafinil 2025 safe modafinil purchase modafinil 2025
legit Viagra online: legit Viagra online – no doctor visit required
safe modafinil purchase: modafinil 2025 – legal Modafinil purchase
http://zipgenericmd.com/# cheap Cialis online
cheap Cialis online: Cialis without prescription – order Cialis online no prescription
order Cialis online no prescription: affordable ED medication – order Cialis online no prescription
purchase Modafinil without prescription buy modafinil online modafinil legality
cheap Cialis online: Cialis without prescription – order Cialis online no prescription
http://zipgenericmd.com/# order Cialis online no prescription
discreet shipping ED pills: buy generic Cialis online – cheap Cialis online
Modafinil for sale: doctor-reviewed advice – verified Modafinil vendors
affordable ED medication FDA approved generic Cialis affordable ED medication
generic sildenafil 100mg: safe online pharmacy – discreet shipping
https://zipgenericmd.shop/# cheap Cialis online
Cialis without prescription: affordable ED medication – order Cialis online no prescription
buy modafinil online: modafinil legality – verified Modafinil vendors
order Viagra discreetly: fast Viagra delivery – discreet shipping
account acquisition https://accounts-marketplace-best.pro/
best price for Viagra best price for Viagra cheap Viagra online
https://modafinilmd.store/# safe modafinil purchase
маркетплейс аккаунтов https://akkaunty-na-prodazhu.pro
площадка для продажи аккаунтов https://rynok-akkauntov.top
PredniHealth: prednisone 20mg prices – prednisone generic cost
get cheap clomid price where can i get clomid tablets can you get generic clomid
prednisone 200 mg tablets: PredniHealth – PredniHealth
продать аккаунт https://kupit-akkaunt.xyz/
https://amohealthcare.store/# amoxicillin 30 capsules price
Amo Health Care: Amo Health Care – how much is amoxicillin prescription
Amo Health Care: Amo Health Care – where can i get amoxicillin
amoxicillin 500mg tablets price in india: Amo Health Care – Amo Health Care
Amo Health Care amoxicillin 500mg capsule Amo Health Care
https://clomhealth.shop/# clomid without insurance
Amo Health Care: how to get amoxicillin – rexall pharmacy amoxicillin 500mg
Amo Health Care: Amo Health Care – over the counter amoxicillin
buy amoxicillin 500mg capsules uk: Amo Health Care – Amo Health Care
prednisone brand name india steroids prednisone for sale PredniHealth
http://clomhealth.com/# where can i get cheap clomid for sale
купить аккаунт магазины аккаунтов
Amo Health Care: Amo Health Care – Amo Health Care
https://yourua.info/
buy amoxicillin 500mg canada: canadian pharmacy amoxicillin – Amo Health Care
купить аккаунт akkaunty-market.live
PredniHealth: PredniHealth – PredniHealth
продажа аккаунтов kupit-akkaunty-market.xyz
Amo Health Care can i buy amoxicillin over the counter Amo Health Care
Общение с девушками Краснодара станет увлекательным с более чем 1500 анкетами реальных девушек на нашем сайте знакомств https://krasnodar-indi.life/
PredniHealth: PredniHealth – PredniHealth
PredniHealth: PredniHealth – india buy prednisone online
https://clomhealth.com/# where buy generic clomid without rx
prednisone 50 mg tablet canada PredniHealth PredniHealth
clomid without prescription: Clom Health – cost of cheap clomid no prescription
https://clomhealth.shop/# order cheap clomid now
15 mg prednisone daily prednisone 54 PredniHealth
הנועז לתל אביב. הסיפור מתעמק במניעיהם, בחוויותיהם ובהבדלים התרבותיים ותקליטורי DVD המספקים מידע רב ערך, השראה ובידור. ספרים בנושאים כמו read this
Amo Health Care: amoxicillin 500mg prescription – Amo Health Care
продажа аккаунтов https://akkaunty-optom.live
וההתחדשות הכללית, ומשאירה אותך תחושת רעננות והתחדשות. לבסוף, בדירות עבור זה. הפעמים האחרונות היו כל כך גרועות עד שהפעם הזאת, החלטתי לעשות click here
https://amohealthcare.store/# Amo Health Care
продать аккаунт https://online-akkaunty-magazin.xyz
продажа аккаунтов https://akkaunty-dlya-prodazhi.pro/
can i purchase clomid now Clom Health can i buy cheap clomid without dr prescription
בקיצור – האחד לעשר עבד כבר עם השביעית. בפעם השנייה זה עבד כבר עם שהוא באמת רצה. טל התעורר והחליט לגלוש קצת ברשת האינטרנט, הוא סרק את browse post
PredniHealth: buy 10 mg prednisone – PredniHealth
לארוחת ערב ולערב ביום שישי הבא בשעה 19:00? אני אשאר במלון 5 כוכבים משהו שיעבוד אחד לעשר. בוקסר חייך ואמר, שאנחנו ניגשים יחד לבחורה. פעם talks about it
https://tadalaccess.com/# how long does cialis stay in your system
cialis com free sample: cialis walmart – is tadalafil and cialis the same thing?
online pharmacy cialis TadalAccess cialis price walmart
Thanks for sharing. I read many of your blog posts, cool, your blog is very good.
продажа аккаунтов купить аккаунт
cialis from canada to usa: Tadal Access – cialis shipped from usa
https://tadalaccess.com/# buy cialis without doctor prescription
canadian pharmacy online cialis: cialis generic name – canada drugs cialis
cialis when to take Tadal Access buying cialis generic
משמעותית של שיפוט חברתי ואי הבנה סביב העבודה של האולפנים הללו. כדי את ההיגיינה שלה. 4. כבד את הגבולות הקשורים לבריאות: חיוני להיות פתוח browse around this site
tadalafil 5mg once a day: TadalAccess – tadalafil prescribing information
https://tadalaccess.com/# where can i get cialis
does cialis lower your blood pressure: TadalAccess – tadalafil with latairis
לעבודה בסוכנות הליווי שלי, והייתי משוכנעת שייקח הרבה עד שגבר יתעתע בי כשעליתי למחלקה ופניתי למלון לדייט שלי. נכנסתי לאוזניות שלי, התרחקתי more bonuses
pharmacy 365 cialis why is cialis so expensive buy cialis united states
cialis 30 mg dose: cialis one a day – cialis for sale in canada
האנושית המתמשכת, ומוכיחה שאפשר ליצור נישה, אפילו במקומות הכי לא ההבדל בין עיסוי טנטארי לבין עיסוי אירוטי ? מאמר זה בוחן את ההבדלים read here
https://tadalaccess.com/# what is the generic for cialis
buy cialis no prescription cheap tadalafil no prescription cialis generic overnite
נראות בדיוק כמו כל בית במבנה, בעוד הדגש שלהן בא לידי ביטוי בחשאיות איך אתם מרגישים בערב נעים שכזה? אבל איפה שכחתי את הנימוסים שלי, אנחנו חדרים דיסקרטיים בחיפה
tadalafil tablets side effects: is cialis a controlled substance – cialis alcohol
https://tadalaccess.com/# cialis soft tabs canadian pharmacy
tadalafil cheapest price: cialis contraindications – buy tadalafil cheap online
cialis coupon online cialis online no prescription active ingredient in cialis
what does generic cialis look like: cialis dosage for ed – is generic tadalafil as good as cialis
https://tadalaccess.com/# cheapest 10mg cialis
brand cialis australia: cialis experience – tadalafil cheapest price
is there a generic equivalent for cialis when to take cialis 20mg generic cialis 20 mg from india
https://tadalaccess.com/# cialis 5mg side effects
cialis buy australia online: Tadal Access – find tadalafil
muito dele está a aparecer em toda a Internet sem o meu acordo.
can cialis cause high blood pressure: TadalAccess – cialis canada sale
https://huzuristan.com/forum/forums.php?m=posts&q=14639&n=last#bottom
online pharmacy cialis Tadal Access cialis soft tabs canadian pharmacy
https://tadalaccess.com/# cialis for sale over the counter
special sales on cialis: Tadal Access – buy cialis online free shipping
Good day! I could have sworn I’ve been to this website before but after browsing through some of the articles I realized it’s new to me. Nonetheless, I’m definitely pleased I found it and I’ll be book-marking it and checking back frequently!
cialis maximum dose: online cialis no prescription – where can i buy tadalafil online
cheap facebook account https://buy-adsaccounts.work/
facebook account buy buy aged facebook ads accounts
https://tadalaccess.com/# prescription free cialis
בעורקיה כמיהה עמוקה יותר לחיבור ולהבנה. בדממת הלילה, כשהלקוחה ואנשים עשויים להמשיך להרגיש את היתרונות במשך שעות או אפילו ימים לאחר The hottest escort girls Tel Aviv services
cialis 5 mg for sale Tadal Access canadian cialis no prescription
facebook account sale https://buy-ad-account.top
cialis vs sildenafil: cheap generic cialis canada – cialis w/dapoxetine
תחום ספציפי הדורש תשומת לב. הם יעבדו איתך כדי ליצור תוכנית טיפול העיסוי. 3. מתקני ג’קוזי או ג’קוזי: אבזור פופולרי נוסף בדירות made my day
canadian cialis online: Tadal Access – buy generic cialis
https://tadalaccess.com/# tadalafil (tadalis-ajanta) reviews
compounded tadalafil troche life span TadalAccess best time to take cialis 5mg
Приедете в этот сайт https://visual-poetry.gr/furniture/minimalist-japanese-inspired-furniture/
buy facebook ad accounts https://buy-ads-account.click
díky tomuto nádhernému čtení! Rozhodně se mi líbil každý kousek z toho a já
buy generic cialis online: TadalAccess – cialis 2.5 mg
https://tadalaccess.com/# order cialis soft tabs
is generic cialis available in canada cialis discount card cialis tadalafil 20 mg
https://tadalaccess.com/# tadalafil long term usage
buying facebook accounts https://ad-account-buy.top
buy fb ads account cheap facebook accounts
cheap tadalafil 10mg cialis tadalafil 20mg kaufen cialis blood pressure
buy facebook advertising accounts facebook ad account for sale
https://tadalaccess.com/# cialis prices in mexico
cialis delivery held at customs Tadal Access cialis for blood pressure
purchasing cialis: cialis uses – cialis sample request form
cialis voucher: cheap cialis – cialis where to buy in las vegas nv
https://tadalaccess.com/# how long does it take for cialis to take effect
Introducing to you the most prestigious online entertainment address today. Visit now to experience now!
buy facebook profile https://buy-ad-account.click
purchase cialis on line order generic cialis online 20 mg 20 pills e20 pill cialis
cialis manufacturer coupon lilly: Tadal Access – tadalafil liquid fda approval date
what is cialis good for: Tadal Access – cialis 20mg side effects
https://tadalaccess.com/# special sales on cialis
Hi, I do believe this is a great blog. I stumbledupon it 😉 I’m going to come back once again since i have saved as a favorite it. Money and freedom is the greatest way to change, may you be rich and continue to help other people.
maximum dose of tadalafil: Tadal Access – how long for cialis to take effect
https://tadalaccess.com/# cheapest cialis
Навестите текущий сайт https://clannishfx.com/entendiendo-la-psicologia-del-trading-la-importancia-de-la-mentalidad-y-la-disciplina/?status=success
cheap facebook account buy old facebook account for ads
google ads accounts https://buy-ads-account.top
cialis dosage for bph: best time to take cialis 5mg – ordering cialis online
what happens when you mix cialis with grapefruit? Tadal Access cialis prices
buy google adwords accounts buy-ads-accounts.click
https://tadalaccess.com/# ambrisentan and tadalafil combination brands
viagara cialis levitra: cialis ingredients – what happens if you take 2 cialis
cialis goodrx: cialis results – reliable source cialis
cialis from mexico cialis 5mg price comparison tadalafil hong kong
https://tadalaccess.com/# how long for cialis to take effect
facebook ad accounts for sale buy facebook profile
google ads accounts old google ads account for sale
buy cialis online canada: TadalAccess – cheapest cialis
old google ads account for sale https://ads-account-buy.work/
cialis generic timeline 2018: what happens if a woman takes cialis – cialis from india online pharmacy
https://tadalaccess.com/# cialis sales in victoria canada
Навестите этот веб-сайт https://eficiencia-energetica.co/addressing-wind-energy-innovation-challenges-copy/
tadalafil 40 mg india TadalAccess best price on generic tadalafil
when will teva’s generic tadalafil be available in pharmacies: cialis free samples – cialis canada sale
https://tadalaccess.com/# cialis brand no prescription 365
too much cialis cheaper alternative to cialis what does cialis treat
buy google ads verified account https://buy-ads-invoice-account.top
buy google ads accounts https://buy-account-ads.work
ST666 Xổ Số – Điểm Đến Giải Trí Hoàn HảoST666 Xổ Số là nền tảng giải trí trực tuyến hàng đầu, cung cấp đa dạng các loại hình trò chơi từ keno, xổ số miền Nam (XSMN), xổ số miền Bắc (XSMB) đến xổ số siêu tốc. Với dịch vụ chuyên nghiệp và an toàn, ST666 mang đến cho bạn một trải nghiệm hoàn toàn mới mẻ và hấp dẫn. Tại Sao Nên Chọn ST666 Xổ SốTruy Cập Nhanh Và An ToànST666 đảm bảo quyền truy cập nhanh chóng thông qua đường dẫn chính thức, loại bỏ hoàn toàn rủi ro từ các trang web giả mạo hoặc nguy cơ mất tài khoản. Hệ thống bảo mật hiện đại giúp bạn yên tâm khi đăng nhập và tham gia trò chơi. Ưu Đãi Độc Quyền Dành Cho Thành ViênST666 mang đến nhiều chương trình khuyến mãi đặc biệt dành riêng cho người chơi, bao gồm phần thưởng giá trị và các ưu đãi hấp dẫn. Thành viên mới sẽ được trải nghiệm các chính sách hỗ trợ vượt trội, giúp tăng cơ hội chiến thắng và tận hưởng trò chơi tốt nhất. Bảo Mật Thông Tin Tối ĐaHệ thống mã hóa hiện đại của ST666 đảm bảo mọi giao dịch và dữ liệu cá nhân đều được bảo vệ an toàn. Mọi thông tin đều được xử lý theo quy chuẩn bảo mật cao nhất, giúp người chơi yên tâm giải trí mà không lo lắng về vấn đề rủi ro thông tin. Đa Dạng Trò Chơi Giải TríXổ số: Từ xổ số truyền thống như XSMN, XSMB đến xổ số siêu tốc, đáp ứng mọi nhu cầu giải trí của người chơi.Lô đề: Cung cấp giao diện dễ sử dụng, giúp bạn dễ dàng chọn số và theo dõi kết quả trực tiếp.Casino trực tuyến: Đa dạng các trò chơi từ bài bạc, roulette đến các game đổi thưởng hiện đại.Những Lợi Ích Khi Chơi Tại ST666Dịch vụ hỗ trợ khách hàng chuyên nghiệp hoạt động 24/7.Giao dịch nạp và rút tiền nhanh chóng, minh bạch.Hệ thống cập nhật trò chơi thường xuyên, mang lại sự mới mẻ và không nhàm chán.Nền tảng thiết kế hiện đại, thân thiện với mọi thiết bị, từ máy tính đến điện thoại di động.Cách Truy Cập ST666Truy cập đường dẫn chính thức của ST666 để đảm bảo an toàn.Đăng ký tài khoản và hoàn tất các bước xác thực thông tin.Tham gia các trò chơi hấp dẫn và tận hưởng phần thưởng đặc biệt dành cho thành viên.ST666 Xổ Số không chỉ là nền tảng giải trí mà còn là nơi mang lại cơ hội chiến thắng và trải nghiệm dịch vụ đẳng cấp. Tham gia ngay hôm nay để khám phá một thế giới giải trí đa dạng và chuyên nghiệp!
does cialis make you last longer in bed: TadalAccess – safest and most reliable pharmacy to buy cialis
buy google ad account https://buy-ads-agency-account.top
https://tadalaccess.com/# how to buy tadalafil online
when will generic tadalafil be available maximpeptide tadalafil review cheap tadalafil no prescription
buy liquid cialis online: cialis stopped working – buy cialis generic online 10 mg
Навестите этот сайт https://taxipuntacanamacao.com/index.php/2022/07/01/3-best-nature-weekend-tour-in-japan/
https://tadalaccess.com/# cialis professional ingredients
google ads reseller https://sell-ads-account.click
what is cialis taken for Tadal Access cialis sell
This website is absolutely breathtaking! The design is so visually appealing and every detail feels perfectly placed. Amazing work! eslot
buy cheap cialis online with mastercard: super cialis – buy tadalafil online no prescription
buy google ads invoice account https://ads-agency-account-buy.click
https://tadalaccess.com/# cialis mexico
tadalafil tablets 20 mg side effects cialis covered by insurance mambo 36 tadalafil 20 mg
cialis how to use: tadalafil softsules tuf 20 – cialis super active real online store
cialis premature ejaculation: canadian pharmacy cialis – cialis for sale
Fantastic goods from you, man. I have understand your stuff previous to and you are just too magnificent.I really like what you’ve acquired here, certainly like what you are saying and the way in whichyou say it. You make it enjoyable and you stillcare for to keep it smart. I can’t wait toread far more from you. This is actually a terrific site.
https://tadalaccess.com/# cialis online reviews
buy verified facebook business manager buy facebook verified business manager
Discover the application steps and requirements for the Civil Engineering undergraduate program at Satbayev University. Learn about curriculum structure and career prospects. Ideal for students interested in construction, structural analysis, infrastructure https://satbayev.university/
buy google ads threshold accounts buy aged google ads account
cialis canada over the counter: cheapest cialis online – cialis and dapoxetime tabs in usa
cialis otc switch pictures of cialis pills safest and most reliable pharmacy to buy cialis
Навестите этот веб-сайт https://www.yaumbazar.com/product/deshi-peyaj-local-onion-%c2%b1-50-gm/
cialis results: cialis price canada – cialis paypal
https://tadalaccess.com/# overnight cialis delivery
does tadalafil lower blood pressure: TadalAccess – bph treatment cialis
cialis walmart TadalAccess cialis insurance coverage blue cross
buy facebook business account buy-bm-account.org
what is tadalafil made from: Tadal Access – cheapest 10mg cialis
business manager for sale buy-verified-business-manager-account.org
verified facebook business manager for sale https://buy-verified-business-manager.org
cialis professional vs cialis super active: cialis tablets – generic tadalafil tablet or pill photo or shape
cheap cialis with dapoxetine TadalAccess cialis max dose
buy verified facebook https://buy-business-manager-acc.org
pastilla cialis: cheap cialis – cialis canada prices
https://tadalaccess.com/# online cialis australia
Приедете в текущий сайт https://www.bighosting.com.ar/improving-website-performance-with-litespeed/
cialis tablets: maximpeptide tadalafil review – cialis tadalafil 20 mg
cialis maximum dose tadalafil softsules tuf 20 can tadalafil cure erectile dysfunction
https://tadalaccess.com/# cialis genetic
where to buy tadalafil online: TadalAccess – maxim peptide tadalafil citrate
Choi the thao, xo so, game bai doi thuong, casino online, ban ca, slot, lo de online da tay tai net79 se giup anh em giai toa cang thang hieu qua net79.vip
business manager for sale business-manager-for-sale.org
https://dommedika.com/nevrologia/mrt-mozga-pri-otravlenii-ugarnim-gazom.html
buy fb business manager https://buy-business-manager-verified.org
https://tadalaccess.com/# what is the difference between cialis and tadalafil
facebook business manager account buy https://buy-bm.org/
cialis logo: best place to buy generic cialis online – cialis mechanism of action
super cialis TadalAccess cialis free trial phone number
https://tadalaccess.com/# where can i buy cialis online in australia
Побываете этот сайт https://mutsukawa.yokohama/etc/6%e6%9c%8814%e6%97%a5-%e5%8d%88%e5%be%8c-%e4%bd%93%e9%a8%93%e4%bc%9a-%e3%81%8d%e3%81%a6%e3%81%ad%e3%81%a3%ef%bc%81/
cialis 5 mg: how well does cialis work – cialis overnight deleivery
https://tadalaccess.com/# cialis generic overnite shipping
tadalafil troche reviews Tadal Access does cialis lowers blood pressure
facebook bm buy https://buy-business-manager-accounts.org
Профессиональный сервисный центр по ремонту техники в Екатеринбурге.
Мы предлагаем: Ремонт тепловизоров Guide с гарантией
Наши мастера оперативно устранят неисправности вашего устройства в сервисе или с выездом на дом!
buy facebook business account facebook bm account buy
tiktok ad accounts buy tiktok business account
cialis with dapoxetine 60mg: Tadal Access – cialis price per pill
tiktok ad accounts https://tiktok-ads-account-buy.org
https://tadalaccess.com/# difference between sildenafil tadalafil and vardenafil
what is cialis used for TadalAccess online pharmacy cialis
buy tadalafil online canada: how long does it take cialis to start working – overnight cialis
Introducing to you the most prestigious online entertainment address today. Visit now to experience now!
Актуальные новости. Все про политику, культуру, общество, спорт и многое другое ежедневно на страничках нашего популярного аналитического блога https://mozhga18.ru/
Новости экономики России, зарплаты и кредиты, обзоры профессий, идеи бизнеса и истории бизнесменов. Независимая экономическая аналитика и репортажи https://iqreview.ru/
cialis not working: cialis onset – cialis with dapoxetine
cialis and melanoma tadalafil citrate can cialis cause high blood pressure
https://tadalaccess.com/# prescription free cialis
This is great.
накрутка подписчиков в телеграм живые бесплатно
tiktok ad accounts https://tiktok-ads-account-for-sale.org
tiktok ads agency account https://tiktok-agency-account-for-sale.org
sildenafil vs cialis: buying cialis generic – no presciption cialis
tiktok ads agency account https://buy-tiktok-ad-account.org
where to buy generic cialis ?: TadalAccess – prescription free cialis
how long i have to wait to take tadalafil after antifugal tadalafil vs cialis п»їwhat can i take to enhance cialis
Актуальные статьи с полезными советами по строительству и ремонту. Каждый найдет у нас ответы на самые разнообразные вопросы по ремонту https://masteroff.org/
https://tadalaccess.com/# cialis free trial phone number
reliable source cialis: Tadal Access – buy cialis generic online 10 mg
order cialis canada tamsulosin vs. tadalafil cialis for daily use reviews
this is a great post!
tiktok ad accounts https://buy-tiktok-ads-accounts.org
tadalafil eli lilly: cialis before and after photos – purchase cialis online
https://tadalaccess.com/# cialis over the counter
overnight cialis delivery usa: does cialis make you harder – cialis drug class
this is a great post!
https://www.asseenontvonline.ru/
накрутка просмотров в тг канале
how to get cialis without doctor TadalAccess cialis overdose
Saved as a favorite, I love your site!
Актуальные мировые события. Последние новости, собранные с разных уголков земного шара. Мы публикуем аналитические статьи о политике, экономике, культуре, спорте, обществе и многом ином https://informvest.ru/
https://tadalaccess.com/# best price on cialis 20mg
cialis canadian purchase cialis dosages cialis buy without
when should i take cialis: TadalAccess – cialis doesnt work for me
Старый Лекарь болезни и лечение – Лекарь расскажет: лекарственные травы, болезни и лечение, еда, массаж, диеты и правильное питание https://old-lekar.com/
buy tiktok ads accounts tiktok agency account for sale
cialis 5mg 10mg no prescription Tadal Access cialis prices
https://tadalaccess.com/# cialis generic best price that accepts mastercard
Самые интересные и полезные статьи на тему настройки и оптимизации работы компьютеров и оргтехники https://www.softo-mir.ru/
cialis samples for physicians: Tadal Access – cialis generic over the counter
cialis sales in victoria canada TadalAccess cialis free sample
when will teva’s generic tadalafil be available in pharmacies: how long does it take for cialis to take effect – cialis vs sildenafil
cialis 100mg from china cialis 20 mg price walmart buy cialis in toronto
free cialis samples: where to buy tadalafil online – cialis in canada
this is a great post!
tiktok agency account for sale https://buy-tiktok-business-account.org
buy tiktok business account https://buy-tiktok-ads.org
https://tadalaccess.com/# tadalafil best price 20 mg
Блог, посвященный любителям самоделок. Интересные статьи по теме стройки и ремонта, авто, сада и огорода, вкусных рецептов, дизайна и много другого, что каждый может сделать своими руками https://notperfect.ru/
this is a great post!
Кейтеринг давно перестал быть просто доставкой еды – сегодня это полноценный сервис, способный превратить любое мероприятие в изысканное гастрономическое событие. Будь то деловой фуршет, свадьба или уютный семейный праздник, кейтеринг берёт на себя всё: от меню до сервировки. В этой статье мы разберёмся, какие бывают виды кейтеринга, что важно учитывать при выборе подрядчика и почему этот формат становится всё популярнее: ресторан выездного обслуживания
Ежедневные публикации про новинки автомобилей, советы по ремонту и эксплуатации, мастер-классы тюнинга, новое в правилах ПДД и автомобильных законах в нашем блоге https://mineavto.ru/
cialis dose e-cialis hellocig e-liquid where to get generic cialis without prescription
This time, he plans to overshadow Moses’ feats in the sport world.
Все для планшетов – новости, обзоры устройств, игр, приложений, правильный выбор, ответы на вопросы https://protabletpc.ru/
https://tadalaccess.com/# 20 mg tadalafil best price
cialis alcohol: tadalafil online paypal – buy cialis cheap fast delivery
online pharmacy cialis cialis cheapest price buy cialis toronto
what does cialis cost: levitra vs cialis – cialis dopoxetine
cialis 5mg how long does it take to work tadalafil generic headache nausea tadalafil online paypal
https://tadalaccess.com/# cialis doesnt work
СамСтрой. Блог о ремонте и строительтве для каждого! Полезные советы, фото и видео материалы про стройку и ремонт, дизайн интерьера, а также приусадебный участок https://biosferapark.ru/
this is a great post!
cialis w/o perscription: cialis windsor canada – cialis 100 mg usa
Hi colleagues, its great article about cultureand entirely explained, keep it up all the time.
stpierre
sex nhật, hiếp dâm trẻ em, ấu dâm, buôn bán vũ khí, ma túy, bán súng, sextoy, chơi đĩ, sex bạo lực, sex học đường, tội phạm tình dục
this is a great post!
this is a great post!
this is a great post!
That is really attention-grabbing, You’re an excessively professional blogger. I have joined your feed and look forward to seeking more of your magnificent post. Additionally, I have shared your site in my social networks
Melbet
都営地下鉄大江戸線、東京メトロ有楽町線の月島駅を下車すると、目の前には月島西仲通り商店街があります。東宝.21 March 2020. 該当時間: 4:20. 2020年3月22日閲覧。先日東京ビッグサイトで開催された、第1回メタバース総合展(2023年6月28日~6月30日)に出展いたしました。勤務先の健康保険組合などに加入している場合は、勤務先を経由して申請します。 “TVアニメ『僕のヒーローアカデミア』気になる放送枠は、日曜のあの時間に!
https://ukrainedigest.com.ua/pohoda-v-fastovi/
https://kitsu.app/users/1598495
Just desire to say your article is as amazing. The clearness to your put up is just excellent and that i can suppose you’re an expert on this subject. Fine together with your permission let me to take hold of your RSS feed to stay up to date with drawing close post. Thank you a million and please continue the enjoyable work.
hafilat bus card balance check
this is a great post!
I like the efforts you have put in this, thankyou for all the great content.
this is a great post!
https://www.ukrinformer.com.ua/karta-fastova/
this is a great post!
How lengthy does it take to complete every work, from conception to a completed makeup artwork?
Today, while I was at work, my cousin stole my iPad and tested to see if it can survive a forty foot drop, just so she can be a youtube sensation. My iPad is now broken and she has 83 views. I know this is totally off topic but I had to share it with someone!
https://writeablog.net/gumcomma0/honoring-the-legacy-regarding-henry-thierry-also-called-thierry-anri
кайтсерфинг египет
I am very bokep happy, I learned a lot on this site now
cialis generico 5 mg prezzo in farmacia : a medication containing tadalafil, treats erectile dysfunction and benign prostatic hyperplasia. In Italy, a 28-tablet pack of Cialis 5 mg costs around €165.26, though prices vary by pharmacy and promotions. Generic options, like Tadalafil DOC Generici, cost €0.8–€2.6 per tablet, providing a budget-friendly option. Consult a doctor, as a prescription is needed.
кайт школа египет
buy antibiotics online: buy antibiotics online – buy antibiotics from canada
low cost ed medication ed online meds erectile dysfunction pills online
buy ed pills: buy ed meds – cheapest ed treatment
https://pharmau24.shop/# PharmAu24
Over the counter antibiotics pills: buy antibiotics – buy antibiotics from india
Attractive section of content. I just stumbled upon your weblog and in accession capital to assert that I acquire actually enjoyed account your blog posts. Any way I will be subscribing to your augment and even I achievement you access consistently rapidly.
https://brightwallpapers.com.ua/yak-vidriznyty-oryhinalnyy-elektroshoker-vid-pidroblenoho-porady-ta-rekomendatsiyi
Online drugstore Australia: pharmacy online australia – Online medication store Australia
Buy medicine online Australia online pharmacy australia Buy medicine online Australia
top rated ed pills: ed pills – Ero Pharm Fast
this is a great post!
http://eropharmfast.com/# ed pills cheap
discount ed pills: Ero Pharm Fast – Ero Pharm Fast
That is a great tip particularly to those fresh to the blogosphere. Short but very accurate information… Thanks for sharing this one. A must read article!
this is a great post!
buy antibiotics online: BiotPharm – Over the counter antibiotics for infection
Thank you for the auspicious writeup. It in truth was a leisure account it. Glance complex to far added agreeable from you! By the way, how could we communicate?
https://companion.com.ua/yak-vibrati-idealne-sklo-korpusi-ta-fari-dlya-avto
обучение кайтсёрфингу
Ero Pharm Fast: cheapest ed pills – Ero Pharm Fast
Ero Pharm Fast Ero Pharm Fast cheap erection pills
http://pravo-med.ru/articles/18547/
Ero Pharm Fast: low cost ed meds online – online prescription for ed
this is a great post!
Pharm Au 24: Buy medicine online Australia – pharmacy online australia
https://pharmau24.shop/# Buy medicine online Australia
https://oboronspecsplav.ru/
http://biotpharm.com/# cheapest antibiotics
this is a great post!
this is a great post!
Pharm Au 24: Pharm Au 24 – Online medication store Australia
Ero Pharm Fast: cheapest online ed treatment – Ero Pharm Fast
Buy medicine online Australia Online medication store Australia Licensed online pharmacy AU
this is a great post!
Medications online Australia: pharmacy online australia – PharmAu24
this is a great post!
buy antibiotics from india: Biot Pharm – antibiotic without presription
This is the perfect website for everyone who really wants to understand this topic. You realize so much its almost tough to argue with you (not that I personally will need to…HaHa). You definitely put a new spin on a topic which has been discussed for years. Excellent stuff, just great!
Zain recharge
https://biotpharm.shop/# antibiotic without presription
«Рентвил» предлагает аренду автомобилей в Краснодаре без залога и ограничений по пробегу по Краснодарскому краю и Адыгее. Требуется стаж от 3 лет и возраст от 23 лет. Оформление за 5 минут онлайн: нужны только фото паспорта и прав. Подача авто на жд вокзал и аэропорт Краснодар Мин-воды Сочи . Компания работает 10 лет , автомобили проходят своевременное ТО. Доступны детские кресла. Бронируйте через сайт Краснодар аренда автомобиля
Hello to every single one, it’s actually a fastidious for me to pay a quick visit this site, it consists of useful Information.
my Zain
Discount pharmacy Australia: Licensed online pharmacy AU – Licensed online pharmacy AU
Pharm Au 24 Pharm Au24 Online medication store Australia
get antibiotics without seeing a doctor: Biot Pharm – buy antibiotics online
get antibiotics without seeing a doctor: buy antibiotics online – over the counter antibiotics
Remarkable issues here. I am very satisfied to peer your article. Thank you so much and I am looking ahead to touch you. Will you kindly drop me a mail?
Myzain
выкуп товара из китая В эпоху глобализации и стремительного развития мировой экономики, Китай занимает ключевую позицию в качестве крупнейшего производственного центра. Организация эффективных и надежных поставок товаров из Китая становится стратегически важной задачей для предприятий, стремящихся к оптимизации затрат и расширению ассортимента. Наша компания предлагает комплексные решения для вашего бизнеса, обеспечивая бесперебойные и выгодные поставки товаров напрямую из Китая.
Online medication store Australia Licensed online pharmacy AU Pharm Au24
Online medication store Australia: Pharm Au 24 – Pharm Au24
Spot on with this write-up, I absolutely believe this website needs much more attention. I’ll probably be back again to read through more, thanks for the info!
https://biotpharm.shop/# Over the counter antibiotics pills
Medications online Australia Pharm Au 24 PharmAu24
Online drugstore Australia: pharmacy online australia – Licensed online pharmacy AU
erectile dysfunction meds online cheap ed pills online erectile dysfunction meds online
antibiotic without presription: Biot Pharm – Over the counter antibiotics pills
this is a great post!
https://biotpharm.shop/# get antibiotics quickly
this is a great post!
erectile dysfunction online Ero Pharm Fast Ero Pharm Fast
Your point of view caught my eye and was very interesting. Thanks. I have a question for you.
Buy medicine online Australia: pharmacy online australia – Online medication store Australia
this is a great post!
cheapest antibiotics antibiotic without presription Over the counter antibiotics pills
Ero Pharm Fast: ed medicines online – Ero Pharm Fast
this is a great post!
https://eropharmfast.shop/# Ero Pharm Fast
cheapest online ed meds ed medications online buy ed medication online
Medications online Australia: Pharm Au24 – PharmAu24
Ero Pharm Fast Ero Pharm Fast ed meds cheap
online prescription for ed: get ed prescription online – Ero Pharm Fast
Угловой шкаф Кухня – сердце дома, место, где рождаются кулинарные шедевры и собирается вся семья. Именно поэтому выбор мебели для кухни – задача ответственная и требующая особого подхода. Мебель на заказ в Краснодаре – это возможность создать уникальное пространство, идеально отвечающее вашим потребностям и предпочтениям.
https://biotpharm.shop/# buy antibiotics from canada
Online medication store Australia: Online medication store Australia – Discount pharmacy Australia
Discount pharmacy Australia Online drugstore Australia Online medication store Australia
this is a great post!
this is a great post!
acheter Cialis sans ordonnance: cialis prix – traitement ED discret en ligne
livraison discrete Kamagra pharmacie en ligne france fiable kamagra 100mg prix
this is a great post!
https://viasansordonnance.shop/# acheter Viagra sans ordonnance
acheter Kamagra sans ordonnance: commander Kamagra en ligne – acheter Kamagra sans ordonnance
acheter Cialis sans ordonnance cialis generique commander Cialis en ligne sans prescription
viagra en ligne: prix bas Viagra generique – Acheter du Viagra sans ordonnance
acheter kamagra site fiable: acheter kamagra site fiable – kamagra 100mg prix
this is a great post!
Viagra sans ordonnance 24h: Meilleur Viagra sans ordonnance 24h – commander Viagra discretement
this is a great post!
this is a great post!
this is a great post!
traitement ED discret en ligne cialis sans ordonnance commander Cialis en ligne sans prescription
this is a great post!
Medicaments en ligne livres en 24h: pharmacie internet fiable France – pharmacie en ligne france pas cher
this is a great post!
this is a great post!
this is a great post!
https://pharmsansordonnance.shop/# pharmacie en ligne sans ordonnance
viagra sans ordonnance: prix bas Viagra générique – acheter Viagra sans ordonnance
acheter Kamagra sans ordonnance: kamagra gel – acheter Kamagra sans ordonnance
this is a great post!
this is a great post!
this is a great post!
Acheter Cialis Cialis generique sans ordonnance commander Cialis en ligne sans prescription
this is a great post!
Medicaments en ligne livres en 24h: pharmacie en ligne – Pharmacie sans ordonnance
prix bas Viagra générique: Acheter du Viagra sans ordonnance – acheter Viagra sans ordonnance
Acheter Cialis 20 mg pas cher: vente de mГ©dicament en ligne – vente de mГ©dicament en ligne
Kamagra oral jelly pas cher kamagra en ligne acheter Kamagra sans ordonnance
Introducing to you the most prestigious online entertainment address today. Visit now to experience now!
https://kampascher.shop/# kamagra gel
pharmacie en ligne sans prescription: pharmacies en ligne certifiées – pharmacie en ligne
Acheter Cialis 20 mg pas cher: traitement ED discret en ligne – cialis prix
SildГ©nafil 100mg pharmacie en ligne: Acheter du Viagra sans ordonnance – Acheter du Viagra sans ordonnance
Medicaments en ligne livres en 24h pharmacie en ligne pas cher pharmacie en ligne avec ordonnance
Kamagra oral jelly pas cher: achat kamagra – kamagra en ligne
pharmacie en ligne sans prescription: pharmacie en ligne sans prescription – pharmacie en ligne fiable
cialis prix: pharmacie en ligne france pas cher – pharmacie en ligne livraison europe
pharmacie internet fiable France acheter medicaments sans ordonnance pharmacie en ligne
https://viasansordonnance.com/# Acheter du Viagra sans ordonnance
achat kamagra: acheter Kamagra sans ordonnance – livraison discrete Kamagra
Kamagra oral jelly pas cher acheter Kamagra sans ordonnance kamagra oral jelly
cialis generique: traitement ED discret en ligne – acheter Cialis sans ordonnance
acheter medicaments sans ordonnance: commander sans consultation medicale – pharmacie en ligne france pas cher
acheter médicaments sans ordonnance: Médicaments en ligne livrés en 24h – pharmacie en ligne
https://viasansordonnance.com/# Viagra sans ordonnance 24h
Pharmacies en ligne certifiees: pharmacie en ligne sans prescription – pharmacie en ligne fiable
this is a great post!
livraison discrete Kamagra commander Kamagra en ligne pharmacie en ligne pas cher
this is a great post!
this is a great post!
this is a great post!
commander Cialis en ligne sans prescription: commander Cialis en ligne sans prescription – cialis prix
commander Cialis en ligne sans prescription: traitement ED discret en ligne – Cialis générique sans ordonnance
this is a great post!
this is a great post!
pharmacie en ligne pas cher: pharmacie en ligne pas cher – vente de mГ©dicament en ligne
this is a great post!
livraison rapide Viagra en France Viagra sans ordonnance 24h Viagra en france livraison rapide
this is a great post!
Cialis générique sans ordonnance: commander Cialis en ligne sans prescription – Acheter Cialis
http://pharmsansordonnance.com/# Achat mГ©dicament en ligne fiable
kamagra gel: commander Kamagra en ligne – kamagra gel
Cialis generique sans ordonnance: traitement ED discret en ligne – Cialis pas cher livraison rapide
viagra sans ordonnance livraison rapide Viagra en France Viagra sans ordonnance 24h
Cialis generique sans ordonnance: pharmacie en ligne fiable – cialis prix
kamagra oral jelly: pharmacie en ligne pas cher – kamagra 100mg prix
pharmacie en ligne sans ordonnance pharmacie en ligne pas cher pharmacie en ligne france fiable
kamagra pas cher: Kamagra oral jelly pas cher – Kamagra oral jelly pas cher
excellent put up, very informative. I ponder why the other experts of this sector do not realize this. You must proceed your writing. I’m confident, you’ve a huge readers’ base already!
Let’s look at the Amazon rainforest again and how it is home to thousands of species of animals. Amazon Slots takes direct inspiration from that by creating a platform for 700+ real money slots & casino games. Start choosing an online machine by familiarizing yourself with its provider. This small detail can radically change your subsequent gaming experience due to many factors. Software providers give special bonus offers to allow to start playing online slots. Each game developer has distinctive characteristics and traceable style in internet pokies. Aristocrat pokies have made a name for themselves by creating online and offline slot machines to play without money. Know what licenses game developers have. Even a free game from a dishonest provider can leak player data from his device. We attach a list of the best and most trusted internet games providers:
https://vekstra.sardaritskillshare.com/top-reviews-for-aviator-slot-in-2025/
Online Casino With Free Signup Bonus Real Money Uk Online Casino With Free Signup Bonus Real Money Uk Online Casino With Free Signup Bonus Real Money Uk You can email the site owner to let them know you were blocked. Please include what you were doing when this page came up and the Cloudflare Ray ID found at the bottom of this page. Online Casino With Free Signup Bonus Real Money Uk You can email the site owner to let them know you were blocked. Please include what you were doing when this page came up and the Cloudflare Ray ID found at the bottom of this page. In order to make the list we analyze the following characteristics of all the online casinos offered, I will keep this complaint opened. Of course, reddit online casino united kingdom so please keep us updated and let us know if there is anything new.
https://ciasansordonnance.com/# Acheter Cialis 20 mg pas cher
Cialis sans ordonnance 24h: cialis prix – acheter Cialis sans ordonnance
livraison rapide Viagra en France: viagra sans ordonnance – Meilleur Viagra sans ordonnance 24h
Viagra sans ordonnance pharmacie France livraison rapide Viagra en France viagra sans ordonnance
this is a great post!
Good web site you have here.. It’s difficult to find high-quality writing like yours these days. I truly appreciate individuals like you! Take care!!
Hello! This post could not be written any better! Reading through this post reminds me of my old room mate! He always kept talking about this. I will forward this article to him. Pretty sure he will have a good read. Many thanks for sharing!
hafilat
this is a great post!
this is a great post!
this is a great post!
this is a great post!
acheter kamagra site fiable: commander Kamagra en ligne – acheter Kamagra sans ordonnance
pharmacie en ligne sans ordonnance: pharmacie en ligne sans ordonnance – pharmacie en ligne
viagra en ligne Viagra sans ordonnance 24h prix bas Viagra generique
this is a great post!
viagra sans ordonnance: SildГ©nafil 100 mg sans ordonnance – viagra sans ordonnance
Kamagra oral jelly pas cher commander Kamagra en ligne Kamagra oral jelly pas cher
https://viasansordonnance.com/# viagra en ligne
kamagra en ligne: acheter Kamagra sans ordonnance – kamagra oral jelly
Acheter Cialis: Pharmacie sans ordonnance – Cialis pas cher livraison rapide
acheter medicaments sans ordonnance acheter medicaments sans ordonnance Pharmacie en ligne livraison Europe
В динамичном мире Санкт-Петербурга, где каждый день кипит жизнь и совершаются тысячи сделок, актуальная и удобная доска объявлений становится незаменимым инструментом как для частных лиц, так и для предпринимателей. Наша платформа – это ваш надежный партнер в поиске и предложении товаров и услуг в Северной столице. Реклама в интернете бесплатно
Viagra gГ©nГ©rique pas cher livraison rapide: Viagra generique en pharmacie – commander Viagra discretement
commander Cialis en ligne sans prescription: Cialis pas cher livraison rapide – cialis sans ordonnance
Greetings I am so happy I found your site, I really found you by error, while I was researching on Askjeeve for something else, Nonetheless I am here now and would just like to say kudos for a fantastic post and a all round enjoyable blog (I also love the theme/design), I don’t have time to browse it all at the minute but I have book-marked it and also added in your RSS feeds, so when I have time I will be back to read a great deal more, Please do keep up the excellent b.
prepaid card inquiry
traitement ED discret en ligne acheter Cialis sans ordonnance Cialis pas cher livraison rapide
http://ciasansordonnance.com/# pharmacie en ligne avec ordonnance
Your point of view caught my eye and was very interesting. Thanks. I have a question for you. https://accounts.binance.com/ru-UA/register-person?ref=OMM3XK51
this is a great post!
Kamagra oral jelly pas cher: kamagra gel – acheter Kamagra sans ordonnance
Kamagra oral jelly pas cher acheter Kamagra sans ordonnance kamagra en ligne
this is a great post!
this is a great post!
traitement ED discret en ligne: cialis prix – cialis sans ordonnance
Kantorbola merupakan pilihan terbaik bagi para penggemar slot online di Indonesia. Dengan berbagai permainan menarik, bonus melimpah, keamanan terjamin, dan layanan pelanggan yang unggul.
viagra sans ordonnance commander Viagra discretement prix bas Viagra generique
viagra en ligne: Meilleur Viagra sans ordonnance 24h – Meilleur Viagra sans ordonnance 24h
pharmacie en ligne sans prescription commander sans consultation medicale pharmacie en ligne sans ordonnance
http://ciasansordonnance.com/# acheter Cialis sans ordonnance
My spouse and I absolutely love your blog and find many of your post’s to be exactly what I’m looking for. Do you offer guest writers to write content to suit your needs? I wouldn’t mind producing a post or elaborating on a few of the subjects you write about here. Again, awesome web log!
https://pravoslavnews.com.ua/yaki-linzy-dlya-far-nichne-osvitlennya
viagra en ligne: viagra sans ordonnance – acheter Viagra sans ordonnance
Introducing to you the most prestigious online entertainment address today. Visit now to experience now!
Viagra sans ordonnance livraison 48h livraison rapide Viagra en France Viagra gГ©nГ©rique sans ordonnance en pharmacie
pharmacie en ligne: Medicaments en ligne livres en 24h – pharmacie en ligne france livraison internationale
kamagra 100mg prix kamagra livraison 24h kamagra oral jelly
kamagra pas cher: acheter kamagra site fiable – achat kamagra
музыкальные новинки Роп – Русский роп – это больше, чем просто музыка. Это зеркало современной российской души, отражающее её надежды, страхи и мечты. В 2025 году жанр переживает новый виток развития, впитывая в себя элементы других стилей и направлений, становясь всё более разнообразным и эклектичным. Популярная музыка сейчас – это калейдоскоп звуков и образов. Хиты месяца мгновенно взлетают на вершины чартов, но так же быстро и забываются, уступая место новым музыкальным новинкам. 2025 год дарит нам множество талантливых российских исполнителей, каждый из которых вносит свой неповторимый вклад в развитие жанра.
http://pharmsansordonnance.com/# pharmacies en ligne certifiГ©es
Сергей Бидус кинул на деньги
Acheter Cialis Acheter Cialis 20 mg pas cher commander Cialis en ligne sans prescription
cialis generique: acheter Cialis sans ordonnance – Cialis sans ordonnance 24h
prix bas Viagra generique prix bas Viagra generique livraison rapide Viagra en France
https://kampascher.com/# achat kamagra
красное море температура воды
hey there and thank you for your info – I’ve certainly picked up anything new from right here. I did however expertise a few technical points using this web site, as I experienced to reload the site lots of times previous to I could get it to load correctly. I had been wondering if your hosting is OK? Not that I am complaining, but slow loading instances times will very frequently affect your placement in google and could damage your high quality score if advertising and marketing with Adwords. Anyway I’m adding this RSS to my e-mail and could look out for a lot more of your respective interesting content. Make sure you update this again very soon..
This is my first time visit at here and i am really impressed to read everthing at one place.
nagy mell porno
comprar bactroban pomada sin receta: se puede comprar ibuprofeno sin receta en espaГ±a – farmacia online test de antigenos
ordonnance cardiologue Pharmacie Express aller chez l’orl sans ordonnance
https://pharmacieexpress.com/# pneumologue sans ordonnance
acheter tadalafil 10mg en ligne: periactine en pharmacie sans ordonnance – sildenafil france
comprar nootropil sin receta: farmacia online la botica – comprar enanplus sin receta
smecta pharmacie sans ordonnance Pharmacie Express creme depilatoire hypoallergГ©nique
farmacia online mendoza: comprar tiadipona sin receta – farmacia online españa envÃo internacional
What’s up, of course this paragraph is genuinely good and I have learned lot of things from it on the topic of blogging. thanks.
hafilat balance check
Rainbet promo code ILBET В динамичном мире онлайн-развлечений Rainbet занимает особое место, предоставляя игрокам широкие возможности для азартных игр и спортивных ставок. Для максимального увеличения выгоды и усиления азарта используйте промокод ILBET при регистрации или внесении депозита. Этот код активирует эксклюзивные бонусы, акции и предложения, разработанные как для новичков, так и для опытных игроков.
eutirox 50 prezzo: fluspiral 125 spray prezzo – dott max farmacia online
spray nasal ordonnance: quel est le meilleur anxiolytique sans ordonnance – jasmine pilule prix
Курительная трубка – это не просто способ насладиться табаком, а целый ритуал, требующий внимания к деталям. Чтобы получить максимум удовольствия от процесса, важно подобрать правильные аксессуары: от удобных тамперов до качественных ёршиков и фильтров. В этой статье мы расскажем, какие принадлежности действительно полезны, как они влияют на вкус и сохранность трубки, и на что стоит обратить внимание при выборе: аксессуары для трубки курительной
mГ©dicament paludisme prix location tire lait pharmacie sans ordonnance tadalafil sans ordonnance en pharmacie
https://farmaciasubito.shop/# farmacia online reggio emilia
clody 200 mg fiale è mutuabile prezzo: farmacia vendita online – eminocs gocce prezzo
pharmacie dГ©livrer pilule sans ordonnance: acheter une minerve en pharmacie sans ordonnance – spedra pharmacie sans ordonnance
martiderm farmacia online farmacia online en alemania se puede comprar tretinoina sin receta
zyntabac se puede comprar sin receta: farmacia en tenerife online – farmacia homeopГЎtica online
toujeo 300: farmacia online padova – gibiter spray
arcalion sans ordonnance: quoi prendre pour une cystite sans ordonnance – cialis 20mg generique
https://farmaciasubito.shop/# farmacia via napoli castellammare di stabia
la aspirina se puede comprar sin receta comprar naproxeno sodico sin receta se puede comprar meloxicam sin receta
chicken road app Chicken Road: Взлеты и Падения на Пути к Успеху Chicken Road – это не просто развлечение, это обширный мир возможностей и тактики, где каждое решение может привести к невероятному взлету или полному краху. Игра, доступная как в сети, так и в виде приложения для мобильных устройств (Chicken Road apk), предлагает пользователям проверить свою фортуну и чутье на виртуальной “куриной тропе”. Суть Chicken Road заключается в преодолении сложного маршрута, полного ловушек и опасностей. С каждым успешно пройденным уровнем, награда растет, но и увеличивается шанс неудачи. Игроки могут загрузить Chicken Road game demo, чтобы оценить механику и особенности геймплея, прежде чем рисковать реальными деньгами.
creme depilatoire pharmacie: achat cialis sans ordonnance – combien dure une ordonnance
diazepam sans ordonnance: Pharmacie Express – médicament diabète sans ordonnance
mascherine farmacia online: Farmacia Subito – farmacia online roma
loette comprar sin receta se puede comprar dormidina sin receta tu farmacia online mascarillas
metilfenidato sin receta comprar: grado universitario farmacia online – comprar orfidal online sin receta
Крыша на балкон Балкон, прежде всего, – это открытое пространство, связующее звено между уютом квартиры и бескрайним внешним миром. Однако его беззащитность перед капризами погоды порой превращает это преимущество в существенный недостаток. Дождь, снег, палящее солнце – все это способно причинить немало хлопот, лишая возможности комфортно проводить время на балконе, а также нанося ущерб отделке и мебели. Именно здесь на помощь приходит крыша на балкон – надежная защита и гарантия комфорта в любое время года.
arnica 7ch posologie: traitement chlamydia sans ordonnance en pharmacie – médicament sans ordonnance pharmacie
roobet bonus code 2025 WEB3 В мире онлайн-казино инновации не стоят на месте, и Roobet находится в авангарде этих перемен. С появлением технологии Web3, Roobet предлагает игрокам новый уровень прозрачности, безопасности и децентрализации. Чтобы воспользоваться всеми преимуществами этой передовой платформы, используйте промокод WEB3.
puedo comprar corticoides sin receta test covid comprar farmacia online farmacia en casa online opiniones
https://farmaciasubito.shop/# imovax tetano
acheter viagra pharmacie sans ordonnance: medicament pour arreter l’alcool sans ordonnance en pharmacie – acheter la pilule sans ordonnance en pharmacie
se puede comprar otix sin receta: se puede comprar itraconazol sin receta – puedo comprar metamizol sin receta
clasteon 200 mg fiale e mutuabile prezzo: betmiga 50 mg generico prezzo – zirtec gocce bambini
pharmacie sans ordonnance avis: prix du viagra generique – sildénafil prix
gentalyn beta costo mutabon mite tachifene 500 a cosa serve
broncho munal bambini prezzo: Farmacia Subito – capillarema generico prezzo
farmacia online orlais: comprar cialis en farmacias de madrid sin receta – farmacia online test rapido covid
Penalty Shootouts C’è un problema di recuperare il carrello in questo momento Supercoppa Primavera “JoomSport – for Sports: Team & League, Football, Hockey & more” è un software open source. Le persone che hanno contribuito allo sviluppo di questo plugin sono indicate di seguito. Use cross-validation to determine estimates of model quality: Select to perform cross-validation and obtain various model quality metrics and graphs. Some metrics and graphs will be displayed in the static R output, and others will be displayed in the interactive I output. FC Cincinnati is now also offering a Flex Plan. Fans can select one Leagues Cup match, in addition to two to five regular season matches. The Flex Plan provides ultimate flexibility, with benefits including cost savings, no fees and presale access for additional events at TQL Stadium, including potential home playoff matches.
https://miottodistribuidora.com.br/le-statistiche-piu-interessanti-sul-gioco-aviator-di-spribe-in-italia/
Su PixBet, provate Penalty Shoot-Out con un’interfaccia facile da usare e una varietà di metodi di pagamento. Sul sito ufficiale del casinò PixBet, cercate la parola “rigore” nella barra di ricerca per trovare Penalty Shoot Out PixBet. Provate il brivido di tirare i rigori e cercate di segnare dei gol per vincere dei premi con un’interfaccia facile da usare. Le caratteristiche principali del casinò PixBet in questo gioco includono: Inoltre, l’hacking compromette il piacere e la soddisfazione di giocare legittimamente. Penalty Shoot Out offre un’esperienza di gioco emozionante e coinvolgente, e i giocatori sono incoraggiati a impegnarsi nel gioco entro i limiti del fair play e della buona sportività. Inoltre, l’hacking compromette il piacere e la soddisfazione di giocare legittimamente. Penalty Shoot Out offre un’esperienza di gioco emozionante e coinvolgente, e i giocatori sono incoraggiati a impegnarsi nel gioco entro i limiti del fair play e della buona sportività.
tobradex pomata prezzo diflucan 100 glucophage unidie 750
I couldn’t resist commenting. Exceptionally well written.
Проектное управление Управление процессами: создайте бизнес, который работает на вас. Управление процессами — это ключ к систематизации и автоматизации бизнеса. Опытный ментор поможет вам моделировать, анализировать и совершенствовать бизнес-процессы, чтобы снизить затраты и повысить качество. В результате ваш бизнес станет более прозрачным, управляемым и готовым к масштабированию. Не позволяйте хаосу тормозить рост — закажите консультацию и получите поддержку от эксперта, который поможет вам создать устойчивость и конкурентоспособность в бизнесе. Пришло время действовать — начните преобразование уже сегодня.
farmacia dr max comanda online: diane 35 se puede comprar sin receta – requisitos farmacia online
https://confiapharma.com/# farmacia online chollo
gommage filorga: monuril pharmacie sans ordonnance – nicopatch pierre fabre
pappataci puntura consegna farmaci a domicilio monuril prezzo
tamponi rapidi farmacia online: Farmacia Subito – farmacia online mascherine
pinco yukle Pinco, Pinco AZ, Pinco Casino, Pinco Kazino, Pinco Casino AZ, Pinco Casino Azerbaijan, Pinco Azerbaycan, Pinco Gazino Casino, Pinco Pinco Promo Code, Pinco Cazino, Pinco Bet, Pinco Yukl?, Pinco Az?rbaycan, Pinco Casino Giris, Pinco Yukle, Pinco Giris, Pinco APK, Pin Co, Pin Co Casino, Pin-Co Casino. Онлайн-платформа Pinco, включая варианты Pinco AZ, Pinco Casino и Pinco Kazino, предлагает азартные игры в Азербайджане, также известная как Pinco Azerbaycan и Pinco Gazino Casino. Pinco предоставляет промокоды, а также варианты, такие как Pinco Cazino и Pinco Bet. Пользователи могут загрузить приложение Pinco (Pinco Yukl?, Pinco Yukle) для доступа к Pinco Az?rbaycan и Pinco Casino Giris. Pinco Giris доступен через Pinco APK. Pin Co и Pin-Co Casino — это связанные термины.
jasminelle gГ©nГ©rique prix: viagra achat en ligne – betamethasone sans ordonnance prix
viagra pour homme en pharmacie sans ordonnance vente viagra pharmacie en ligne sans ordonnance belgique
clairial serum: diurГ©tique sans ordonnance en pharmacie – amoxicilline sans ordonnance prix
jasminelle gГ©nГ©rique prix: acheter tadalafil 5mg en ligne – faire une radio sans ordonnance
https://pharmacieexpress.shop/# liste des mГ©dicaments sur ordonnance sГ©curisГ©e
donde comprar productos de farmacia online tiadipona farmacia online comprar ventolase sin receta
farmacia via crispi: Farmacia Subito – aerius 5 mg prezzo
mi farmacia tienda online: mifepristona se puede comprar sin receta medica – farmacia online cГЎdiz
farmacia online alemana Confia Pharma como comprar antibiotico sin receta
antibiotiques infection urinaire sans ordonnance: verrue plantaire traitement pharmacie sans ordonnance – acheter ozempic en ligne sans ordonnance
comprar vacuna gripe sin receta: Confia Pharma – creaciГіn de farmacia online
нова версия мода тик ток Мир мобильных приложений не стоит на месте, и Тик Ток продолжает оставаться одной из самых популярных платформ для создания и обмена короткими видео. Но что, если стандартной функциональности вам недостаточно? На помощь приходит Тик Ток Мод – модифицированная версия приложения, открывающая доступ к расширенным возможностям и эксклюзивным функциям.
https://pharmacieexpress.com/# louer bГ©quille pharmacie sans ordonnance prix
se puede comprar enalapril sin receta: donde comprar nitrofurantoina sin receta – se puede comprar anticonceptivos orales sin receta
medicament pour rage de dent sans ordonnance cialis 10mg par quoi remplacer lexomil sans ordonnance
Предлагаем услуги профессиональных инженеров офицальной мастерской.
Еслли вы искали ремонт холодильников gorenje, можете посмотреть на сайте: срочный ремонт холодильников gorenje
Наши мастера оперативно устранят неисправности вашего устройства в сервисе или с выездом на дом!
Г©quivalent du solupred sans ordonnance: Pharmacie Express – eau de rose sanoflore
omeprazole sans ordonnance en pharmacie pharmacie medicament sans ordonnance avene lotion micellaire
liste des somniferes sans ordonnance en pharmacie en france: peut on faire un test pcr en pharmacie sans ordonnance – remboursement doliprane sans ordonnance
Thank you for your sharing. I am worried that I lack creative ideas. It is your article that makes me full of hope. Thank you. But, I have a question, can you help me?
http://confiapharma.com/# farmacia online aviles
farmacia natural online: farmacia tei online contact – farmacia online opinion
se puede comprar lorazepam sin receta en farmacias la farmacia mas barata online farmacia veterinaria comprar online
proviron farmacia online: Confia Pharma – puedo comprar estrogenos sin receta
atenololo 50 mg prezzo: dona bustine 1500 mg prezzo – cacit 1000
zolpidem ordonnance sГ©curisГ©e Pharmacie Express acheter sildenafil
oferty pracy dla Ukrainek w Polsce Стань вебкам моделью в польской студии, работающей в Варшаве! Открыты вакансии для девушек в Польше, особенно для тех, кто говорит по-русски. Ищешь способ заработать онлайн в Польше? Предлагаем подработку для девушек в Варшаве с возможностью работы в интернете, даже с проживанием. Рассматриваешь удаленную работу в Польше? Узнай, как стать вебкам моделью и сколько можно заработать. Работа для украинок в Варшаве и высокооплачиваемые возможности для девушек в Польше ждут тебя. Мы предлагаем легальную вебкам работу в Польше, онлайн работа без необходимости знания польского языка. Приглашаем девушек без опыта в Варшаве в нашу вебкам студию с обучением. Возможность заработка в интернете без вложений. Работа моделью онлайн в Польше — это шанс для тебя! Ищешь “praca dla dziewczyn online”, “praca webcam Polska”, “praca modelka online” или “zarabianie przez internet dla kobiet”? Наше “agencja webcam Warszawa” и “webcam studio Polska” предлагают “praca dla mlodych kobiet Warszawa” и “legalna praca online Polska”. Смотри “oferty pracy dla Ukrainek w Polsce” и “praca z domu dla dziewczyn”.
farmacia online duodart: mejor farmacia online madrid – la pildora del dia despues se puede comprar sin receta
mГ©dicament cystite ordonnance medicament pour prostate sans ordonnance pilule pharmacie sans ordonnance
https://farmaciasubito.com/# farmacia online foggia
сбербанк заказать дебетовую карту онлайн Ваш проводник в мире удобных банковских карт Оформление современной дебетовой карты теперь стало простым и доступным благодаря нашей группе. Вы сможете легко выбрать карту, подходящую именно вам, и воспользоваться всеми преимуществами современного финансового сервиса. Что мы предлагаем? Полезные советы: Лайфхаки и рекомендации по эффективному использованию вашей карты. Актуальные акции: Будьте в курсе всех новых предложений и специальных условий от банков-партнеров. Преимущества нашего сообщества Здесь вы найдете всю необходимую информацию о различных видах карт, особенностях тарифов и комиссий. Наши публикации регулярно обновляются, предоставляя актуальные данные и свежие новости о продуктах российских банков. Присоединяйтесь к нашему сообществу, чтобы сделать ваши финансовые решения простыми, быстрыми и надежными. Вместе мы сможем оптимизировать использование банковских продуктов и сэкономить ваше время и средства. Ведь наша цель — помогать вам эффективно управлять своими финансами и получать максимум выгоды от каждого взаимодействия с банком.
farmacia online san marino Farmacia Subito farmacia via filippo di giovanni
Thank you for your sharing. I am worried that I lack creative ideas. It is your article that makes me full of hope. Thank you. But, I have a question, can you help me?
rybelsus mexico online mexican pharmacy desoxyn cheap prescriptions online
indian pharmacy: InPharm24 – india online pharmacy
https://pharmmex.shop/# pharmacy in mexico
sams club pharmacy propecia asacol online pharmacy 24 7 pharmacy online
легальная вебкам работа в Польше Стань вебкам моделью в польской студии, работающей в Варшаве! Открыты вакансии для девушек в Польше, особенно для тех, кто говорит по-русски. Ищешь способ заработать онлайн в Польше? Предлагаем подработку для девушек в Варшаве с возможностью работы в интернете, даже с проживанием. Рассматриваешь удаленную работу в Польше? Узнай, как стать вебкам моделью и сколько можно заработать. Работа для украинок в Варшаве и высокооплачиваемые возможности для девушек в Польше ждут тебя. Мы предлагаем легальную вебкам работу в Польше, онлайн работа без необходимости знания польского языка. Приглашаем девушек без опыта в Варшаве в нашу вебкам студию с обучением. Возможность заработка в интернете без вложений. Работа моделью онлайн в Польше — это шанс для тебя! Ищешь “praca dla dziewczyn online”, “praca webcam Polska”, “praca modelka online” или “zarabianie przez internet dla kobiet”? Наше “agencja webcam Warszawa” и “webcam studio Polska” предлагают “praca dla mlodych kobiet Warszawa” и “legalna praca online Polska”. Смотри “oferty pracy dla Ukrainek w Polsce” и “praca z domu dla dziewczyn”.
online pharmacy nizoral: Pharm Express 24 – baclofen uk pharmacy
Luke Skywalker later learned about Momin and his historical past during his travels throughout the galaxy, and described the Sith Lord’s role in constructing Vader’s fortress in his e-book, titled The Secrets of the Jedi.
can you buy percocet in mexico Pharm Mex pharmacy store online
http://pharmmex.com/# apteka usa online
lorazepam mexican pharmacy: drugs for sale online – can i buy viagra in mexico and bring it to the us
top online pharmacy in india: india mart pharmacy – e pharmacy in india
diflucan online pharmacy review online pharmacy pharmacy coupons
india medicine: InPharm24 – top online pharmacy in india
b pharmacy fees in india: pharmacy name ideas in india – prescription drugs from india
https://pharmexpress24.shop/# united kingdom online pharmacy
india online pharmacy online india pharmacy india pharmacy website
medicine order online: medicines online shopping – can you get ozempic over the counter in mexico
prednisone mexico: Pharm Mex – mexican pharmacy websites
india pharmacy website online pharmacy in india india pharmacy website
pharmacy website in india: order medicines online – medicine from india
готовые игровые компьютеры Сборка компьютеров на заказ: Ваш путь к идеальной машине В мире, где технологии развиваются с головокружительной скоростью, выбор компьютера становится задачей, требующей особого внимания. Готовые решения не всегда отвечают индивидуальным потребностям, и здесь на помощь приходит сборка компьютеров на заказ. Это возможность создать машину, идеально подходящую для ваших задач, будь то игры, работа или стриминг.
https://pharmexpress24.shop/# gen rx pharmacy
medicines online india top online pharmacy in india pharmacy names in india
medical store online: india online pharmacy – divya pharmacy india
quality rx pharmacy hyde park ma pharmacy store hours target pharmacy cephalexin
amlodipine pharmacy prices: acyclovir target pharmacy – buying online pharmacy
good article please join my site bro yaa ..
central rx pharmacy: Pharm Express 24 – clozapine pharmacy registry
mexican water pills Pharm Mex medicine online usa
https://pharmexpress24.com/# Lamictal
prescriptions from india: apotheke academy – reliable pharmacy india
Предлагаем услуги профессиональных инженеров офицальной мастерской.
Еслли вы искали ремонт кофемашин philips, можете посмотреть на сайте: ремонт кофемашин philips рядом
Наши мастера оперативно устранят неисправности вашего устройства в сервисе или с выездом на дом!
retin a mexico pharmacy prescriptions in mexico what to buy at a mexican pharmacy
pharmacy rx by crystal zamudio: Pharm Express 24 – generic cialis online pharmacy reviews
list of pharmacies in india: InPharm24 – india mail order pharmacy
Any Indian user above 18 years of age can start playing Jet X. This page contains basic information on how to register via phone number, email and social media and also gives detailed instructions on how to verify your account. It is always a good idea to read the terms and conditions of each promo code before using it. This will ensure that you understand the requirements and restrictions. In most cases, promo codes are a great way to get started with JetX Game. Maximize your chances of winning in Aviator by following these tips: One of the most popular promo codes for our game is a deposit bonus. This is the accumulation of additional funds to the user’s personal account when certain conditions are met. This bonus is applied to your first deposit. This means that you can use the promo code the moment you make your first deposit into your internal account. There are also promo codes for free spins, which are more typical for the classic type of machines and slots. After entering the promo code in the special window of the form, the bonus will be automatically credited to your account.
https://fundidoanegro.com/uncategorized/review-balloon-game-by-smartsoft-free-play-vs-paid-modes-in-indian-online-casinos/
A free app for Android, by HDuo Fun Games. The hottest Roulette game show with multipliers up to 2,500x! The game is easy to learn and play, making it accessible to everyone. The objective of the game is to predict which hand, the Dragon or the Tiger, will have the highest card. You can get up to 1000 free chips every 2 minutes, and you can also earn free chips by watching ads. I will do real money rummy game blackjack dragon vs tiger bet app cards ludo crash game Savings are based on the price of the yearly plan paid upfront compared to the monthly plan paid over 12 months. Ads served on select live and linear content on Standard and Premium Plans. Live Sports and CNN Max available only on select plans. Plan availability varies by subscription provider. Check with your subscription provider for details. Select games available and blackouts may apply. Download limits apply to certain content categories. See max information for more.
accutane online pharmacy reviews best online pharmacies no prescription global online pharmacy
Профессиональный сервисный центр по ремонту Apple iPhone в Москве.
Мы предлагаем: ремонт айфонов на дому в москве
Наши мастера оперативно устранят неисправности вашего устройства в сервисе или с выездом на дом!
https://pharmmex.shop/# national spine pain centers
viagra online pharmacy us study pharmacy online free thailand pharmacy online
is tramadol otc in mexico: Pharm Mex – doxycycline mexican pharmacy
online us pharmacy viagra: buy sildenafil without prescription – sildenafil buy online canada
20mg sildenafil: VGR Sources – best viagra pills
sildenafil daily use: VGR Sources – buy viagra 500mg
https://vgrsources.com/# sildenafil 5 mg tablet
canadian pharmacy brand viagra: VGR Sources – where to buy viagra online uk
generic viagra usa: VGR Sources – how to get viagra tablets
purchase viagra online from canada: order viagra from canada – buy viagra over the counter in australia
купить игровой ПК
viagra 100 price: purchase viagra over the counter – viagra 100mg buy online
také jsem si vás poznamenal, abych se podíval na nové věci na vašem blogu.|Hej! Vadilo by vám, kdybych sdílel váš blog s mým facebookem.
can i buy viagra online without a prescription: canada viagra buy – order viagra online canada mastercard
medication viagra online: VGR Sources – viagra tabs
https://vgrsources.com/# viagra online nz
discount pharmacy sildenafil: VGR Sources – sildenafil 100mg canada
sildenafil 88: online viagra prescription usa – female viagra buy australia
drugstore female viagra: VGR Sources – where can i order real viagra
Can you be more specific about the content of your article? After reading it, I still have some doubts. Hope you can help me.
море хургада
viagra without a rx: VGR Sources – generic viagra soft
prescription female viagra: VGR Sources – female viagra australia where to buy
female viagra prescription: viagra canadian pharmacy – viagra tablets online australia
https://vgrsources.com/# 200 mg viagra for sale
buy generic 100mg viagra online: viagra 1 tablet price – how to viagra online
viagra 100mg cost in india: best viagra online australia – buy female viagra uk online
buy sildenafil online uk: how to buy viagra in australia – viagra without prescription in united states
buy viagra soft cheap generic viagra from canada best generic viagra prices
this is a great post!
It contains fastidious material.|I think the admin of this website is actually working hard in favor of his site,
where can i buy viagra in canada: canadian prices for sildenafil – how much is sildenafil 50 mg
this is a great post!
sildenafil india purchase: VGR Sources – sildenafil prescription discount
this is a great post!
sildenafil price in india: VGR Sources – discount pharmacy sildenafil
can you buy viagra online in canada: order sildenafil online uk – sildenafil price comparison uk
https://vgrsources.com/# viagra generic 50 mg
Hi there I am so thrilled I found your webpage, I really found you by accident, while I was researching on Digg for something else, Regardless I am here now and would just like to say cheers for a marvelous post and a all round thrilling blog (I also love the theme/design), I don’t have time to read through it all at the minute but I have bookmarked it and also included your RSS feeds, so when I have time I will be back to read a great deal more, Please do keep up the awesome jo.
hafilat card online recharge
sildenafil 100mg price in india: viagra 25 mg daily – viagra online cheap price
BestGold: Сияние золота и блеск бриллиантов в Краснодаре В сердце Краснодарского края, где солнце ласкает поля и виноградники, расцветает мир изысканных ювелирных украшений BestGold. Мы предлагаем вам уникальную возможность прикоснуться к великолепию золота 70% пробы, воплощенному в утонченных кольцах и серьгах, сверкающих бриллиантами. Кольца, достойные королевы Наши кольца – это не просто украшения, это символ вашей индивидуальности и безупречного вкуса. От классических обручальных колец до экстравагантных коктейльных, каждое изделие BestGold создано с любовью и вниманием к деталям. Вставки из бриллиантов различной огранки и каратности подчеркнут вашу элегантность и добавят образу неповторимый шарм. Ювелирные украшения fix-55% Краснодарский край Серьги, подчеркивающие красоту Серьги BestGold – это идеальное дополнение к любому наряду. От лаконичных пусетов до эффектных подвесок, они призваны подчеркнуть вашу женственность и утонченность. Наши серьги с бриллиантами станут ярким акцентом вашего образа, притягивая восхищенные взгляды. Ювелирный фестиваль BestGold: праздник роскоши и стиля Не упустите возможность стать участником ювелирного фестиваля BestGold, где вас ждут эксклюзивные скидки на золото до 70% и невероятные предложения на бриллианты. Это ваш шанс приобрести ювелирные украшения мечты по самым выгодным ценам. BestGold: выбирайте лучшее, выбирайте золото! Погрузитесь в мир роскоши и блеска вместе с BestGold. Наши ювелирные украшения станут вашими верными спутниками, подчеркивая вашу красоту и элегантность в любой ситуации. Купите кольцо или серьги из золота в Краснодаре и ощутите себя королевой!
Can you be more specific about the content of your article? After reading it, I still have some doubts. Hope you can help me.
generic viagra sildenafil: VGR Sources – buy generic viagra 100mg
viagra canada purchase: VGR Sources – where to buy cheap viagra in usa
viagra online from india: VGR Sources – viagra 100mg online in india
viagra generics: sildenafil online prices – viagra free shipping canada
where to buy viagra online in india where can i get sildenafil without prescription viagra medicine in india
buy generic viagra online paypal: viagra singapore pharmacy – us pharmacy generic viagra
viagra generics: viagra 200mg online – sildenafil citrate medication
https://vgrsources.com/# lowest price viagra
where to buy cheap sildenafil: generic viagra from canada pharmacy – best price viagra uk
can you buy viagra in australia sildenafil prescription prices cheap viagra 100mg uk
viagra gel for sale: where can i get viagra – buy 90 sildenafil 100mg price
кайтсёрфинг в анапе Кайтсерфинг в Анапе – это стиль жизни, который выбирают смелые и энергичные люди.
viagra uk fast delivery: VGR Sources – buy online viagra
generic viagra for daily use: viagra cheapest – generic viagra prescription
generic viagra united states VGR Sources generic viagra online united states
sildenafil buy paypal: buy viagra medicine online india – purchase viagra safely online
viagra samples: buy viagra over the counter usa – cheapest soft viagra soft on line
sildenafil capsule: VGR Sources – viagra pills price in south africa
https://vgrsources.com/# best generic viagra online
400 mg sildenafil: cheap viagra fast delivery – buy sildenafil from canada
Conhecem algum método para ajudar a evitar que o conteúdo seja roubado? Agradecia imenso.
buy viagra soft online: VGR Sources – over the counter viagra united states
sildenafil best price: where can you get women’s viagra – buy brand viagra online australia
viagra generic uk: VGR Sources – sildenafil 100mg from india
Můžete mi doporučit nějaké další blogy / webové stránky / fóra, které se zabývají stejnými tématy?
sildenafil 100mg price india: 20 mg sildenafil cost – viagra professional cheap
sildenafil 100: sildenafil otc australia – viagra online purchase in india
https://vgrsources.com/# viagra pills for sale uk
buy viagra online usa VGR Sources can i buy generic viagra
where to buy viagra pharmacy: VGR Sources – sildenafil australia buy
cheap prices for viagra: sildenafil medicine in india – viagra in usa prescription
mexico viagra prices: VGR Sources – buy female viagra pills
how long does it take for semaglutide to work: can you take rybelsus and mounjaro at the same time – Order Rybelsus discreetly
rybelsus contraindications: Semaglu Pharm – No prescription diabetes meds online
Rybelsus 3mg 7mg 14mg: Semaglu Pharm – semaglutide drug class
https://prednipharm.com/# PredniPharm
Semaglu Pharm: Rybelsus side effects and dosage – Rybelsus 3mg 7mg 14mg
Predni Pharm: PredniPharm – prednisone where can i buy
CrestorPharm: side effects from rosuvastatin – Crestor Pharm
I used to be able to find good advice from your blog articles.
hafilat bus card recharge
direct meds semaglutide: Affordable Rybelsus price – SemagluPharm
prednisone cream brand name: canadian online pharmacy prednisone – 15 mg prednisone daily
Order Rybelsus discreetly SemagluPharm Semaglu Pharm
Crestor Pharm: Crestor Pharm – CrestorPharm
http://lipipharm.com/# Lipi Pharm
Predni Pharm: Predni Pharm – buy prednisone nz
Semaglu Pharm: No prescription diabetes meds online – Semaglu Pharm
Lipi Pharm: Lipi Pharm – Discreet shipping for Lipitor
LipiPharm: LipiPharm – LipiPharm
http://crestorpharm.com/# CrestorPharm
Crestor Pharm rosuvastatin and brain fog Affordable cholesterol-lowering pills
common side effects of rosuvastatin: Crestor Pharm – Crestor Pharm
Predni Pharm: PredniPharm – PredniPharm
does rosuvastatin 10 mg raise blood sugar: Crestor Pharm – cholesterol medicine rosuvastatin side effects
PredniPharm 6 prednisone Predni Pharm
Lucky Jet é uma crash game inovadora que vem ganhando popularidade rapidamente em cassinos online. Com sua mecânica simples e emocionante, o jogo cativa jogadores que buscam diversão e a chance de grandes ganhos. Neste guia, exploraremos as regras, estratégias e características únicas que fazem do Lucky Jet um dos favoritos entre os apostadores. O Luckyjet é um jogo de apostas popular que se assemelha ao lendário “Aviator”. O tocar está ganhando popularidade rapidamente no Brasil e nos cassinos 1win. Registre-se e ganhe bônus para um começo confortável! Lucky Jet é um jogo viciante desenvolvido pela GambleTech. O jogo oferece aos jogadores a oportunidade de ganhar quantias impressionantes de dinheiro em um curto espaço de tempo. O RTP do Lucky Jet é de 96%, o que garante aos jogadores uma parte de suas apostas no longo prazo. Lucky Jet Brasil está disponível na plataforma de cassino online 1Win desenvolvida pelo software GambleTech.
https://gamehay.today/sweet-bonanza-da-pragmatic-play-analise-da-popularidade-no-brasil/
Gostaríamos de destacar que, de vez em quando, um programa de software potencialmente mal-intencionado pode não ser encontrado. Para continuar prometendo a você um catálogo de programas e apps livre de malware, nossa equipe incluiu o recurso Report Software (Relatar software) em cada página de catálogo que encaminha seu feedback de volta para nós. Important predictions WHATSAPP lucky-jet-win.br © Site oficial do jogo 1win lucky jet. | TRADIÇÃO EM TALENTO | +55 71 3037 2523 | TRADIÇÃO EM TALENTO | Tamanho do arquivo WHATSAPP Important predictions Tamanho do arquivo Embora o Predictor Aviator não seja perfeito, ele definitivamente melhora suas chances de ganhar no jogo de apostas cada vez mais popular. Ao fornecer previsões, o aplicativo impulsionado por algoritmos realmente aumenta sua confiança em manter suas apostas para obter mais ganhos. Embora não suporte prontamente todas as plataformas de apostas de Aviação, ele permite que você acesse as grandes ligas. Requer uma conta e um depósito, e você está pronto para começar.
PredniPharm: prednisone 50 mg canada – Predni Pharm
Semaglu Pharm: Semaglu Pharm – Semaglu Pharm
http://prednipharm.com/# PredniPharm
rybelsus cost without insurance SemagluPharm No prescription diabetes meds online
prednisone 50: Predni Pharm – prednisone 5mg over the counter
Thanks for sharing. I read many of your blog posts, cool, your blog is very good.
CrestorPharm: rosuvastatin and fenofibrate tablets – Over-the-counter Crestor USA
Lipi Pharm: atorvastatin 80 mg side effects – does lipitor reduce plaque
vykřiknout a říct, že mě opravdu baví číst vaše příspěvky na blogu.
Safe atorvastatin purchase without RX: atorvastatin price without insurance – what is atorvastatin good for
USA-based pharmacy Lipitor delivery: LipiPharm – FDA-approved generic statins online
can rybelsus cause diarrhea: Semaglu Pharm – rybelsus insomnia
Affordable Rybelsus price Where to buy Semaglutide legally semaglutide (wegovy)
https://semaglupharm.com/# SemagluPharm
PredniPharm: prednisone 50 mg tablet canada – prednisone canada
https://semaglupharm.shop/# SemagluPharm
Crestor Pharm: rosuvastatin 5 mg vs 10mg – CrestorPharm
SemagluPharm olympia semaglutide Semaglu Pharm
Predni Pharm: prednisone 30 mg daily – PredniPharm
Lipi Pharm: LipiPharm – lipitor skin rash
Great article! That is the type of info that are meant to be shared around the net.Disgrace on the search engines for no longer positioning thispost upper! Come on over and visit my site . Thanks =)
https://prednipharm.com/# prednisone tablets india
this is a great post!
PredniPharm: prednisone 10mg tablets – 100 mg prednisone daily
this is a great post!
FDA-approved Rybelsus alternative: Semaglu Pharm – Rybelsus for blood sugar control
this is a great post!
grupo do facebook? Há muitas pessoas que eu acho que iriam realmente
this is a great post!
this is a great post!
Predni Pharm prednisone 30 Predni Pharm
this is a great post!
prednisone 20 mg in india: order prednisone online no prescription – PredniPharm
Semaglu Pharm: SemagluPharm – SemagluPharm
LipiPharm: Lipi Pharm – LipiPharm
Predni Pharm Predni Pharm PredniPharm
Over-the-counter Crestor USA: Crestor mail order USA – is 5mg of rosuvastatin a low-dose
https://semaglupharm.com/# Semaglu Pharm
Can you be more specific about the content of your article? After reading it, I still have some doubts. Hope you can help me.
60 mg prednisone daily: buy prednisone with paypal canada – prednisone 20mg nz
LipiPharm FDA-approved generic statins online atorvastatin calcium 10mg
http://prednipharm.com/# PredniPharm
Semaglu Pharm: SemagluPharm – semaglutide and breastfeeding
https://semaglupharm.shop/# Semaglu Pharm
2.5 mg semaglutide: get semaglutide online – SemagluPharm
purchase prednisone from india prednisone 100 mg where can i get prednisone
https://semaglupharm.com/# semaglutide colorado springs
п»їBuy Crestor without prescription: Crestor Pharm – Crestor Pharm
Consiglio vivamente Ernesto.it come partner affidabile per tutte le soluzioni legate a SOLIDWORKS. La loro competenza e professionalità sono evidenti e garantiscono un supporto efficace per affrontare ogni tipo di esigenza nel campo della simulazione e del design. Con Ernesto.it, la nostra azienda ha migliorato significativamente i processi di sviluppo e di testing, ottimizzando tempi e risorse. La loro assistenza tempestiva e competente ci permette di rimanere sempre aggiornati sulle ultime novità come quelle presentate nell’articolo sui miglioramenti di SOLIDWORKS Simulation 2024. Scegliere Ernesto.it significa affidarsi a un partner che mette le esigenze del cliente al primo posto, offrendo soluzioni innovative e personalizzate. La qualità del loro servizio ci ha dato la sicurezza di poter affrontare con successo le sfide tecniche più complesse, migliorando la nostra competitività sul mercato.
Where to buy Semaglutide legally: Rybelsus 3mg 7mg 14mg – Order Rybelsus discreetly
https://semaglupharm.com/# cheapest semaglutide online
https://lipipharm.shop/# USA-based pharmacy Lipitor delivery
prednisone 10 mg tablet 54 prednisone prednisone 2 5 mg
Semaglu Pharm: SemagluPharm – Semaglu Pharm
https://semaglupharm.shop/# Semaglu Pharm
Predni Pharm: prednisone for sale in canada – Predni Pharm
Affordable cholesterol-lowering pills CrestorPharm CrestorPharm
LipiPharm: Lipi Pharm – LipiPharm
this is a great post!
https://semaglupharm.shop/# Safe delivery in the US
I don’t think the title of your article matches the content lol. Just kidding, mainly because I had some doubts after reading the article.
this is a great post!
LipiPharm: LipiPharm – LipiPharm
side effects to atorvastatin Lipi Pharm Safe atorvastatin purchase without RX
prednisone 40 mg tablet: where to buy prednisone 20mg no prescription – Predni Pharm
this is a great post!
https://lipipharm.com/# lipitor liver damage repair
https://semaglupharm.shop/# SemagluPharm
vykřiknout a říct, že mě opravdu baví číst vaše příspěvky na blogu.
can rosuvastatin cause dementia: Over-the-counter Crestor USA – CrestorPharm
PredniPharm: prednisone online australia – PredniPharm
Predni Pharm PredniPharm PredniPharm
Your article helped me a lot, is there any more related content? Thanks!
https://semaglupharm.shop/# Affordable Rybelsus price
Generic Lipitor fast delivery: nursing interventions for lipitor – Affordable Lipitor alternatives USA
SemagluPharm: SemagluPharm – SemagluPharm
LipiPharm LipiPharm LipiPharm
https://crestorpharm.com/# Crestor home delivery USA
http://semaglupharm.com/# Semaglu Pharm
Lipi Pharm atorvastatin 20 mg reviews Lipi Pharm
PredniPharm: Predni Pharm – buy prednisone 10mg online
lovastatin vs crestor: Crestor home delivery USA – crestor vs lipitor dosage
http://semaglupharm.com/# SemagluPharm
this is a great post!
difference between crestor and lipitor CrestorPharm CrestorPharm
this is a great post!
crestor vs atorvastatin: Buy cholesterol medicine online cheap – rosuvastatin calcium brand name
Safe online pharmacy for Crestor: Crestor Pharm – CrestorPharm
¡Saludos, apasionados del azar !
Casinos sin licencia espaГ±ola sin necesidad de ID – https://casinossinlicenciaenespana.es/ casino online sin licencia espaГ±a
¡Que vivas oportunidades exclusivas !
this is a great post!
https://semaglupharm.com/# rybelsus cost in mexico
http://lipipharm.com/# atorvastatin manufacturers in usa
Crestor mail order USA Buy statins online discreet shipping Online statin therapy without RX
Crestor Pharm: Order rosuvastatin online legally – Crestor Pharm
does medicaid cover semaglutide: SemagluPharm – semaglutide constipation
http://semaglupharm.com/# Semaglu Pharm
Online statin drugs no doctor visit: Online statin drugs no doctor visit – Lipi Pharm
Semaglu Pharm semaglutide compound dosage chart can semaglutide cause cancer
http://semaglupharm.com/# Order Rybelsus discreetly
Lipi Pharm: Lipi Pharm – Cheap Lipitor 10mg / 20mg / 40mg
http://canadapharmglobal.com/# pharmacies in canada that ship to the us
http://canadapharmglobal.com/# canada ed drugs
India Pharm Global India Pharm Global India Pharm Global
canadapharmacyonline: Canada Pharm Global – northwest canadian pharmacy
Meds From Mexico: Meds From Mexico – Meds From Mexico
https://canadapharmglobal.shop/# best online canadian pharmacy
Meds From Mexico: Meds From Mexico – purple pharmacy mexico price list
canadian pharmacy online ship to usa Canada Pharm Global canadian pharmacy checker
best rated canadian pharmacy: Canada Pharm Global – reputable canadian online pharmacy
http://indiapharmglobal.com/# top online pharmacy india
http://canadapharmglobal.com/# canadian pharmacy review
purple pharmacy mexico price list: Meds From Mexico – Meds From Mexico
India Pharm Global top 10 online pharmacy in india India Pharm Global
canadapharmacyonline: northwest pharmacy canada – canadadrugpharmacy com
¡Saludos, descubridores de oportunidades !
Mejores casinos online extranjeros para tragamonedas – https://www.casinosextranjerosenespana.es/ mejores casinos online extranjeros
¡Que vivas increíbles jackpots extraordinarios!
http://medsfrommexico.com/# Meds From Mexico
indian pharmacy paypal: best online pharmacy india – indian pharmacy online
India Pharm Global best india pharmacy cheapest online pharmacy india
canadian pharmacy no scripts: canadian drugstore online – reddit canadian pharmacy
https://canadapharmglobal.shop/# buying from canadian pharmacies
http://canadapharmglobal.com/# best canadian pharmacy online
mexican drugstore online: Meds From Mexico – Meds From Mexico
canadian pharmacy best canadian pharmacy online canadian pharmacy 24
medicine in mexico pharmacies: Meds From Mexico – Meds From Mexico
https://indiapharmglobal.com/# India Pharm Global
canada drug pharmacy: reputable canadian online pharmacies – canadian pharmacies online
Umożliwia przechowywanie danych powiązanych z reklamami oraz wysyłanie danych użytkownika w celach związanych z reklamami online. Jeśli wpłacisz od 30 do 199 PLN, to dostaniesz 125% bonusu oraz 50 darmowych spinów na Ice Mania. A dla wyższej kwoty bonus rośnie do 200% do 2800 PLN oraz 100 darmowych spinów dla slotu Starburst. Kasyno 1win zapewnia wiele wygodnych sposobów wpłaty, aby zagrać w Aviator slot 1win.͏ A lista płatności zależy od kraju. Możesz być pewien, że niezależnie od kraju, którego jesteś obywatelem i rezydentem, zawsze znajdziesz najpopularniejsze systemy płatności na stronie 1win. Jednorazowy zakup: 81,66 zł Minimаlnа stаwkа zаkłаdu w 1Win Plinkօ wуnօsi 0,1 USD lub równօwаrtօść tеj kwօtу w innеj wаluсiе. Mаksуmаlnу zаkłаd niе mօżе przеkrօсzуć 100 USD lub równօwаrtօśсi tеj kwօtу. Pаmiętаj, żе limitу różnią się w zаlеżnօśсi օd wуbrаnеj wеrsji Plinkօ.
http://jobs.emiogp.com/author/akanerroe1971/
Usamos cookies para ayudarle a navegar de manera eficiente y realizar ciertas funciones. Encontrará información detallada sobre cada una de las cookies bajo cada categoría de consentimiento a continuación. medicine in mexico pharmacies: mexican pharmacy – mexican border pharmacies shipping to usa aviator игра на деньги скачать 1win14005.ru . POLÍTICA DE COOKIES Zazwyczaj 800–1200 balloon 1win apk balloon 1win apk . 1win download apk 1win download apk . AVISO LEGAL AVISO LEGAL Найдите РїСЂРѕРјРѕРєРѕРґ ANDROID777 для 7k Casino Рё скачайте APK через телеграм канал, чтобы начать РёРіСЂСѓ t.me casino_7kk
India Pharm Global online pharmacy india India Pharm Global
https://canadapharmglobal.shop/# canada pharmacy 24h
maple leaf pharmacy in canada: is canadian pharmacy legit – legit canadian online pharmacy
http://canadapharmglobal.com/# canadian pharmacies online
onlinecanadianpharmacy: Canada Pharm Global – canadian pharmacy victoza
¡Hola, buscadores de riqueza !
Casino online fuera de EspaГ±a con retiro inmediato – п»їп»їhttps://casinoonlinefueradeespanol.xyz/ casino online fuera de espaГ±a
¡Que disfrutes de asombrosas tiradas afortunadas !
mexican drugstore online buying prescription drugs in mexico Meds From Mexico
http://indiapharmglobal.com/# India Pharm Global
pharmacy rx world canada: canadian pharmacy price checker – reliable canadian pharmacy
Meds From Mexico: buying from online mexican pharmacy – mexico pharmacies prescription drugs
http://medsfrommexico.com/# Meds From Mexico
https://indiapharmglobal.com/# online pharmacy india
Meds From Mexico: п»їbest mexican online pharmacies – buying prescription drugs in mexico online
Meds From Mexico: Meds From Mexico – reputable mexican pharmacies online
¡Saludos, amantes de la adrenalina !
CГіmo iniciar sesiГіn en casinoextranjerosenespana.es – https://www.casinoextranjerosenespana.es/ casinos extranjeros
¡Que disfrutes de triunfos épicos !
http://indiapharmglobal.com/# India Pharm Global
apotek ГҐpent julaften: Rask Apotek – apotek levering samme dag
Papa Farma: farmacia tienda – Papa Farma
https://svenskapharma.shop/# filmdragerade tabletter
Papa Farma farmacias cerca de mi abiertas Papa Farma
https://papafarma.shop/# Papa Farma
farmacia europa 7: farmacia b – movicol necesita receta
Svenska Pharma: Svenska Pharma – smГ¤rtstillande munskГ¶lj
http://efarmaciait.com/# drovelis compresse
testosteron tilskudd apotek næringsdrikk apotek Rask Apotek
farmacia sevilla este: Papa Farma – parafarmacias on line
forstГёverapparat apotek: Rask Apotek – Rask Apotek
https://raskapotek.com/# Rask Apotek
http://raskapotek.com/# billigst apotek pГҐ nett
dalacin t opinioni EFarmaciaIt EFarmaciaIt
Papa Farma: fwrmacia – pagina web farmacia
https://svenskapharma.shop/# Svenska Pharma
Papa Farma para quГ© sirve movicol elocom crema precio espaГ±a
Papa Farma: durex lubricante natural opiniones – capital farma
EFarmaciaIt: EFarmaciaIt – lucen bustine pediatriche
https://svenskapharma.shop/# klorhexidin schampo hund apotek
http://svenskapharma.com/# Svenska Pharma
Rask Apotek oksalsyre apotek visir apotek
shampoo apotek: Svenska Pharma – Svenska Pharma
https://papafarma.shop/# pastillas cariban precio
Rask Apotek: Rask Apotek – massasje olje apotek
¡Saludos, participantes del juego !
casinosextranjero.es – accede desde cualquier dispositivo – https://www.casinosextranjero.es/# casino online extranjero
¡Que vivas increíbles victorias épicas !
eritritolo dove si compra EFarmaciaIt EFarmaciaIt
Svenska Pharma: apotek app – apotek hemleverans idag
https://papafarma.shop/# Papa Farma
Svenska Pharma: bestГ¤ll hem covid test – lika delar apotek
https://raskapotek.com/# kviseplaster apotek
iraltone champГє opiniones: eucerin anti-pigment serum opiniones – Papa Farma
¡Hola, descubridores de oportunidades!
Mejores casinos online extranjeros sin restricciones – https://www.casinoextranjero.es/ casino online extranjero
¡Que vivas conquistas brillantes !
apotek kreatin antikroppstest apotek Svenska Pharma
http://papafarma.com/# Papa Farma
EFarmaciaIt: EFarmaciaIt – EFarmaciaIt
http://papafarma.com/# Papa Farma
tea tree olje apotek: Rask Apotek – Rask Apotek
a-vitamin krem apotek fiber apotek Rask Apotek
efarma ГЁ affidabile: pastiglie per – EFarmaciaIt
http://svenskapharma.com/# paracetamol pris
https://efarmaciait.com/# EFarmaciaIt
Svenska Pharma: Svenska Pharma – mГ¤ta blodtryck pГҐ apotek
tu parafarmacia farmacias getafe parafarmacia en sevilla
apotek 24/7: Rask Apotek – neti pot apotek
https://efarmaciait.shop/# kamagra oral jelly amazon
Svenska Pharma: Svenska Pharma – hГҐrklippare rea
hitta mina recept Svenska Pharma Svenska Pharma
Awsome article and straight to the point. I am not sure if this is in fact the best place to ask but do you people have any ideea where to hire some professional writers? Thank you 🙂
https://papafarma.shop/# Papa Farma
кайтсерфинг девушки Сертификат кайтсерфинг — это документ, подтверждающий ваши навыки и знания в области кайтинга. Он может быть выдан после успешного завершения курса обучения в кайт школе. Наличие сертификата открывает новые возможности для занятий кайтингом.
https://papafarma.com/# Papa Farma
Rask Apotek: аптека норвегия – Rask Apotek
EFarmaciaIt: diflucan 150 costo – EFarmaciaIt
tГҐdelare apotek Svenska Pharma svamp tassar hund apotek
I don’t think the title of your article matches the content lol. Just kidding, mainly because I had some doubts after reading the article.
https://efarmaciait.com/# EFarmaciaIt
PharmaJetzt: internetapotheke – Pharma Jetzt
http://medicijnpunt.com/# Medicijn Punt
https://pharmaconnectusa.com/# mogadon online pharmacy
¡Bienvenidos, entusiastas del azar !
Casino fuera de EspaГ±a con promociones activas – https://www.casinoporfuera.guru/# п»їcasino fuera de espaГ±a
¡Que disfrutes de maravillosas triunfos legendarios !
baclofen river pharmacy: online pharmacy paypal – pharmacy global rx reviews
http://medicijnpunt.com/# Medicijn Punt
apotheek recept MedicijnPunt MedicijnPunt
pharmacie allemagne: Pharma Confiance – Pharma Confiance
Pharma Connect USA: mexican pharmacy online – heb online pharmacy
https://pharmaconfiance.shop/# pharmacie Ã
marque pharmacie Pharma Confiance pharmacie sa
http://pharmaconnectusa.com/# Pharma Connect USA
Pharma Connect USA: PharmaConnectUSA – Pharma Connect USA
Can you be more specific about the content of your article? After reading it, I still have some doubts. Hope you can help me.
Do you have any video of that? I’d care to find out more details.
Weapon
apotheek medicijnen: apotheek medicijnen – online pharmacy
https://pharmajetzt.shop/# Pharma Jetzt
shop apothe apotheken mediherz versandapotheke online shop bestellen
¡Saludos, exploradores de recompensas !
casino online fuera de EspaГ±a sin spam – https://www.casinosonlinefueraespanol.xyz/# casino online fuera de espaГ±a
¡Que disfrutes de recompensas asombrosas !
eu pharmacy avis: Pharma Confiance – Pharma Confiance
rx unlimited pharmacy: advair pharmacy price – PharmaConnectUSA
https://pharmajetzt.shop/# Pharma Jetzt
https://medicijnpunt.com/# Medicijn Punt
Pharma Jetzt PharmaJetzt Pharma Jetzt
MedicijnPunt: online apotheek nederland met recept – MedicijnPunt
le chat gel douche: Pharma Confiance – Pharma Confiance
https://pharmaconfiance.com/# Pharma Confiance
tadalafil 10 mg avis Pharma Confiance Pharma Confiance
Pharma Jetzt: 0nline apotheke – Pharma Jetzt
¡Hola, aventureros del riesgo !
Mejores bingos en casinos online extranjeros – https://casinosextranjerosdeespana.es/# casinos extranjeros
¡Que vivas increíbles jackpots sorprendentes!
https://pharmajetzt.com/# apotheken
pharmacie notre dame: Pharma Confiance – exemple ordonnance bas de contention
https://pharmajetzt.shop/# Pharma Jetzt
apteka holandia online apotheek 24 pharmacy nl
PharmaJetzt: sanicare apotheke online bestellen – Pharma Jetzt
https://pharmaconnectusa.com/# first medicine online pharmacy store reviews
apoteke: onlineapothele – Pharma Jetzt
Pharma Confiance Pharma Confiance Pharma Confiance
https://pharmaconfiance.com/# différence entre parapharmacie et pharmacie
MedicijnPunt: MedicijnPunt – Medicijn Punt
пластиковые шторы Шторы на пластиковых окнах – это не только красиво, но и практично. Они защищают от солнца, сохраняют тепло и создают уют. Шторы фото
https://pharmaconfiance.com/# Pharma Confiance
application grossesse taille animaux god ceinture pas cher gdc expertise
http://pharmaconnectusa.com/# PharmaConnectUSA
Secnidazole: PharmaConnectUSA – Pharma Connect USA
shop apotheke auf rechnung: apotheke online ohne versandkosten – bad apotheke online shop
apotheek medicijnen bestellen Medicijn Punt MedicijnPunt
gГјnstig online apotheke: gГјnstige online apotheke auf rechnung – PharmaJetzt
Натяжной потолок в зал Окна ПВХ в Малаховке – это надежная защита от холода и шума, а также современный внешний вид вашего дома. Окна ПВХ Жуковский
¡Bienvenidos, participantes del desafío !
Casino fuera de EspaГ±a con giros gratis semanales – https://www.casinofueraespanol.xyz/ casinofueraespanol
¡Que vivas increíbles botes deslumbrantes!
аккаунты варфейс Варфейс купить
https://pharmaconfiance.shop/# Pharma Confiance
MedicijnPunt medicijnen zonder recept Medicijn Punt
https://pharmaconnectusa.shop/# Pharma Connect USA
PharmaJetzt: apotal online – shop apotheke versandapotheke
Sykaaa casino бонусы Загрузите бесплатное приложение Sykaaa Casino на свой телефон и наслаждайтесь азартом в любое удобное для вас время. Простота установки и оптимизированный интерфейс обеспечат комфортную игру. Sykaaa Casino Отзывы
caudalie bruxelles: dante discount – mycose nez chat
http://medicijnpunt.com/# MedicijnPunt
Pharma Jetzt online apothke Pharma Jetzt
Pharma Connect USA: PharmaConnectUSA – Pharma Connect USA
PharmaJetzt: Pharma Jetzt – Pharma Jetzt
http://medicijnpunt.com/# Medicijn Punt
PharmaJetzt online apotheke selbitz Pharma Jetzt
viagra pour homme prix pharmacie: pharmacie de garde dans l’orne – Pharma Confiance
https://pharmaconfiance.shop/# Pharma Confiance
international pharmacy domperidone: Flomax – wedgewood pharmacy flagyl
https://pharmaconfiance.shop/# parfum pure grace
?Hola, descubridores de oportunidades unicas!
casino online fuera de EspaГ±a con cashback – https://www.casinosonlinefueradeespanol.xyz/# casino online fuera de espaГ±a
?Que disfrutes de asombrosas oportunidades inigualables !
вавада казино официальный сайт рабочее Вавада Казино Официальный Сайт Вход
Pharma Connect USA Finax Pharma Connect USA
apteka nl online: apotheek webshop – MedicijnPunt
¡Saludos, exploradores de la fortuna !
Mejores casinos online extranjeros con gran reputaciГіn – https://www.casinoextranjerosdeespana.es/# casinos extranjeros
¡Que experimentes maravillosas triunfos inolvidables !
PharmaConnectUSA: Pharma Connect USA – cetirizine pharmacy
LengBear 777 – Khmer Games offers flashy visuals with classic casino sound effects, providing users with an immersive gaming experience. At the start, you are given a certain amount of money. It’s up to you how to earn more money. If you lose, you can buy coins through in-app purchases. Gift Media Package Craft 365 Rummy application is a type of gaming platform which has become a means of earning money in India. There are many games available in this application which you can play and earn money. Teen Patti Wolf: A Fun and Addictive Card Game LengBear 777 – Khmer Games is a free casino game where players can play various mini card and slot games. In this wager title, users can play with up to six players, allowing them to go against friends, family, and even strangers online.
https://osrocofol1970.bearsfanteamshop.com/home
Big Bass Bonanza Megaways Connect with us The reel structure uses the Megaways system, which varies the number of symbols in each as well as their size for each spin. In the case of Big Bass Bonanza Megaways, reels 1 and 6 can contain a maximum of 6 symbols. Meanwhile, the remaining reels can contain a maximum of 5 symbols. The highest RTP slots include Mega Joker (99%), Blood Suckers (98%), Starmania (97.86%) and White Rabbit Megaways (97.72%). Most online slots are near 96 percent for RTP. Uk casino Finally, payouts for casinos in united kingdom awesome sound effects and a slew of features that includes Wild. 3Big Bass Bonanza Fruit machine slots Innocently, and it has evolved over time to become one of the most exciting and diverse games in the casino. There are a few key elements to look out for with Big Bass Bonanza Megaways. The fish icon is the Money symbol and these can take a random value. This value can be won during free spins.
http://medicijnpunt.com/# apotheek medicijnen bestellen
MedicijnPunt mijn apotheek online online apotheek goedkoper
Pharma Jetzt: Pharma Jetzt – Pharma Jetzt
Pharma Confiance: Pharma Confiance – Pharma Confiance
http://pharmajetzt.com/# Pharma Jetzt
https://medicijnpunt.com/# internet apotheek nederland
shop apothrke Pharma Jetzt Pharma Jetzt
PharmaJetzt: medikament online – apotal online
https://pharmajetzt.com/# apotheke internet
PharmaConnectUSA: Pharma Connect USA – PharmaConnectUSA
Pharma Confiance Pharma Confiance pharmacie de garde lyon 7 aujourd’hui
online apoteken: apotehke – welche versandapotheke ist die gГјnstigste
http://medicijnpunt.com/# online apotheek frankrijk
billiger apotheke: online pharmacy – Pharma Jetzt
china to dubai Cargo Shipping Companies in UAE: Contributing to the UAE’s Economic Vision.
https://pharmaconfiance.shop/# naproxГЁne sans ordonnance prix
пионы москва Пионы Москва: Ода красоте и элегантности в сердце столицы. Пионы – это символ процветания, любви и благополучия, и они как нельзя лучше отражают атмосферу Москвы. Мы предлагаем широкий выбор пионов, выращенных в лучших питомниках, чтобы каждый бутон был наполнен жизненной силой и энергией. Создайте атмосферу уюта и роскоши в своем доме или офисе с помощью этих великолепных цветов. Пионы – это идеальный способ выразить свои чувства и подарить незабываемые эмоции.
online apotheek nederland met recept: apotheek winkel 24 review – Medicijn Punt
Pharma Confiance Pharma Confiance Pharma Confiance
https://pharmajetzt.shop/# PharmaJetzt
скачать игры без торрента Скачать игры с облака Mail: Играйте в любимые игры без ограничений по времени и месту. Облако Mail – это ваш персональный игровой архив, всегда под рукой. Загружайте, скачивайте и наслаждайтесь играми в любое время и в любом месте, где есть доступ к интернету.
Pharma Jetzt: medikamenten preisvergleich – PharmaJetzt
Hello pursuers of pure air !
Air Purifier Smoke – Top Rated in 2025 – http://bestairpurifierforcigarettesmoke.guru/# what is the best air purifier for cigarette smoke
May you experience remarkable exceptional air purity !
Pharma Confiance: couche pour chien mГўle incontinent – metronidazole avis
Pharma Connect USA mogadon online pharmacy precision pharmacy omeprazole
https://pharmajetzt.com/# apotheken versand
shop apotheke deutschland: Pharma Jetzt – apotheke auf rechnung bestellen
http://pharmaconfiance.com/# Pharma Confiance
https://medicijnpunt.shop/# online apotheker
concerta pharmacy card: which pharmacy has the cheapest viagra – PharmaConnectUSA
Pharma Confiance drakkars parapharmacie Pharma Confiance
Pharma Confiance: Pharma Confiance – Pharma Confiance
https://pharmaconnectusa.shop/# cialis generic online pharmacy
Pharma Connect USA: viagra asda pharmacy – best rated online pharmacy
medikamente sofort liefern bei apotheke bestellen apotheke online
online pharmacy: pharmacy nederlands – Medicijn Punt
http://pharmajetzt.com/# PharmaJetzt
https://pharmajetzt.com/# abotheke
Pharma Connect USA: kamagra pharmacy uk – Sinemet
PharmaJetzt Pharma Jetzt versand apotheke online
PharmaJetzt: Pharma Jetzt – PharmaJetzt
Pharma Jetzt: Pharma Jetzt – PharmaJetzt
https://pharmaconfiance.shop/# Pharma Confiance
Pharma Confiance Pharma Confiance Pharma Confiance
Когда я увидел эту платформу, чувство было таким, будто я переступил грань реальности. Здесь каждая игра — это не просто волнение, а эмоция, которую ты ощущаешь с каждым вращением.
Интерфейс удобен, словно легкое прикосновение направляет тебя от момента к моменту. Операции, будь то депозиты или вывод средств, проходят легко, как поток воды, и это удивляет. А служба помощи всегда отвечает мгновенно, как друг, который никогда не подведёт.
Для меня Селектор онлайн стал миром, где удовольствие и смысл соединяются. Здесь каждый момент — это часть пути, которую хочется создавать снова и снова.
Pharma Confiance: Pharma Confiance – lait en poudre 25 kg grossiste
mijn medicijn bestellen: MedicijnPunt – online apotheek zonder recept
http://pharmajetzt.com/# Pharma Jetzt
http://pharmajetzt.com/# Pharma Jetzt
PharmaJetzt: billige medikamente – PharmaJetzt
medicine online shop: online apotheken gГјnstig – PharmaJetzt
grГ¶Гџte online apotheke arznei gГјnstig online apotheke
температура воды в хургаде в декабре Кайт школа Хургада: Начните свое приключение Кайт школа в Хургаде – это ваш шанс освоить кайтсерфинг в комфортных и безопасных условиях. Профессиональные инструкторы помогут вам сделать первые шаги на воде, а живописные пейзажи Красного моря подарят незабываемые впечатления.
https://pharmajetzt.com/# PharmaJetzt
Medicijn Punt: MedicijnPunt – MedicijnPunt
Pharma Confiance: tadalafil 10 mg boГ®te de 24 prix prГЁs de paris, france – comparatif parapharmacie en ligne
http://pharmajetzt.com/# sofort apotheke
PharmaJetzt apotheke im internet luitpold apotheke bad steben
Pharma Confiance: ketoprofene effet – Pharma Confiance
ремонт стиральных машин алатауский район Найти мастера холодильников Алматы: Помощь в поиске квалифицированного мастера.
Pharma Jetzt: Pharma Jetzt – versandkostenfreie apotheke
https://pharmaconfiance.com/# pharmacie de garde cannes aujourd’hui
online apotehke: PharmaJetzt – medikamente billig
Sykaaa casino бонусы Получите доступ к актуальному рабочему зеркалу Sykaaa Casino на сегодняшний день и наслаждайтесь непрерывной игрой!
good online pharmacy online pharmacy reviews provigil real cialis online pharmacy
новые авто Купить Мерседес: Символ престижа и инноваций Mercedes-Benz – это бренд, ассоциирующийся с престижем, инновациями и высочайшим качеством.
http://pharmajetzt.com/# apoteke online
PharmaConnectUSA: online pharmacy brand viagra – meijer pharmacy cipro
https://pharmaconnectusa.com/# PharmaConnectUSA
Medicijn Punt: MedicijnPunt – Medicijn Punt
https://2bs-2best.at/bs2web_at.html
minimalist home decor Why don’t birds get zapped? This clever science question inspires our minimalist birds on wires art posters. Designed by singer-artist Alesya G, each premium print features silhouetted birds on a power line with a witty caption. These black-and-white wall art pieces are perfect for modern home decor or a kids’ room. Gift playful science and style – browse our bird-wire art prints for unique wall decor today.
internetapotheken: online apotheke de – beste online apotheke
Pharma Connect USA PharmaConnectUSA pharmacy online shopping usa
https://medicijnpunt.shop/# medicijnen bestellen apotheek
shopapotjeke: Pharma Jetzt – Pharma Jetzt
¡Saludos, seguidores de la diversión !
Casino sin licencia con validaciГіn instantГЎnea – п»їaudio-factory.es casino online sin licencia espaГ±a
¡Que disfrutes de asombrosas triunfos inolvidables !
pharmacy nl: Medicijn Punt – Medicijn Punt
mijn apotheek medicijnen: Medicijn Punt – apotheek apotheek
https://pharmajetzt.shop/# PharmaJetzt
https://pharmajetzt.shop/# online apotheken deutschland
target pharmacy ventolin online pharmacy coupon Pharma Connect USA
magnesium pure: Pharma Confiance – Pharma Confiance
Pharma Jetzt: Pharma Jetzt – claras apotheke online
https://pharmajetzt.shop/# Pharma Jetzt
Medicijn Punt: dokter online medicijnen bestellen – п»їmedicijnen bestellen
Medicijn Punt: MedicijnPunt – Medicijn Punt
Pharma Confiance Pharma Confiance fucidine 2
Асфальтировка
https://1-bs2best.lat/blacksprut_zerkalo.html
Phenylnitropropene Ephedrine is often used to produce phenylacetone, a key intermediate in stimulant synthesis. From phenylacetone, substances like methylone, mephedrone (4-MMC), and 3-CMC can be made using methylamine. Phenylnitropropene, derived from nitroethane, is another precursor. A-PVP and 4-methylpropiophenone are also widely used in synthetic drug production. BMK glycidate is commonly used to synthesize controlled substances.
MedicijnPunt: pharmacy nederlands – online apotheek nederland met recept
https://pharmaconnectusa.shop/# can i buy viagra from tesco pharmacy
https://pharmaconfiance.shop/# Pharma Confiance
новое казино с бездепозитным бонусом за регистрацию Бездепозитные бонусы
¡Bienvenidos, estrategas del juego !
Casino sin licencia espaГ±ola y juego seguro – https://www.mejores-casinosespana.es/ casino sin registro
¡Que experimentes maravillosas premios excepcionales !
Pharma Confiance: ghd livraison – Pharma Confiance
PharmaJetzt medikamente bei Pharma Jetzt
https://b2shop.gl/bs2_best_at.html
ordre de pharmacien: grande pharmacie du 15 – Pharma Confiance
¡Saludos, aventureros de la fortuna !
Casino online sin licencia EspaГ±a fГЎcil y rГЎpido – https://emausong.es/# casino sin licencia
¡Que disfrutes de increíbles instantes memorables !
http://medicijnpunt.com/# de online apotheek
provigil online pharmacy no prescription: testosterone cypionate online pharmacy – us pharmacy clomid
Pharma Confiance: Pharma Confiance – parapharmacie paris 18
MedicijnPunt MedicijnPunt MedicijnPunt
https://medicijnpunt.com/# MedicijnPunt
apotek online: Medicijn Punt – Medicijn Punt
https://2-bs2best.lat/blacksprut_zerkalo.html
https://pharmaconnectusa.shop/# adipex online pharmacy reviews
Pharma Connect USA: percocet prices pharmacy – meds online without doctor prescription
PharmaConnectUSA: viagra online us pharmacy – PharmaConnectUSA
бездепозитные казино с выводом денег Бездепозитные бонусы – это как бесплатный билет в мир азарта, возможность испытать удачу, не рискуя собственными средствами. Они привлекают новичков, позволяя им освоиться в казино и попробовать различные игры, прежде чем делать депозит. Это своего рода тест-драйв, позволяющий оценить атмосферу и функциональность платформы. Бездепозитные бонусы в казино
MedicijnPunt Medicijn Punt apotheek on line
https://2-bs2best.art/blaksprut_ssylka.html
https://medicijnpunt.shop/# MedicijnPunt
pharmacie prix: pharmacie et parapharmacie en ligne – pharamacie en ligne
¡Hola, seguidores de la aventura !
Casinos sin licencia con apps para Android y iOS – https://casinosonlinesinlicencia.es/# casinos sin licencia espaГ±a
¡Que vivas increíbles giros afortunados !
vipps canadian pharmacy: CanRx Direct – the canadian drugstore
http://indimedsdirect.com/# pharmacy website india
https://indimedsdirect.com/# best india pharmacy
IndiMeds Direct world pharmacy india Online medicine order
Online medicine order: cheapest online pharmacy india – indian pharmacy online
medicine in mexico pharmacies: TijuanaMeds – mexican online pharmacies prescription drugs
https://tijuanameds.com/# TijuanaMeds
https://bs2bet.at
reputable indian pharmacies indian pharmacy paypal IndiMeds Direct
canadianpharmacymeds: CanRx Direct – legal to buy prescription drugs from canada
п»їbest mexican online pharmacies: TijuanaMeds – mexican online pharmacies prescription drugs
https://indimedsdirect.com/# pharmacy website india
http://indimedsdirect.com/# buy medicines online in india
canadian pharmacy uk delivery buy prescription drugs from canada cheap canada drugs online reviews
safe canadian pharmacy: canadian mail order pharmacy – legitimate canadian pharmacy online
секс Горловка Знакомства Донецк – это запрос, который говорит о желании людей найти друзей, партнеров или спутников жизни в Донецке.
https://tijuanameds.shop/# buying from online mexican pharmacy
Бездепозитные бонусы в казино Бездепозитный бонус – это не просто бесплатные деньги, а ценный инструмент для обучения и тестирования. Это возможность примерить на себя роль профессионального игрока, изучить тонкости различных игр и понять, какие из них приносят наибольшее удовольствие и прибыль. Это шанс стать более уверенным и опытным игроком, готовым к игре на реальные деньги. Это инвестиция в себя и свои навыки, которая может окупиться многократно. Бездепозитный бонус в казино
TijuanaMeds mexican rx online TijuanaMeds
Online medicine home delivery: IndiMeds Direct – IndiMeds Direct
Its like you learn my thoughts! You appear to understand a lot approximately this, like you wrote the e-book in it or something. I think that you simply can do with a few percent to power the message house a bit, but other than that, this is fantastic blog. A fantastic read. I’ll definitely be back.
https://b2shop.gl/bs2best.html
http://canrxdirect.com/# cheapest pharmacy canada
https://indimedsdirect.com/# top 10 pharmacies in india
mail order pharmacy india reputable indian online pharmacy indian pharmacy online
Have you ever decided that watching DVDs and taking part in video video games is simply not enough in-automotive leisure for you?
TijuanaMeds: buying prescription drugs in mexico – TijuanaMeds
https://canrxdirect.com/# canadian pharmacy meds review
https://hbocqmxb.jz6897.com
Great blog here! Also your website loads up very fast!
What web host are you using? Can I get your affiliate link
to your host? I wish my site loaded up as quickly as yours lol
https://2bs-2best.at/https_bs2best_at.html
IndiMeds Direct IndiMeds Direct Online medicine home delivery
mexican mail order pharmacies: buying from online mexican pharmacy – mexico pharmacies prescription drugs
Introducing to you the most prestigious online entertainment address today. Visit now to experience now!
http://tijuanameds.com/# TijuanaMeds
https://aurora-game-ph.com/aurora-game-login/
https://yalla-bar-dahab.com/d8b3d8a7d981d98ad8aad8b4-d984d986-d98ad988d982d981d986d8a7-d8a3d8add8af-d988d987d8afd981d986d8a7-d8a7d984d984d982d8a8-d8a7d984d8a2/
https://sky-sports-football-eg.com/d8a5d986d8b2d8a7d8acd98a-d98ad8afd8b1d8b3-d982d8b1d8a7d8b1d8a7-d985d981d8a7d8acd8a6d8a7-d8a8d8b4d8a3d986-d984d8a7d988d8aad8a7d8b1d988/
Online medicine home delivery: best online pharmacy india – IndiMeds Direct
https://tijuanameds.com/# TijuanaMeds
https://betleao-cassino.com/conheca-a-betleao-cassino-confianca-e-satisfacao-na-pratica/
TijuanaMeds: TijuanaMeds – TijuanaMeds
TijuanaMeds TijuanaMeds TijuanaMeds
https://canrxdirect.shop/# reputable canadian pharmacy
вавада 100 бесплатных вращений Возможность бесплатно скачать приложение Vavada Casino на телефон – это прекрасная возможность всегда иметь под рукой любимые игры. Процесс скачивания прост и занимает всего несколько минут, после чего мир азарта будет у вас в кармане. Vavada Casino Отзывы
психиатрическая клиника Психиатрическая клиника. Само это словосочетание вызывает в воображении образы, окутанные туманом страха и предрассудков. Белые стены, длинные коридоры, приглушенный свет – все это лишь проекции нашего собственного внутреннего смятения, отражение боязни заглянуть в темные уголки сознания. Но за этими образами скрывается мир, полный боли, надежды и, порой, неожиданной красоты. В этих стенах встречаются люди, чьи мысли и чувства не укладываются в рамки общепринятой “нормальности”. Они борются со своими демонами, с голосами в голове, с навязчивыми идеями, которые отравляют их существование. Каждый из них – это уникальная история, сложный лабиринт переживаний и травм, приведших к этой точке. Здесь работают люди, посвятившие себя помощи тем, кто оказался на краю. Врачи, медсестры, психологи – они, как маяки, светят в ночи, помогая найти путь к выздоровлению. Они не волшебники, и не всегда могут исцелить, но их сочувствие, их понимание и профессионализм – это часто единственная нить, удерживающая пациента от окончательного падения в бездну. Жизнь в психиатрической клинике – это не заточение, а скорее передышка. Время для того, чтобы собраться с силами, чтобы разобраться в себе, чтобы научиться жить со своими особенностями. Это место, где можно найти поддержку, где можно не бояться быть собой, даже если этот “себя” далек от идеала. И хотя выход из клиники не гарантирует безоблачного будущего, он дает шанс на новую жизнь, на жизнь, в которой найдется место для радости, для любви и для надежды.
https://yalla-kora-live-eg.com/d8add8a7d8b1d8b3-d8a7d984d8b1d98ad8a7d984-d8a7d984d8b3d8a7d8a8d982-d987d8b0d8a7-d8b3d8b1-d8aad8b1d8a7d8acd8b9-d8a7d984d981d8b1d98ad982/
https://h3ltve7z.com/quem-levou-a-melhor-entre-flamengo-e-corinthians/
https://3o6kze3l.com/onde-assistir-ao-jogo-betis-x-athletic-bilbao/
https://u1bmqjtw.com/onde-assistir-ao-jogo-atletico-mg-x-river-plate/
mexican drugstore online: TijuanaMeds – buying from online mexican pharmacy
https://kora-live-360.com/d8a3d8b3d8b7d988d8b1d8a9-d985d98ad984d8a7d986-d98ad8a7d985d8a7d984-d8bad98ad8b1-d8a8d8b4d8b1d98a/
https://b2tor2.cc/bs2best_at.html
https://i3ax7gwv.com/onde-assistir-a-copa-do-brasil/
https://yalla-shoot-com.com/d8aad8b4d983d98ad984-d8b1d98ad8a7d984-d985d8afd8b1d98ad8af-d8a7d984d985d8aad988d982d8b9-d8a3d985d8a7d985-d8a3d988d8b3d8a7d8b3d988d986/
http://rxfreemeds.com/# what pharmacy can i buy viagra
enclomiphene price buy enclomiphene online enclomiphene for men
iraltone prospecto: tu boutique parafarmacia – Farmacia Asequible
https://yalla-live-football-eg.com/d981d98ad8afd98ad988-d8aad988d8aad986d987d8a7d985-d98ad981d988d8b2-d8b9d984d989-d8a8d988d8afd988-d8acd984d98ad985d8aa-d8a8d8abd984d8a7/
https://farmaciaasequible.shop/# Farmacia Asequible
Farmacia Asequible: Farmacia Asequible – Farmacia Asequible
https://enclomiphenebestprice.shop/# enclomiphene price
¡Saludos, apostadores talentosos !
Casino con bono de bienvenida sin docs – https://bono.sindepositoespana.guru/ casino online bono de bienvenida
¡Que disfrutes de asombrosas tiradas exitosas !
naltrexone river pharmacy RxFree Meds RxFree Meds
enclomiphene testosterone: buy enclomiphene online – enclomiphene buy
https://7lk38tsi.com/
This excellent website truly has all the information and facts I wanted about this subject and didn’t know
who to ask.
RxFree Meds: RxFree Meds – online pharmacy testosterone cypionate
https://e-football-eg.com/d8a7d984d8b0d983d8a7d8a1-d8a7d984d8a7d8b5d8b7d986d8a7d8b9d98a-d98ad8aad988d982d8b9-d986d8aad98ad8acd8a9-d8afd98ad8b1d8a8d98a-d8a7d984/
http://enclomiphenebestprice.com/# enclomiphene for sale
https://063csicb.com/santos-convoca-dois-atletas-da-copinha-para-disputar-o-campeonato-paulista/
of course like your website but you have to check the spelling on several of your posts.
A number of them are rife with spelling issues and I to find it very bothersome to
tell the reality then again I will certainly come back again.
https://yalla-bar.com/d985d988d8b9d8af-d988d8a7d984d982d986d8a7d8a9-d8a7d984d986d8a7d982d984d8a9-d984d985d8a8d8a7d8b1d8a7d8a9-d8a7d984d985d8b5d8b1d98a-d988/
https://fdhbr8iu.com/quem-esta-liderando-a-copa-do-brasil/
Terrific post however , I was wondering if you could write a litte more on this
topic? I’d be very grateful if you could
elaborate a little bit further. Thanks!
https://8fzss4zt.com/category/competicoes/
RxFree Meds domperidone us pharmacy RxFree Meds
https://football-strike.com/d8b5d8add98ad981d8a9-d8a5d986d8acd984d98ad8b2d98ad8a9-d8b4d8b9d8a8d98ad8a9-d8b1d988d986d8a7d984d8afd988-d8aad8add8b1d8ac-d985d8a8d8a7/
enclomiphene best price: enclomiphene online – enclomiphene online
http://farmaciaasequible.com/# zapatillas health opiniones
comprar cariban online: prospecto pastilla del dia despues – capital energy opiniones
https://blazecasino-br.com/blaze-casino-apostas-bonuses-e-como-ganhar-dinheiro/
https://marjackbet-br.com/marjack-bet-onde-a-sorte-encosta-a-estrategia/
https://tjk80nw9.com/
https://yalla-shoot-pro-eg.com/d8aad8b4d983d98ad984-d8b1d98ad8a7d984-d985d8afd8b1d98ad8af-d8a3d985d8a7d985-d8a2d8b1d8b3d986d8a7d984-d981d98a-d8afd988d8b1d98a-d8a3d8a8/
https://ohio-state-football.com/d8a8d98ad984d98ad986d8acd987d8a7d985-d98ad8b3d8acd984-d987d8afd981-d8aad8b9d8a7d8afd984-d8b1d98ad8a7d984-d985d8afd8b1d98ad8af-d8a7d984/
http://rxfreemeds.com/# online pharmacy no prescription ultram
https://8otrt1ve.com/gremio-apresenta-kike-olivera-e-luan-candido-como-novas-contratacoes/
https://aviatorbet-br.com/o-que-e-a-aviator-apostas/
подшипник для конвейера Виброустойчивые подшипники предназначены для работы в условиях повышенной вибрации. Они обладают специальной конструкцией и материалами, обеспечивающими устойчивость к вибрационным нагрузкам.
https://football-boots-eg.com/d8a7d984d986d8add8a7d8b3-d8a5d8b5d8a7d8a8d8a9-d8afd8a7d8b1d98a-d8b5d8b9d8a8d8aa-d8a7d984d8a3d985d988d8b1-d988d985d8b9d984d988d984/
enclomiphene enclomiphene testosterone enclomiphene for men
rite aid pharmacy store number: flomax pharmacy questionnaire – RxFree Meds
horario farmacia cerca de mi: Farmacia Asequible – mycostatin oral para que sirve
https://bong88-vn.com/
https://germany-football.com/d983d985-d8b9d8afd8af-d8a8d8b7d988d984d8a7d8aa-d8a7d984d8a3d987d984d98a-d8a7d984d8b3d8b9d988d8afd98a-d981d98a-d8aad8a7d8b1d98ad8aed987/
https://ajga4706.com/onde-assistir-copa-do-brasil/
https://yalla-shoot-kora-live.com/d8aad982d8a7d8b1d98ad8b1-d8a7d984d987d984d8a7d984-d8a7d984d8b3d8b9d988d8afd98a-d98ad8add8afd8af-d8a8d8afd98ad984-d986d98ad985d8a7d8b1/
https://uagbobz8.com/qual-e-o-proximo-adversario-do-gremio-na-copa-do-brasil/
https://ohio-state-football.com/d98ad8aad8b3d8b9-d984d980-100-d8a3d984d981-d985d8aad981d8b1d8ac-d985d8a7d986d8b4d8b3d8aad8b1-d98ad988d986d8a7d98ad8aad8af-d98ad982d8b1/
https://egypt-football-team.com/d985d983d8a7d986d8a9-d8aed8a7d8b5d8a9-d984d985d987d986d8afd8b3-d8a7d984d986d8b5d8b1-d981d98a-d986d8aed8a8d8a9-d8a2d8b3d98ad8a7/
https://enclomiphenebestprice.shop/# enclomiphene buy
римские шторы Шторы тюль — легкие и воздушные занавеси, создающие мягкий рассеянный свет и уютную атмосферу. Тюль отлично сочетается с плотными шторами, дополняя интерьер и обеспечивая приватность без затемнения комнаты. Разнообразие узоров и текстур позволяет подобрать тюль под любой стиль.
https://betmotion-br.com/desbravando-o-mundo-das-apostas-com-betmotion-um-passo-a-passo-de-como-comecar/
Farmacia Asequible Farmacia Asequible Farmacia Asequible
https://world-of-football-eg.com/d988d8a7d8a6d984-d8acd985d8b9d8a9-d98ad985d8afd8ad-d987d8a7d986d8b2-d981d984d98ad983-d8a3d8b9d8a7d8af-d987d98ad8a8d8a9-d8a8d8b1d8b4d984/
https://jp3nej09.com/voce-ja-sabe-quando-sera-o-sorteio-das-quartas-de-final-da-copa-do-brasil/
Howdy! I could have sworn I’ve been to this website before
but after browsing through some of the post
I realized it’s new to me. Nonetheless, I’m definitely delighted I found
it and I’ll be bookmarking and checking back often!
pharmacy near me: RxFree Meds – nexium pharmacy coupon
enclomiphene buy: enclomiphene testosterone – enclomiphene best price
http://enclomiphenebestprice.com/# enclomiphene online
https://football-players-eg.com/
https://rxfreemeds.shop/# the drug store
https://yalla-tv-eg.com/d985d988d8b9d8af-d988d8a7d984d982d986d8a7d8a9-d8a7d984d986d8a7d982d984d8a9-d984d985d8a8d8a7d8b1d8a7d8a9-d8b1d98ad8a7d984-d985d8afd8b1-2/
https://w8m181bl.com/quem-sera-que-o-paulo-pega-na-copa-do-brasil/
Right here is the perfect webpage for everyone who really
wants to find out about this topic. You understand so
much its almost hard to argue with you (not that I
really would want to…HaHa). You definitely put a fresh
spin on a topic which has been written about for ages. Excellent stuff,
just wonderful!
https://vck2ws73.com/imprensa-espanhola-revela-crise-em-vida-pessoal-do-ex-jogador-daniel-alves/
Hello, after reading this awesome paragraph i am too delighted to
share my experience here with colleagues.
enclomiphene best price enclomiphene online enclomiphene buy
https://xdmlayb7.com/quem-o-corinthians-vai-enfrentar-nas-oitavas-de-final-da-copa-do-brasil/
I like the valuable information you provide for your articles.
I’ll bookmark your blog and test once more right
here frequently. I am reasonably certain I will be informed a lot of new stuff right right here!
Good luck for the next!
https://p504hwt9.com/quem-e-o-maior-campeao-da-copa-do-brasil/
Farmacia Asequible: Farmacia Asequible – Farmacia Asequible
enclomiphene buy: enclomiphene online – enclomiphene
Have a quick look https://casino-ball.qx6255.com
https://rxfreemeds.shop/# tadalafil 20 mg online pharmacy
Find out how to do it https://aa2259.com/おでかけ ライブ 高崎-2025-06-16/64d0799928/
Want to know more? Click here https://rkpior.v71en.com
RxFree Meds online pharmacy ratings india rx pharmacy
See what we’ve got https://f7.r3re8.com
Ставки на спорт Фрибеты за регистрацию – отличный способ попробовать свои силы в ставках на спорт. Используйте их с умом и не рискуйте слишком многим.
Discover more here https://k.fu9924.com
enclomiphene: enclomiphene for men – enclomiphene citrate
See what we’re offering https://ys3735.com?cassino=nboo
https://farmaciaasequible.com/# Farmacia Asequible
Farmacia Asequible: Farmacia Asequible – Farmacia Asequible
https://enclomiphenebestprice.com/# enclomiphene online
Take a tour here https://339.ww6678.com
See what’s new https://657tgb.com/16-06-2025/69314429721691383263364555641515914683/
Read this post https://wc7353.com?cassino=qh
preferred rx pharmacy RxFree Meds thyroxine pharmacy
farma e: Farmacia Asequible – farmacia cadiz
Get the full story https://6b9ysb6z.pgi6e.com
https://enclomiphenebestprice.shop/# enclomiphene for sale
enclomiphene citrate: enclomiphene testosterone – enclomiphene testosterone
Check the info here https://fu9932.com/rup/65d12699808/
Продвижение товара в социальных сетях Маркетинговое продвижение бренда – это комплекс мероприятий, направленных на формирование положительного имиджа компании в сознании потребителей. Это создание уникального торгового предложения, разработка фирменного стиля, проведение рекламных кампаний и работа с репутацией.
buy enclomiphene online enclomiphene best price enclomiphene citrate
интерактивные дисплеи Кабинет робототехники с наборами Arduino Кабинет робототехники с наборами Arduino от ТОО «Astana IT Garant» — это практическая лаборатория для изучения основ электроники, программирования и мехатроники. Мы создаем кабинеты, которые позволяют учащимся создавать функциональных роботов от простых до сложных, развивая инженерное мышление и творческие способности. Наши наборы Arduino включают микроконтроллеры различных типов, датчики, исполнительные механизмы, элементы конструирования и электронные компоненты. Модульная система позволяет создавать роботов любой сложности: от простых мигающих светодиодов до автономных мобильных платформ. Разнообразные датчики расширяют возможности роботов: ультразвуковые для измерения расстояния, гироскопы для определения ориентации, камеры для компьютерного зрения, температурные и влажностные для мониторинга среды. Это позволяет создавать роботов для различных применений. Astana IT Garant предоставляет интегрированную среду разработки Arduino IDE и визуальные языки программирования Scratch for Arduino. Постепенный переход от блочного программирования к текстовому коду делает изучение доступным для учащихся разного возраста и уровня подготовки. Соревновательные проекты мотивируют учащихся к изучению робототехники. Мы организуем внутришкольные олимпиады и готовим команды к участию в региональных и международных соревнованиях по робототехнике, развивая командный дух и стремление к совершенству.
Go visit this site https://ospp3r5al3u.qt6622.com
гибкая керамика для фасада дома Гибкая керамика отделка фасадов дома может включать в себя различные цветовые решения и текстуры, что позволяет подобрать оптимальный вариант под любой архитектурный стиль.
RxFree Meds: RxFree Meds – motilium new zealand pharmacy
https://enclomiphenebestprice.com/# enclomiphene buy
Have a glance here https://xs3772.com?cassino=bhkvw
Want more details? Visit here https://xu7527.com/n/70d891891011/
Look at this article https://fu9953.com/unxpaxxrkmsu-9b999981/
Want to know more? Click here https://zs2575.com/sitemap.xml
RxFree Meds: RxFree Meds – RxFree Meds
http://farmaciaasequible.com/# Farmacia Asequible
pharmacy store nearby RxFree Meds can i buy viagra at a pharmacy
работа военным Военная служба – это не только обязанность, но и честь, которой следует гордиться.
Farmacia Asequible: direct farmacia – Farmacia Asequible
https://rxfreemeds.shop/# Persantine
http://enclomiphenebestprice.com/# enclomiphene buy
farmacias abiertas en bilbao vender farmacia en madrid farmavias
https://stroidom36.ru/catalog/doma/ Ремонт квартиры – это всегда хлопотное, но необходимое мероприятие. Комплексный подход включает в себя разработку дизайн-проекта, демонтажные работы, отделку стен, потолка и пола, а также установку сантехники и электрооборудования.
Farmacia Asequible: Farmacia Asequible – Farmacia Asequible
RxFree Meds: RxFree Meds – pharmacy online tadalafil
http://enclomiphenebestprice.com/# enclomiphene testosterone
Проверенное зеркало для доступа без ограничений: vavada рабочее зеркало
работа военным Работа военным: служение Родине Работа военным – это не просто профессия, это призвание. Это служение Родине, защита ее интересов и обеспечение безопасности граждан. Военные – это люди, готовые рисковать своей жизнью ради мира и спокойствия в стране. Служба в армии – это школа жизни, которая закаляет характер, учит дисциплине и ответственности. Военные приобретают навыки, необходимые не только на поле боя, но и в обычной жизни. Они умеют работать в команде, быстро принимать решения в сложных ситуациях и нести ответственность за свои действия. Военная служба – это возможность получить образование и профессию. Армия предоставляет широкий выбор специальностей, от технических до гуманитарных. Военные могут получить высшее образование за счет государства и стать высококвалифицированными специалистами. Работа военным – это стабильность и социальные гарантии. Военнослужащие получают достойную зарплату, жилье, медицинское обслуживание и другие льготы. Они уверены в завтрашнем дне и могут планировать свое будущее. Служба в армии – это возможность проявить себя и сделать карьеру. Военные могут расти по служебной лестнице, занимать высокие должности и участвовать в принятии важных решений. Они вносят свой вклад в развитие страны и укрепление ее обороноспособности. Работа военным – это почет и уважение. Военные – это герои, которыми гордится страна. Их подвиги и заслуги отмечаются государственными наградами и званиями. Они являются примером для подражания и вдохновляют молодежь на служение Родине. Служба в армии – это нелегкий труд, требующий мужества, силы и выносливости. Но это также возможность реализовать себя, принести пользу обществу и оставить свой след в истории. Работа военным – это выбор сильных и ответственных людей, готовых посвятить свою жизнь защите Родины.
enclomiphene: enclomiphene price – enclomiphene buy
online pharmacy lorazepam in store pharmacy RxFree Meds
RxFree Meds: RxFree Meds – RxFree Meds
enclomiphene price enclomiphene testosterone enclomiphene price
enclomiphene for men: enclomiphene best price – enclomiphene for men
http://enclomiphenebestprice.com/# enclomiphene citrate
психология будущего Плазменное поле: Концепция энергетического поля, окружающего человека. Влияние поля на физическое и психическое здоровье.
Farmacia Asequible: Farmacia Asequible – farmacia gran parque granada
Грузоперевозки Луганск Грузовое такси Луганск: Оперативная подача автомобиля в любой район города. Идеальное решение для срочных доставок и небольших переездов.
https://rxfreemeds.shop/# RxFree Meds
enclomiphene citrate: enclomiphene best price – enclomiphene citrate
https://rxfreemeds.com/# pharmacy online no prescription
Farmacia Asequible farmacia 24 horas barcelona cerca de mi Farmacia Asequible
Как вылечить народными средствами Целитель: поиск гармонии души и тела. В современном мире, полном стрессов и тревог, все больше людей обращаются к целителям в поисках альтернативных методов восстановления здоровья и душевного равновесия.
enclomiphene for sale: enclomiphene citrate – enclomiphene best price
buy enclomiphene online: enclomiphene best price – enclomiphene best price
https://farmaciaasequible.shop/# cápsulas baratas
enclomiphene testosterone enclomiphene online enclomiphene online
enclomiphene buy: enclomiphene citrate – enclomiphene best price
Грузоперевозки Луганск Перевозка стройматериалов Луганск: Доставка стройматериалов на строительные площадки и объекты.
profesional direct sales: farmacai – Farmacia Asequible
http://rxfreemeds.com/# RxFree Meds
best online pharmacies in mexico purple pharmacy mexico price list mexican online pharmacies prescription drugs
Online medicine home delivery: IndoMeds USA – IndoMeds USA
https://meximedsexpress.com/# MexiMeds Express
http://medismartpharmacy.com/# online pharmacy uk tadalafil
IndoMeds USA: IndoMeds USA – п»їlegitimate online pharmacies india
MexiMeds Express reputable mexican pharmacies online medication from mexico pharmacy
cheapest online pharmacy india: IndoMeds USA – IndoMeds USA
военная служба по контракту Служба по контракту: гордость за свою страну, вклад в ее развитие и процветание
http://meximedsexpress.com/# MexiMeds Express
MexiMeds Express: MexiMeds Express – MexiMeds Express
http://meximedsexpress.com/# MexiMeds Express
sky pharmacy MediSmart Pharmacy creighton university pharmacy online
Служба по контракту Служба по контракту: Современные условия службы, комфортное проживание и развитая инфраструктура военных городков. Созданы все условия для того, чтобы военнослужащие могли сосредоточиться на выполнении своих задач, не отвлекаясь на бытовые проблемы.
best canadian pharmacy to buy from: MediSmart Pharmacy – canadian drug prices
http://medismartpharmacy.com/# amoxicillin boots pharmacy
Sildigra: rx pharmacy services – periactin uk pharmacy
https://tryggmed.com/# apotek d vitamin
coronatest apotek: svensk apotek – billiga Г¤gglossningstest
lavt stoffskifte test apotek: kull tabletter apotek – apotek spania
Excellent post. I was checking continuously this blog and I am impressed! Very helpful info specifically the last part 🙂 I care for such information much. I was looking for this certain information for a long time. Thank you and best of luck.
nieuwe pharma MedicijnPunt bestellen medicijnen
Недвижимость в Турции Гражданство, паспорт Италии, Евросоюза, ЕС Почувствуйте себя частью великой истории и культуры, получив итальянское гражданство. Узнайте о возможностях получения гражданства по происхождению, браку или натурализации. Италия – это не только пицца и паста, но и перспективы для вашего будущего!
https://zorgpakket.com/# mijn medicijnen bestellen
https://v-tagile.ru/obschestvo-iyul-5/kak-vybrat-idealnyj-buket-dlya-zhenshchiny-ot-povoda-do-yazyka-tsvetov
farmacie medicijn: wat is mijn apotheek – bestellen apotheek
Appreciating the persistence you put into your blog and detailed information you offer. It’s good to come across a blog every once in a while that isn’t the same out of date rehashed information. Excellent read! I’ve bookmarked your site and I’m including your RSS feeds to my Google account.
online medicatie bestellen: online medicijnen bestellen zonder recept – online pharmacy
https://zorgpakket.com/# apteka internetowa holandia
frenadol kopen in nederland MedicijnPunt apotheek zonder recept
https://tryggmed.com/# cough syrup apotek
proteinpulver apotek: Snabb Apoteket – billig tandkrГ¤m
tryptofan apotek: Trygg Med – bifidobacterium infantis apotek
https://snabbapoteket.shop/# gratis babybox apotek
apotheek aan huis medicatie aanvragen online doktersrecept
¿Saludos jugadores entusiastas
Los mejores casinos europeos online tienen versiones especiales para jugadores VIP con atenciГіn dedicada y torneos exclusivos. casinos europeos online El trato personalizado marca la diferencia. Ser leal tiene sus privilegios.
Casinosonlineeuropeos recopila testimonios reales en vГdeo para reforzar la transparencia de sus reseГ±as. Esta iniciativa Гєnica en el sector aporta credibilidad. Saber en quГ© casino europeo confГan otros jugadores marca la diferencia.
Mejores casinos online con torneos mensuales – п»їhttps://casinosonlineeuropeos.guru/
¡Que disfrutes de grandes recompensas !
flytende magnesium apotek: kveldsГҐpent apotek – ryggstГёtte apotek
medicijen: Medicijn Punt – betrouwbare online apotheek
https://snabbapoteket.shop/# sax på engelska
online drugstore netherlands MedicijnPunt online apotheek
Muito obrigado!}
dildo billig: recept pГҐ apotek – apotek chat
de apotheek: apotheek aan huis – dokter online medicijnen bestellen
Игроки часто ищут вавада рабочее зеркало, и не зря — именно такие платформы обеспечивают честную игру и качественный сервис. Если вас интересует вавада рабочее зеркало, рекомендуем заглянуть сюда: вавада рабочее зеркало. Вы узнаете о бонусах, мобильной версии, рабочих зеркалах и многом другом. Проверяйте сами — вавада рабочее зеркало может приятно удивить!
|Hello to all, for the reason that I am actually keen of
https://tryggmed.shop/# kompresjons bh apotek
gentest apotek TryggMed beste nettapotek
babyboxar apotek: SnabbApoteket – apotek stan
ljumskbrГҐck bГ¤lte apotek: SnabbApoteket – conditioner svenska
https://snabbapoteket.shop/# kollagen apotek
http://zorgpakket.com/# internet apotheek nederland
Maks. Wygrana. Maksymalna wygrana w grze Sugar Rush jest ograniczona do 5000-krotności zakładu. Jeśli łączna wygrana w kaskadzie lub bonusie darmowych obrotów przekroczy tę wartość, runda zostanie zakończona i nastąpi wypłata. Słodycze obok owoców stanowią częsty motyw przewodni automatów hazardowych. Być może jest to zasługa ogromnej popularności mobilnych gier w rodzaju Candy Crush Saga? Sugar Rush od Pragmatic Play stanowi miły akcent w portfolio tego świetnego producenta. Obok Sweet Bonanza jest to dziś jeden z popularniejszych automatów z rozszerzoną liczbą rzędów i bębnów. Gra toczy się tu na siatce o rozmiarach 7 na 7 pól zaś zwycięskie kombinacje zliczane są systemem clustrowym – nie ma tu więc tradycyjnych linii wypłat. Możesz wygrać prawdziwe pieniądze w turniejach Lemon kasyno, które możesz pobrać ze swojego konta lub wydać na więcej gier online. Ale czasami nagrody konkursowe mogą obejmować bonusowe pieniądze, które wymagają obstawiania, darmowe spiny i punkty lojalnościowe.
https://drafabianemonteiro.com.br/gry-z-wysokimi-wygranymi-w-bizzo-casino-ktore-daja-najwiecej_1752674108/
Log in or register Recommend our store in the affiliate program and earn money. Zastanawiałeś się kiedyś, jak to jest trafić cukrowy jackpot? W Sugar Rush chodzi o to, aby trafić trzy lub więcej symboli scatter, aby uruchomić rundę darmowych spinów. Gdy już tam będziesz, to zupełnie nowa gra. Te mnożniki i wyróżnione miejsca z głównej gry? Nie resetują się. Nie, zostają, co ułatwia zbieranie wygranych. Możesz skończyć z wypłatą słodszą niż szarlotka babci w niedzielne popołudnie. A najlepsze? Możesz ponownie uruchomić więcej darmowych spinów w samej grze bonusowej, co sprawia, że jest to potencjalnie niekończąca się uczta smakołyków. Uwierz mi, raz spróbujesz tej rundy bonusowej w BDMBet, będziesz wracać po kolejne, trzecie… kto by liczył? Na naszym portalu znajdziecie wersję darmową Sugar Rush. Pozwala ona na nieograniczoną rozgrywkę przy komputerze lub na komórce. Niżej prezentujemy wam także listę najlepszych kasyn, które pozwalają zagrać bezpiecznie i bez stresu w ten i setki innych automatów jednoręki bandyta. Zobaczmy więc, co jeszcze oferuje ten ciekawy automat!
häst löss apotek öronproppar orolig mage gravid
ExpressCareRx: generic viagra online us pharmacy – valacyclovir hcl online pharmacy
MediMexicoRx: MediMexicoRx – buy antibiotics from mexico
https://indiamedshub.com/# indian pharmacy
buy priligy online pharmacy: rx pharmacy services – generic viagra pharmacy reviews
low cost mexico pharmacy online п»їmexican pharmacy order kamagra from mexican pharmacy
https://medimexicorx.com/# medicine in mexico pharmacies
¿Hola expertos en apuestas ?
Muchas plataformas permiten crear mГєltiples cuentas para diversificar estrategias sin restricciones.apuestas fuera de espaГ±aEsta flexibilidad es valorada por apostadores profesionales.
En casas apuestas extranjeras puedes acceder a jackpots progresivos internacionales. Los premios suelen ser mucho mayores que en sitios espaГ±oles. AdemГЎs, los pagos son rГЎpidos y sin impuestos ocultos.
Por quГ© casasdeapuestasfueradeespana es lГder en el sector – п»їhttps://casasdeapuestasfueradeespana.guru/
¡Que disfrutes de enormes premios mayores!
http://expresscarerx.org/# ExpressCareRx
IndiaMedsHub: IndiaMedsHub – best online pharmacy india
Производство подшипников в россии заводы Закупка подшипников – это ответственный процесс, требующий тщательного планирования и анализа потребностей предприятия. Важно определить необходимые типы и размеры подшипников, выбрать надежного поставщика и заключить выгодный контракт.
top 10 pharmacies in india india pharmacy mail order world pharmacy india
https://indiamedshub.com/# top 10 online pharmacy in india
gabapentin mexican pharmacy: best mexican pharmacy online – MediMexicoRx
online pharmacy india: top 10 pharmacies in india – pharmacy website india
ExpressCareRx ExpressCareRx can you buy clomid from a pharmacy
https://expresscarerx.org/# online pharmacy prescription
http://expresscarerx.org/# online pharmacy pain relief
Мегаполис в ночь не дремлет, и мы тоже: частная центр лечения алкоголизма и наркомании клиника https://mcnl.ru/ работает 24/7. Без записей и формальностей — приезд специалиста по адресу за 40 минут, мягкий детокс под седацией, ультрабыстрая капельница, нейрокоррекция у вас, бессрочное сопровождение. Без шума, анонимно, результативно — вернем вам трезвость без страха.
ExpressCareRx: pharmacy artane – ExpressCareRx
MediMexicoRx: semaglutide mexico price – get viagra without prescription from mexico
https://medimexicorx.shop/# pharmacies in mexico that ship to usa
ExpressCareRx ExpressCareRx ExpressCareRx
https://gidro-vanna-dush.ru
голодание Польза голодания: От снижения веса до улучшения когнитивных функций
Debet – Sân chơi cá cược thể thao số 1, cập nhật tỷ lệ kèo trực tiếp, hàng nghìn trận đấu mỗi tuần, bắt kèo dễ trúng lớn!
Подшипники для сельхозтехники Подшипники изготовитель Информацию об изготовителе подшипников всегда следует проверять.
Finax: ExpressCareRx – phenytoin pharmacy protocol
https://medimexicorx.shop/# MediMexicoRx
clomid online pharmacy no prescription uk: ExpressCareRx – cheapest pharmacy
erectile dysfunction causes ExpressCareRx tricare pharmacy crestor
|Tato stránka má rozhodně všechny informace, které jsem o tomto tématu chtěl a nevěděl jsem, koho se zeptat.|Dobrý den! Tohle je můj 1. komentář tady, takže jsem chtěl jen dát rychlý
http://indiamedshub.com/# IndiaMedsHub
валютные агенты Агенты платежи в Китай – это компании, которые предоставляют услуги по осуществлению платежей в Китай. Они берут на себя все вопросы, связанные с валютным законодательством и международными платежами.
gruppe? Der er mange mennesker, som jeg tror virkelig ville
IndiaMedsHub: indian pharmacy – buy prescription drugs from india
https://expresscarerx.online/# levofloxacin online pharmacy
It’s awesome to pay a quick visit this website and reading the views of all colleagues about this post, while I am also eager of getting know-how.
Car service near me
IndiaMedsHub: Online medicine home delivery – IndiaMedsHub
MediMexicoRx MediMexicoRx MediMexicoRx
https://medimexicorx.com/# mexican drugstore online
world pharmacy india: IndiaMedsHub – buy medicines online in india
buy medicines online in india: IndiaMedsHub – india pharmacy mail order
платежный агент перевод Банк международных платежей – это международная финансовая организация, которая осуществляет расчеты между центральными банками разных стран. Банк международных платежей играет важную роль в поддержании стабильности международной финансовой системы.
indian pharmacies safe indian pharmacy online п»їlegitimate online pharmacies india
que eu mesmo criei ou terceirizei, mas parece que
https://indiamedshub.shop/# indian pharmacies safe
morrisons pharmacy viagra: ExpressCareRx – bartell drug store pharmacy hours
gruppe? Der er mange mennesker, som jeg tror virkelig ville
clomid online pharmacy: what to consider as budget when running pharmacy store – ExpressCareRx
top 10 pharmacies in india IndiaMedsHub india online pharmacy
Мегаполис после заката не дремлет, и мы тоже: частная центр лечения алкоголизма клиника https://mcnl.ru/ ждёт 24/7. Без записей и документов — вызов врача к вам за менее 45 минут, щадящий детокс под седацией, сверхскоростная капельница, нейрокоррекция на месте, бессрочное сопровождение. Без шума, конфиденциально, точно — вернем вам трезвость без боли.
Solpot Casino pushes the limits of online entertainment Solpot Casino is booming—join the fun at solpot.xl-gamers.com https://solpot.xl-gamers.com Solpot Casino never disappoints high rollers: Bet it all at Solpot Casino and win a fortune!
http://medimexicorx.com/# reputable mexican pharmacies online
buy neurontin in mexico: finasteride mexico pharmacy – order azithromycin mexico
ExpressCareRx online pharmacy generic finasteride ExpressCareRx
https://finasteridefromcanada.com/# order cheap propecia without prescription
http://tadalafilfromindia.com/# tadalafil online no rx
Propecia for hair loss online: cheap Propecia Canada – Propecia for hair loss online
Propecia for hair loss online: generic Finasteride without prescription – buy cheap propecia for sale
Lexapro for depression online lexapro cost uk Lexapro for depression online
http://tadalafilfromindia.com/# generic Cialis from India
cheap Cialis Canada: Cialis without prescription – generic Cialis from India
Isotretinoin From Canada: Isotretinoin From Canada – generic isotretinoin
32WIN offers a legally licensed online betting platform, authorized by PAGCOR and trusted by thousands of players. From sports betting and live casino to lottery games, the platform impresses with its modern interface, fast deposit and withdrawal system, and daily high-value promotions.
Cialis without prescription buy Cialis online cheap tadalafil 5mg tablets in india
https://tadalafilfromindia.com/# generic Cialis from India
buy ball bearings buy deep groove ball bearings: Achieve versatile performance and reliable operation with deep groove ball bearings, the most common type of ball bearing. Designed to handle both radial and axial loads, these bearings are suitable for a wide range of applications. Explore our extensive selection and find the perfect deep groove ball bearing for your needs.
generic Finasteride without prescription: Finasteride From Canada – cost generic propecia price
cheap Cialis Canada: buy tadalafil 20 – Tadalafil From India
Tak Hej der til alle, det indhold, der findes på denne
http://isotretinoinfromcanada.com/# Accutane for sale
https://zoloft.company/# Zoloft Company
Lexapro for depression online Lexapro for depression online Lexapro for depression online
What’s up everybody, here every one is sharing these know-how, thus it’s fastidious to read this webpage, and I used to go to see this web site all the time.
https://phylife.ru/kak-ispolzovat-virtualnyj-nomer-v-avstralii-dlya-biznes-proekta-v-sfere-uslug.html
There is no doubt that this Megaways version will catch the eye of players and they will want to give it a spin. After all, the Buffalo King slot has been one of the gaming community’s favorites for quite some time now. If you’re looking for a Buffalo slot game that’s upping the ante, check out 5 Wild Buffalo from Relax Gaming and 4ThePlayer. Thanks to features like its Boosting Fortunes, you can really amp up the size of your prizes. Plus, there’s a Fortune Wheel that gives you a shot at even bigger rewards. The Buffalo Thunder feature lets you stack buffaloes that can turn into massive symbols with ever-increasing multipliers. The Free Spins are also packed with wild symbols that boost your winnings even more. So take a chance and let the Wild Buffalo guide you to your fortune.
https://sperminator.247kraft.com/stake-mines-strategy-that-doesnt-rely-on-guesswork/
Most rebuy tournaments offer unlimited rebuys for the first hour or so and then stop all rebuys after that, this casino will always give you great promotions with free spins. Which tournaments are held related to the buffalo king megaways game lucky, reload bonuses or cool battles. You can reach us via our contact us page, University of Western Australia. Players can get mind-blowing gifts in exchange for these points, and Chi Kong Tse. Then theres the wild, which tournaments are held related to the buffalo king megaways game Hong Kong Polytechnic University. But for the new players, and you cant use bonus funds. Here’s what you’ll get in this guide: a breakdown of how online slot games work, which ones have the best payouts, and where to play them legally in the US. We’ll also cover jackpot slots, high RTP games, and key features that make some slots better than others. Whether you’re looking for big wins, fun themes, or solid gameplay, this guide has you covered.
Lexapro for depression online: lexapro cost australia – Lexapro for depression online
tadalafil online no rx: Tadalafil From India – Tadalafil From India
Clean UI that’s intuitive for both newcomers and advanced DeFi users.
https://lexapro.pro/# lexapro pills for sale
Zoloft online pharmacy USA buy Zoloft online sertraline online
Highly praised for reliability — “I’ve bridged over 50 transactions without a single issue.”
sertraline online: Zoloft online pharmacy USA – buy Zoloft online
BBCR pillow block bearings: Enhance operational efficiency and simplify installation with our range of pillow block bearings. These pre-assembled units, featuring robust housings and self-aligning capabilities, offer unparalleled ease of use and reliable performance. Ideal for conveyor systems, agricultural equipment, and various industrial applications, pillow block bearings provide a cost-effective and versatile solution for supporting rotating shafts.
Propecia for hair loss online: generic Finasteride without prescription – Propecia for hair loss online
Fully decentralized with audited smart contracts and validator network.
https://lexapro.pro/# where can i purchase lexapro online
Transparent fee structure and gas‑optimized for cost efficiency.
http://isotretinoinfromcanada.com/# USA-safe Accutane sourcing
Isotretinoin From Canada order isotretinoin from Canada to US purchase generic Accutane online discreetly
cheap Cialis Canada: generic Cialis from India – cheap Cialis Canada
изготовление выставочных стендов москва Изготовление стендов в Москве: Гарантия качества и надежности Изготовление стендов в Москве – это гарантия качества и надежности. Многие компании имеют большой опыт работы и используют современные технологии, чтобы создавать стенды, которые соответствуют самым высоким стандартам.
Cialis without prescription: buy Cialis online cheap – tadalafil soft gel
buď vytvořil sám, nebo zadal externí firmě, ale vypadá to.
https://zoloft.company/# Zoloft online pharmacy USA
Tadalafil From India generic Cialis from India cheap Cialis Canada
Lexapro for depression online: Lexapro for depression online – lexapro coupon
изготовление стендов для выставки Выставочный стенд: Эффективный инструмент для продвижения бизнеса Выставочный стенд – это не просто демонстрационная площадка, а ключевой элемент маркетинговой стратегии компании, участвующей в выставке. Он служит визитной карточкой бренда, привлекает внимание потенциальных клиентов и партнеров, способствует укреплению имиджа и увеличению продаж. Грамотно спроектированный и оформленный стенд способен значительно повысить эффективность участия в выставке и обеспечить долгосрочные бизнес-результаты.
http://isotretinoinfromcanada.com/# generic isotretinoin
Tadalafil From India: Cialis without prescription – Tadalafil From India
https://tadalafilfromindia.com/# Tadalafil From India
lexapro 20 mg discount best price for lexapro Lexapro for depression online
Lexapro for depression online: buy lexapro from canada – Lexapro for depression online
https://zoloft.company/# sertraline online
Zoloft online pharmacy USA: cheap Zoloft – Zoloft for sale
wormhole portal
wormhole bridge
Мегаполис после заката не спит, а наша команда вдобавок всегда на страже: эксклюзивная наркологическая клиника https://mcnl.ru/ работает 24/7. Без бюрократии и лишних вопросов — срочный приём доктора к вам, щадящий детокс в сне, экспресс- капельница, нейрокоррекция у вас, долговечное сопровождение. Без шума, конфиденциально, результативно — вернем вам трезвость без страха.
Столица после заката не спит, а наша команда аналогично всегда на страже: частная наркологическая клиника https://mcnl.ru ждёт 24/7. Без очередей и документов — приезд врача к вам, щадящий детокс под седацией, сверхскоростная капельница, психологическая поддержка у вас, пожизненное сопровождение. Без шума, конфиденциально, эффективно — вернем трезвость без боли.
defillama portfolio
defillama dashboard
Zoloft for sale generic sertraline buy Zoloft online without prescription USA
https://frasesmotivacional.com/
uu88mobi.com is the official agent of UU88, one of the leading online entertainment platforms, offering a wide selection of betting games including casino, sports, slot games, and many other exciting options.
With a user-friendly interface and 24/7 professional customer support, 18win delivers a premium, secure, and reliable entertainment experience for users seeking top-tier online gaming.
azerbaycanda kazino sənayesi inkişaf etdikcə, oyunçular üçün daha çox imkanlar yaranır. Yerli və beynəlxalq operatorlar rəqabət edir.
https://finasteridefromcanada.shop/# Finasteride From Canada
buy Cialis online cheap: Cialis without prescription – medicine tadalafil tablets
lexapro generic 20 mg: lexapro 20mg pill – Lexapro for depression online
الاستمرار في توجيه الآخرين.|Ahoj, věřím, že je to vynikající blog. Narazil jsem na něj;
amecapitals.com Отзывы Отличная платформа для начинающих инвесторов. AME Capitals предоставляет все необходимые инструменты и обучение.
https://tadalafilfromindia.shop/# tadalafil mexico price
Accutane for sale USA-safe Accutane sourcing Isotretinoin From Canada
muito dele está a aparecer em toda a Internet sem o meu acordo.
https://lexapro.pro/# cheapest price for lexapro
tadalafil online no rx: Cialis without prescription – buy generic tadalafil
кайтсёрфинг Кайтсёрфинг – это больше, чем просто спорт, это образ жизни, объединяющий людей со всего мира, объединенных любовью к ветру, воде и приключениям. Это путешествия в экзотические места, новые знакомства и незабываемые впечатления.
buy Zoloft online: Zoloft for sale – buy Zoloft online without prescription USA
defillama yield farming
manta bridge
manta airdrop
buy Zoloft online buy Zoloft online without prescription USA sertraline online
https://lexapro.pro/# Lexapro for depression online
purchase generic Accutane online discreetly: generic isotretinoin – order isotretinoin from Canada to US
Cialis without prescription: Cialis without prescription – tadalafil online no rx
https://finasteridefromcanada.shop/# Finasteride From Canada
https://tadalafilfromindia.com/# cheap Cialis Canada
п»їlexapro: Lexapro for depression online – lexapro 50 mg
defillama airdrop
Base Bridge
кайтинг Кайт
https://tadalafilfromindia.shop/# Cialis without prescription
Isotretinoin From Canada purchase generic Accutane online discreetly order isotretinoin from Canada to US
http://ilianicolaevichzavialov.ru/
how much is generic lexapro: can i buy lexapro online without prescription – Lexapro for depression online
авто из китая Авто из Китая: от рабочей лошадки до технологического прорыва. Китайские автомобили прошли долгий путь, превратившись из бюджетных копий в современные, технологичные и конкурентоспособные машины.
как накрутить подписчиков в тг https://vc.ru/marketing/1826718-kak-nakrutit-podpischikov-v-tg-kanal-25-sposobov-nakrutki-v-2025-godu лучшие сервисы
defillama airdrop
USA-safe Accutane sourcing isotretinoin online cheap Accutane
buy lexapro without prescription: Lexapro for depression online – Lexapro for depression online
http://isotretinoinfromcanada.com/# USA-safe Accutane sourcing
generic Finasteride without prescription: generic Finasteride without prescription – buying propecia online
isotretinoin online: cheap Accutane – USA-safe Accutane sourcing
Tadalafil From India tadalafil 5 mg tablet coupon generic Cialis from India
http://xn--80aafabrjladsicc1amg1o4cf1dg.online/
Isotretinoin From Canada: purchase generic Accutane online discreetly – purchase generic Accutane online discreetly
Если вам нужна накрутка подписчиков в Телеграм бесплатно, то рекомендуем изучить рейтинг лучших сервисов на https://dtf.ru/top-smm/3922958-nakrutka-podpischikov-v-telegram-besplatno для безопасного и быстрого результата.
pokračovat v tom, abyste vedli ostatní.|Byl jsem velmi šťastný, že jsem objevil tuto webovou stránku. Musím vám poděkovat za váš čas
tadalafil online no rx: buy Cialis online cheap – tadalafil 20mg lowest price
мебель для зала суда Офисные кресла: ключевой элемент эргономики рабочего места.
generic Finasteride without prescription Finasteride From Canada cheap Propecia Canada
Propecia for hair loss online: order generic propecia for sale – propecia without a prescription
reading this weblog’s post to be updated daily.
http://finasteridefromcanada.com/# Finasteride From Canada
Pretty section of content. I just stumbled upon your weblog and in accession capital to assert that I get actually enjoyed account your blog posts. Anyway I will be subscribing to your feeds and even I achievement you access consistently fast.
Limousine service near me
generic Cialis from India: buy Cialis online cheap – Cialis without prescription
buy Accutane online: order isotretinoin from Canada to US – cheap Accutane
lexapro medication: Lexapro for depression online – Lexapro for depression online
Kèo Nhà Cái is an online platform dedicated to providing comprehensive sports betting information and services. Here, users can access:
Betting odds
Match previews and analysis
Fixture schedules
Expert predictions
And the latest news in the world of sports.
Whether you’re a seasoned bettor or a newcomer, Kèo Nhà Cái offers valuable insights to help you stay informed and make smarter betting decisions.
Противоосколочные модульные одеяла для защиты от дронов (из СВМПЭ) с доставкой по России (ПВЗ в ЛНР и ДНР) Лучшие противоосколочные одеяла из СВМПЭ для защиты военной техники.
purchase generic Zoloft online discreetly: buy Zoloft online without prescription USA – cheap Zoloft
https://zoloft.company/# cheap Zoloft
) Jeg vil besøge igen, da jeg har bogmærket det. Penge og frihed er den bedste måde at ændre sig på, må du være rig og
Химчистка мебели ростов
purchase generic Zoloft online discreetly: generic sertraline – cheap Zoloft
Why is DefiLlama considered an authoritative DeFi resource?
webové stránky jsou opravdu pozoruhodné pro lidi zkušenosti, dobře,
дачные домики Преимущества и недостатки каждого типа строений определяют сферу их применения. Бытовки – мобильность и экономичность, хозблоки – функциональность и практичность, дачные домики – комфорт и сезонное проживание, каркасные дома – скорость возведения и экономичность постоянного жилья.
стеклянная перегородка в душевую Стеклянные перегородки с подсветкой: создание эффектного освещения и оригинального дизайна. Типы подсветки, дизайн, установка.
Propecia for hair loss online: cheap Propecia Canada – generic Finasteride without prescription
плащ от тепловизора военный тепловизор Военные тепловизоры отличаются повышенной надежностью, дальностью обнаружения и устойчивостью к экстремальным условиям.
https://servicestat.ru/service-spb Servicestat.ru — это удобный каталог-рейтинг сервисных центров по ремонту электроники. На сайте собраны контакты (адреса, телефоны), отзывы клиентов, акции и скидки, а также оценки качества услуг. Пользователи могут быстро найти проверенные мастерские в своем городе, сравнить рейтинги и выбрать лучший вариант. Полезен для тех, кто хочет отдать технику в надежные руки.
? Поиск сервисов по местоположению и брендам
? Реальные отзывы и оценки клиентов
? Акции, скидки и спецпредложения
? Удобный фильтр для сравнения услуг
Идеальный помощник в поиске надежного ремонта!
amoxicillin 500 ClearMeds Direct amoxicillin 500 mg without a prescription
affordable Modafinil for cognitive enhancement: order Provigil without prescription – wakefulness medication online no Rx
antibiotic amoxicillin: ClearMeds Direct – amoxicillin online no prescription
https://clomidhubpharmacy.com/# how to get generic clomid for sale
Relief Meds USA: prednisone tablets – Relief Meds USA
gabapentin 300mg capsule NeuroRelief Rx gabapentin extended release depomed
neurontin vs generic gabapentin: gabapentin and sore throat – sciatica gabapentin dosage
low-cost antibiotics delivered in USA: price of amoxicillin without insurance – amoxicillin 500mg capsule cost
nootropic Modafinil shipped to USA order Provigil without prescription WakeMeds RX
Clomid Hub: clomid otc – can i order generic clomid online
https://clomidhubpharmacy.shop/# cheap clomid now
where to get prednisone: Relief Meds USA – Relief Meds USA
how to buy cheap clomid no prescription: Clomid Hub – where to get cheap clomid
information.|My family members every time say that I am killing my time here
order amoxicillin without prescription antibiotic treatment online no Rx ClearMeds Direct
restless leg syndrome gabapentin: gabapentin 300mg weight gain – ketamine gabapentin clonidine
where can i buy generic clomid now: Clomid Hub – Clomid Hub Pharmacy
обучение кайтсёрфингу Кайт лагерь: активный отдых и кайтсёрфинг нон-стоп. Кайт лагерь – это возможность совместить обучение кайтсёрфингу с веселой компанией, яркими вечеринками и незабываемыми приключениями.
http://clearmedsdirect.com/# antibiotic treatment online no Rx
where can you get amoxicillin order amoxicillin without prescription can you purchase amoxicillin online
buying generic clomid prices: Clomid Hub Pharmacy – how can i get cheap clomid for sale
Relief Meds USA: anti-inflammatory steroids online – anti-inflammatory steroids online
Clomid Hub Pharmacy: Clomid Hub Pharmacy – how to get cheap clomid tablets
Bk8
Bk8
WakeMeds RX where to buy Modafinil legally in the US prescription-free Modafinil alternatives
Clomid Hub Pharmacy: can you buy generic clomid without prescription – Clomid Hub Pharmacy
NeuroRelief Rx: NeuroRelief Rx – what is the maximum dose of gabapentin
обучение кайтсёрфингу Кайтсёрфинг летом: идеальный отдых на воде. Наслаждайтесь летним солнцем и ветром на лучших спотах.
Бот для накрутки подписчиков в телеграм – ТОП-25 лучших сервисов https://vc.ru/niksolovov/1275676-bot-dlya-nakrutki-podpischikov-v-telegram-top-25-luchshih-servisov Лучшие платформы для набора и накрутки
Togelup
ClearMeds Direct: Clear Meds Direct – low-cost antibiotics delivered in USA
Clomid Hub order cheap clomid Clomid Hub
Clomid Hub Pharmacy: where to get clomid now – Clomid Hub
Togelup
https://neuroreliefrx.com/# NeuroRelief Rx
ReliefMeds USA: prednisone 20mg capsule – prednisone 10 tablet
order corticosteroids without prescription: order corticosteroids without prescription – prednisone otc price
what is gabapentin 100mg: NeuroRelief Rx – can you gain weight on gabapentin
can i buy generic clomid without a prescription cost generic clomid without a prescription how to buy clomid no prescription
Живая накрутка ТГ вот статья: https://vc.ru/niksolovov/1259243-zhivaya-nakrutka-tg-top-19-servisov-2025-goda-moya-instrukciya Только проверенные бесплатные и платные способы получить больше подписчиков.
ReliefMeds USA: ReliefMeds USA – where can i buy prednisone without a prescription
order amoxicillin without prescription: amoxicillin cost australia – low-cost antibiotics delivered in USA
gabapentin 300 mg wikipedia: NeuroRelief Rx – gabapentin 300mg capsule gre
Frax Swap
Aw8
Clomid Hub Pharmacy Clomid Hub where to buy cheap clomid without prescription
What’s up i am kavin, its my first time to commenting anyplace, when i read this post i thought i could also make comment due to this sensible paragraph.
https://maps.google.pt/url?rct=j&sa=t&url=https://cabseattle.com/
https://neuroreliefrx.shop/# NeuroRelief Rx
Dragon money Dragon Money – это не просто название, это врата в мир безграничных возможностей и захватывающих азартных приключений. Это не просто платформа, это целая вселенная, где переплетаются традиции вековых казино и новейшие цифровые технологии, создавая уникальный опыт для каждого искателя удачи. В современном мире, где финансовые потоки мчатся со скоростью света, Dragon Money предлагает глоток свежего воздуха – пространство, где правила просты, а возможности безграничны. Здесь каждая ставка – это шанс, каждый спин – это предвкушение победы, а каждый выигрыш – это подтверждение вашей удачи. Но Dragon Money – это не только про выигрыши и джекпоты. Это про сообщество единомышленников, объединенных общим стремлением к риску, азарту и адреналину. Это место, где можно найти новых друзей, поделиться опытом и ощутить неповторимый дух товарищества. Мы твердо верим, что безопасность и честность – это фундамент, на котором строится доверие. Именно поэтому Dragon Money уделяет особое внимание защите данных и обеспечению прозрачности каждой транзакции. Мы стремимся создать максимально комфортную и безопасную среду для наших игроков, где каждый может наслаждаться игрой, не беспокоясь о каких-либо рисках. Dragon Money – это не просто игра. Это возможность испытать себя, проверить свою удачу и почувствовать себя настоящим властелином своей судьбы. Присоединяйтесь к нам, и пусть дракон принесет вам богатство, успех и процветание! Да пребудет с вами удача!
http://nirvanaplus.ru/
ClearMeds Direct: Clear Meds Direct – buy amoxil
order corticosteroids without prescription: order corticosteroids without prescription – ReliefMeds USA
Clomid Hub: Clomid Hub – cost clomid tablets
Anyswap
cost generic clomid Clomid Hub Clomid Hub Pharmacy
Aw, this was an exceptionally good post. Taking the time and actual effort to generate a top notch article… but what can I say… I put things off a lot and don’t manage to get nearly anything done.
https://maps.google.bg/url?sa=i&source=web&rct=j&url=https://cabseattle.com/
ClearMeds Direct: Clear Meds Direct – order amoxicillin without prescription
can gabapentin cause restless leg syndrome: gabapentin voice changes – buy generic fluoxetine
ReliefMeds USA: prednisone 5 mg cheapest – anti-inflammatory steroids online
gabapentin pulse rate NeuroRelief Rx NeuroRelief Rx
Mantle Bridge
https://neuroreliefrx.com/# gabapentin substance p
кайт школа Безопасность в кайтсерфинге: погодные условия, трафик на воде
matcha swap
NeuroRelief Rx: can i order gabapentin – gabapentin 5
10 mg prednisone tablets: prednisone 2 5 mg – prednisone pills 10 mg
prednisone without a prescription: order corticosteroids without prescription – order corticosteroids without prescription
NeuroRelief Rx NeuroRelief Rx NeuroRelief Rx
Bandartogel77
antibiotic treatment online no Rx: order amoxicillin without prescription – buy amoxicillin online uk
NeuroRelief Rx: gabapentin does it show up in drug test – NeuroRelief Rx
Clear Meds Direct rexall pharmacy amoxicillin 500mg amoxicillin 500 mg online
order corticosteroids without prescription: prednisone 475 – 20 mg of prednisone
Bos88
http://canadrxnexus.com/# canadian pharmacy cheap
CanadRx Nexus: CanadRx Nexus – CanadRx Nexus
CanadRx Nexus: global pharmacy canada – CanadRx Nexus
Paraswap
п»їlegitimate online pharmacies india indian pharmacy indian pharmacy paypal
Online medicine home delivery: IndiGenix Pharmacy – IndiGenix Pharmacy
кайт лагерь Влияние ветра на кайтсёрфинг: понимание стихии. Изучите типы ветров, их силу и направление, чтобы правильно выбирать кайт и безопасно кататься.
legal canadian pharmacy online: best canadian online pharmacy reviews – CanadRx Nexus
online mexico pharmacy USA MexiCare Rx Hub MexiCare Rx Hub
best online pharmacy india: IndiGenix Pharmacy – indian pharmacy
canadianpharmacyworld com: CanadRx Nexus – CanadRx Nexus
DefiLlama
кайтсёрфинг “Фристайл”: Зрелищные трюки и техника фристайла в кайтсерфинге
mantcha swap airdrops
https://canadrxnexus.shop/# canadian online pharmacy reviews
MexiCare Rx Hub: MexiCare Rx Hub – MexiCare Rx Hub
IndiGenix Pharmacy IndiGenix Pharmacy IndiGenix Pharmacy
MexiCare Rx Hub: buying prescription drugs in mexico – MexiCare Rx Hub
onlinepharmaciescanada com: canada ed drugs – canadian 24 hour pharmacy
mexico pharmacy: MexiCare Rx Hub – MexiCare Rx Hub
Fabulous, what a web site it is! This weblog presents helpful data to us, keep it up.
https://slovakia.kiev.ua/shcho-obraty-oryhinalne-chy-adaptovane-sklo-f.html
mail order pharmacy india indian pharmacy online IndiGenix Pharmacy
IndiGenix Pharmacy: IndiGenix Pharmacy – Online medicine home delivery
canada drugs online review: legal canadian pharmacy online – reliable canadian online pharmacy
Hometogel
http://indigenixpharm.com/# reputable indian pharmacies
mail order pharmacy india: pharmacy website india – Online medicine order
IndiGenix Pharmacy IndiGenix Pharmacy IndiGenix Pharmacy
CanadRx Nexus: canadian pharmacy 24 com – canadian mail order pharmacy
canadian pharmacy in canada: best online canadian pharmacy – CanadRx Nexus
order azithromycin mexico: MexiCare Rx Hub – modafinil mexico online
кайтинг Погода – ваш лучший друг или злейший враг. Следите за прогнозом ветра, учитесь предсказывать изменения и выбирайте споты с подходящими условиями.
MexiCare Rx Hub generic drugs mexican pharmacy MexiCare Rx Hub
real canadian pharmacy: CanadRx Nexus – canadian pharmacy world
indian pharmacy: IndiGenix Pharmacy – Online medicine home delivery
MexiCare Rx Hub: MexiCare Rx Hub – MexiCare Rx Hub
http://canadrxnexus.com/# cross border pharmacy canada
my canadian pharmacy reddit canadian pharmacy CanadRx Nexus
jonitogel
Greetings to all fortune seekers !
The streamlined 1xbet registration nigeria form only asks for essential details. Nigerian players love the simplicity and speed of account creation. 1xbet registration nigeria After finishing the 1xbet registration nigeria, a welcome pack with bonuses is automatically applied.
Secure your account today with 1xbet login registration nigeria and enjoy premium betting features. Nigerian users get access to a curated list of games and odds. Exclusive login bonuses come with every new 1xbet login registration nigeria.
Try 1xbet nigeria registration online mobile flow – п»їhttps://1xbetregistrationinnigeria.com/
Hope you enjoy amazing payouts !
I’m gone to say to my little brother, that he should also pay a quick visit this webpage on regular basis to take updated from newest gossip.
can i order generic vermox price
MexiCare Rx Hub: MexiCare Rx Hub – mexico pharmacies prescription drugs
tadalafil mexico pharmacy: finasteride mexico pharmacy – MexiCare Rx Hub
MexiCare Rx Hub: п»їmexican pharmacy – MexiCare Rx Hub
Sbototo
buy cialis from mexico mexico pharmacy buy cialis from mexico
CanadRx Nexus: www canadianonlinepharmacy – canadian pharmacies comparison
indianpharmacy com: indianpharmacy com – online pharmacy india
MexiCare Rx Hub: MexiCare Rx Hub – order azithromycin mexico
CanadRx Nexus my canadian pharmacy rx legit canadian pharmacy online
http://canadrxnexus.com/# CanadRx Nexus
canadianpharmacyworld com: best canadian pharmacy online – canadian pharmacy meds
MexiCare Rx Hub: best prices on finasteride in mexico – trusted mexico pharmacy with US shipping
п»їlegitimate online pharmacies india: online shopping pharmacy india – IndiGenix Pharmacy
Wow, superb blog layout! How long have you been blogging for? you make blogging look easy. The overall look of your web site is fantastic, as well as the content!
brand vibramycin 100 mg
Online medicine home delivery Online medicine home delivery IndiGenix Pharmacy
Kepritogel
Gengtoto
reputable mexican pharmacies online: mexico drug stores pharmacies – medicine in mexico pharmacies
online canadian pharmacy review: canada pharmacy world – canadian pharmacy cheap
MexiCare Rx Hub: buy kamagra oral jelly mexico – MexiCare Rx Hub
reputable indian online pharmacy IndiGenix Pharmacy IndiGenix Pharmacy
india online pharmacy: IndiGenix Pharmacy – buy medicines online in india
https://canadrxnexus.shop/# online canadian pharmacy
finasteride mexico pharmacy: MexiCare Rx Hub – best mexican pharmacy online
Hometogel
CanadRx Nexus: CanadRx Nexus – CanadRx Nexus
IndiGenix Pharmacy IndiGenix Pharmacy reputable indian online pharmacy
reputable indian online pharmacy: india pharmacy – IndiGenix Pharmacy
pharmacy rx world canada: CanadRx Nexus – canadapharmacyonline
MexiCare Rx Hub: semaglutide mexico price – legit mexico pharmacy shipping to USA
CanadRx Nexus northern pharmacy canada CanadRx Nexus
I was able to find good info from your content.
https://clients1.google.ad/url?q=https://cabseattle.com/
Tizanidine tablets shipped to USA: trusted pharmacy Zanaflex USA – cheap muscle relaxer online USA
https://glucosmartrx.shop/# AsthmaFree Pharmacy
FluidCare Pharmacy: FluidCare Pharmacy – lasix generic name
RelaxMedsUSA buy Zanaflex online USA trusted pharmacy Zanaflex USA
ventolin prescription uk: AsthmaFree Pharmacy – ventolin 200
IverCare Pharmacy: IverCare Pharmacy – ivermectin 2021
Salutations to all luck adventurers !
Make every game more thrilling from the start. 1xbet nigeria registration You’re just moments away from the full experience. Smart betting starts with a smart move.
Begin your adventure with 1xbet registration nigeria and enjoy full betting flexibility. From live games to slots, everything is ready. New players love the instant setup from 1xbet registration nigeria.
Tips for 1xbet registration by phone number nigeria – 1xbetnigeriaregistration.com.ng
Wishing you thrilling sessions !
can you buy ventolin over the counter australia cheap ventolin inhaler cost of ventolin in usa
http://fluidcarepharmacy.com/# buy furosemide online
cheap muscle relaxer online USA: order Tizanidine without prescription – safe online source for Tizanidine
IverCare Pharmacy ivermectin lotion cost IverCare Pharmacy
AsthmaFree Pharmacy: AsthmaFree Pharmacy – AsthmaFree Pharmacy
prescription-free muscle relaxants: order Tizanidine without prescription – safe online source for Tizanidine
prescription-free muscle relaxants: muscle relaxants online no Rx – affordable Zanaflex online pharmacy
AsthmaFree Pharmacy AsthmaFree Pharmacy AsthmaFree Pharmacy
relief from muscle spasms online: RelaxMeds USA – relief from muscle spasms online
http://asthmafreepharmacy.com/# no prescription ventolin hfa
RelaxMeds USA prescription-free muscle relaxants muscle relaxants online no Rx
lasix online: furosemide 100 mg – lasix side effects
semaglutide nausea relief: AsthmaFree Pharmacy – semaglutide pills
FluidCare Pharmacy FluidCare Pharmacy lasix generic name
Bosstoto
IverCare Pharmacy: IverCare Pharmacy – ivermectin injection for sheep
rx coupon ventolin ventolin coupon ventolin order
Zanaflex medication fast delivery: cheap muscle relaxer online USA – trusted pharmacy Zanaflex USA
http://glucosmartrx.com/# AsthmaFree Pharmacy
AsthmaFree Pharmacy: how does semaglutide work to lose weight – AsthmaFree Pharmacy
IverCare Pharmacy IverCare Pharmacy ivermectin covid dose
FluidCare Pharmacy: lasix uses – lasix online
AsthmaFree Pharmacy: where to buy semaglutide – AsthmaFree Pharmacy
safe online source for Tizanidine trusted pharmacy Zanaflex USA relief from muscle spasms online
AsthmaFree Pharmacy: strive pharmacy semaglutide reviews – AsthmaFree Pharmacy
http://glucosmartrx.com/# is rybelsus a high risk medication?
Mariatogel
FluidCare Pharmacy FluidCare Pharmacy lasix online
ivermectin gold: IverCare Pharmacy – ivermectin for mice
AsthmaFree Pharmacy: semaglutide weight loss dosage chart ml – AsthmaFree Pharmacy
I used to be able to find good info from your content.
Farmaci online: dove conviene?
AsthmaFree Pharmacy AsthmaFree Pharmacy AsthmaFree Pharmacy
goltogel login
lasix side effects: lasix 100 mg – FluidCare Pharmacy
safe online source for Tizanidine: Tizanidine tablets shipped to USA – order Tizanidine without prescription
https://relaxmedsusa.com/# RelaxMedsUSA
FluidCare Pharmacy FluidCare Pharmacy furosemide 100 mg
AsthmaFree Pharmacy: AsthmaFree Pharmacy – ventolin price
totojitu
IverCare Pharmacy: ivermectin dosage scabies – stromectol metabolize
FluidCare Pharmacy lasix 20 mg FluidCare Pharmacy
Zanaflex medication fast delivery: Zanaflex medication fast delivery – RelaxMeds USA
IverCare Pharmacy: ivermectin injectable for dogs – IverCare Pharmacy
meget af det dukker op overalt på internettet uden min aftale.
AsthmaFree Pharmacy AsthmaFree Pharmacy order ventolin online uk
order Tizanidine without prescription: order Tizanidine without prescription – trusted pharmacy Zanaflex USA
relief from muscle spasms online: safe online source for Tizanidine – RelaxMeds USA
https://fluidcarepharmacy.com/# FluidCare Pharmacy
webové stránky jsou opravdu pozoruhodné pro lidi zkušenosti, dobře,
|Tato stránka má rozhodně všechny informace, které jsem o tomto tématu chtěl a nevěděl jsem, koho se zeptat.|Dobrý den! Tohle je můj 1. komentář tady, takže jsem chtěl jen dát rychlý
IverCare Pharmacy IverCare Pharmacy IverCare Pharmacy
ventolin 100mcg online: ventolin medication – AsthmaFree Pharmacy
side effects of semaglutide for weight loss: semaglutide injections near me – AsthmaFree Pharmacy
tron defi swap
ventolin capsule price ventolin best price AsthmaFree Pharmacy
rybelsus drug classification: compounded semaglutide – pros and cons of semaglutide
IverCare Pharmacy: IverCare Pharmacy – ivermectin fleet farm
tron swap
Promo slot gacor hari ini: Beta138 – Link alternatif Beta138
Heya i’m for the first time here. I came across this board and I find It truly useful & it helped me out much. I hope to give something back and aid others like you aided me.
Nha cai uy tin Vi?t Nam: Casino online GK88 – Link vao GK88 m?i nh?t
Situs judi resmi berlisensi: Bandar bola resmi – Withdraw cepat Beta138
Jiliko login Jiliko login Jiliko login
Judi online deposit pulsa: Judi online deposit pulsa – Link alternatif Mandiribet
Hand Sanitisers
Jiliko casino walang deposit bonus para sa Pinoy: Jiliko – Jiliko
Jiliko login: Jiliko bonus – Jiliko casino
https://gkwinviet.company/# Ca cu?c tr?c tuy?n GK88
Pinco il? real pul qazan: Pinco il? real pul qazan – Etibarli onlayn kazino Az?rbaycanda
Slot jackpot terbesar Indonesia Mandiribet login Judi online deposit pulsa
I am really enjoying the theme/design of your blog. Do you ever run into any internet browser compatibility issues? A small number of my blog audience have complained about my site not working correctly in Explorer but looks great in Firefox. Do you have any suggestions to help fix this issue?
Slot gacor Beta138: Login Beta138 – Beta138
Link alternatif Beta138: Beta138 – Slot gacor Beta138
Beta138: Login Beta138 – Login Beta138
Have you ever considered writing an e-book or guest authoring on other websites? I have a blog based on the same ideas you discuss and would really like to have you share some stories/information. I know my subscribers would appreciate your work. If you’re even remotely interested, feel free to send me an email.
Nha cai uy tin Vi?t Nam Slot game d?i thu?ng Slot game d?i thu?ng
Link alternatif Abutogel: Bandar togel resmi Indonesia – Situs togel online terpercaya
eh07vz
Jiliko casino: Jiliko app – Jiliko app
¡Saludos a todos los buscadores de suerte !
Casasdeapuestassindni ofrece plataformas rГЎpidas y seguras. Casa de apuestas sin dni elimina esperas innecesarias. casasdeapuestassindni.guru Casas de apuestas SIN registro dni permiten jugar de forma inmediata.
Casa de apuestas sin dni es ideal para jugadores que no quieren dejar rastro. Puedes hacer depГіsitos instantГЎneos sin verificaciГіn. AdemГЎs, retiras sin lГmites.
Casas apuestas sin dni con pagos rГЎpidos – п»їhttps://casasdeapuestassindni.guru/
¡Que goces de increíbles ganancias !
Swerte99 slots: Swerte99 app – Swerte99
Your point of view caught my eye and was very interesting. Thanks. I have a question for you.
https://betawinindo.top/# Link alternatif Beta138
Pinco casino mobil t?tbiq: Yeni az?rbaycan kazino sayt? – Canl? krupyerl? oyunlar
Yeni az?rbaycan kazino sayt? Pinco r?smi sayt Onlayn kazino Az?rbaycan
Jiliko app: Jiliko bonus – Jiliko
Online betting Philippines: 1winphili – Jollibet online sabong
jollibet login: jollibet casino – jollibet login
Pinco casino mobil t?tbiq: Slot oyunlar? Pinco-da – Pinco kazino
Nha cai uy tin Vi?t Nam GK88 Link vao GK88 m?i nh?t
jollibet casino: 1winphili – 1winphili
|Hello to all, for the reason that I am actually keen of
information.|My family members every time say that I am killing my time here
Link alternatif Abutogel: Abutogel login – Abutogel login
Если ищете качественную информацию и полезные сервисы – есть отличное решение!
Обязательно посмотрите статью: 12 самых экономичных конвекторов отопления — эффективный обогрев при низком расходе
На портале собрано всё необходимое: статьи, новости, справочники, онлайн-инструменты. Экономит много времени на поиске нужной информации!
eu9
https://abutowin.icu/# Link alternatif Abutogel
Pinco r?smi sayt: Yuks?k RTP slotlar – Onlayn kazino Az?rbaycan
eu9
Pinco kazino: Slot oyunlari Pinco-da – Canli krupyerl? oyunlar
Beta138 Bonus new member 100% Beta138 Link alternatif Beta138
Link alternatif Beta138: Link alternatif Beta138 – Bonus new member 100% Beta138
Qeydiyyat bonusu Pinco casino: Yüks?k RTP slotlar – Uduslari tez çixar Pinco il?
Live casino Indonesia: Beta138 – Bonus new member 100% Beta138
Mandiribet Situs judi resmi berlisensi Situs judi online terpercaya Indonesia
Situs judi online terpercaya Indonesia: Live casino Mandiribet – Slot jackpot terbesar Indonesia
Abutogel: Abutogel – Abutogel
Swerte99 app: Swerte99 – Swerte99
https://swertewin.life/# Swerte99
Swerte99 online gaming Pilipinas: Swerte99 – Swerte99 bonus
Situs judi resmi berlisensi Slot gacor hari ini Slot jackpot terbesar Indonesia
Way cool! Some extremely valid points! I appreciate you writing this post and the rest of the site is extremely good.
Onlayn kazino Az?rbaycan: Onlayn rulet v? blackjack – Pinco casino mobil t?tbiq
Your point of view caught my eye and was very interesting. Thanks. I have a question for you.
Bandar togel resmi Indonesia: Situs togel online terpercaya – Jackpot togel hari ini
Casino online GK88: Slot game d?i thu?ng – Rut ti?n nhanh GK88
Online gambling platform Jollibet jollibet casino Jollibet online sabong
Swerte99 casino: Swerte99 slots – Swerte99 casino walang deposit bonus para sa Pinoy
Jiliko slots: Jiliko casino – Jiliko slots
https://pinwinaz.pro/# Onlayn rulet v? blackjack
This is the gold standard for what a crypto tutorial should be.
MediDirect USA cheapest online pharmacy india MediDirect USA
order from mexican pharmacy online: Mexican Pharmacy Hub – Mexican Pharmacy Hub
indian pharmacy: indian pharmacy – world pharmacy india
MediDirect USA: propecia pharmacy prices – MediDirect USA
Com tanto conteúdo e artigos, alguma vez se deparou com problemas de plágio ou violação de direitos de autor? O meu site tem muito conteúdo exclusivo que eu próprio criei ou
My USDT to DAI swap on Frax Swap completed in seconds.
https://indianmedsone.com/# Indian Meds One
MediDirect USA: inhouse pharmacy viagra – MediDirect USA
|Tato stránka má rozhodně všechny informace, které jsem o tomto tématu chtěl a nevěděl jsem, koho se zeptat.|Dobrý den! Tohle je můj 1. komentář tady, takže jsem chtěl jen dát rychlý
¡Un cordial saludo a todos los competidores del juego!
Los casinos europeos ofrecen una experiencia de juego segura y variada. Muchos jugadores prefieren casino online europa por sus bonos atractivos y soporte en varios idiomas. casinos online europeos Un casinos online europeos garantiza retiros rГЎpidos y mГ©todos de pago confiables.
Los mejores casinos en linea ofrecen una experiencia de juego segura y variada. Muchos jugadores prefieren casino online europa por sus bonos atractivos y soporte en varios idiomas. Un casino europeo garantiza retiros rГЎpidos y mГ©todos de pago confiables.
Casinos online europeos con bonos sin depГіsito y sorteos – п»їhttps://casinosonlineeuropeos.xyz/
¡Que goces de increíbles ganancias !
Indian Meds One: Indian Meds One – Indian Meds One
Mexican Pharmacy Hub: Mexican Pharmacy Hub – Mexican Pharmacy Hub
online shopping pharmacy india Indian Meds One top online pharmacy india
indian pharmacy paypal: buy medicines online in india – п»їlegitimate online pharmacies india
buy cheap meds from a mexican pharmacy: mexican pharmacy for americans – prescription drugs mexico pharmacy
best mexican online pharmacies: Mexican Pharmacy Hub – mexican border pharmacies shipping to usa
MediDirect USA MediDirect USA zyprexa pharmacy online
Inspiring! It shows that you don’t need to be a whale to make significant money in DeFi.
world pharmacy india: india online pharmacy – top online pharmacy india
https://indianmedsone.com/# mail order pharmacy india
Indian Meds One: top online pharmacy india – Indian Meds One
MediDirect USA: MediDirect USA – cheap online pharmacy
My brother recommended I might like this web site He was totally right This post actually made my day You cannt imagine just how much time I had spent for this information Thanks
Mexican Pharmacy Hub: Mexican Pharmacy Hub – Mexican Pharmacy Hub
online mexico pharmacy USA real mexican pharmacy USA shipping trusted mexican pharmacy
mail order pharmacy india: Indian Meds One – indianpharmacy com
legitimate online pharmacies india: pharmacy website india – Indian Meds One
Mexican Pharmacy Hub: buy cialis from mexico – trusted mexico pharmacy with US shipping
Rather than telling your college students what colors mean, ask students to inform you what colors mean for them.
https://indianmedsone.shop/# Indian Meds One
Indian Meds One: buy medicines online in india – Indian Meds One
MediDirect USA: pharmacy store fixtures and design – MediDirect USA
Indian Meds One Indian Meds One best online pharmacy india
MediDirect USA: modafinil online pharmacy – asacol pharmacy card
MediDirect USA: parlodel online pharmacy – percocet mexico pharmacy
Mexican Pharmacy Hub: buy from mexico pharmacy – Mexican Pharmacy Hub
u888game.org is the official agent of U888, one of the leading online entertainment platforms, offering a wide variety of games including casino, fish shooting, dice games (Tài Xỉu), sports betting, lottery, and more.
With a modern interface, fast deposit and withdrawal system, and 24/7 customer support, U888 delivers a safe, premium, and thrilling gaming experience, where you can win big every day.
best prices on finasteride in mexico buy antibiotics over the counter in mexico Mexican Pharmacy Hub
ventolin mexican pharmacy: MediDirect USA – MediDirect USA
reputable indian pharmacies: Indian Meds One – Indian Meds One
Mexican Pharmacy Hub: Mexican Pharmacy Hub – Mexican Pharmacy Hub
https://medidirectusa.shop/# online mexican pharmacy
MediDirect USA: MediDirect USA – pharmacy error methotrexate
Indian Meds One top 10 online pharmacy in india cheapest online pharmacy india
Indian Meds One: cheapest online pharmacy india – india online pharmacy
Mexican Pharmacy Hub: Mexican Pharmacy Hub – Mexican Pharmacy Hub
cheapest online pharmacy india: п»їlegitimate online pharmacies india – Indian Meds One
Mexican Pharmacy Hub safe place to buy semaglutide online mexico п»їmexican pharmacy
Online medicine order: Indian Meds One – buy prescription drugs from india
online pharmacy lamotrigine: diovan online pharmacy – MediDirect USA
https://mexicanpharmacyhub.com/# mexican rx online
789WIN is a trusted and legally licensed online betting platform, offering a wide range of entertainment services including sports betting, live casino, fish shooting, slot games, cockfighting, and lottery.
With its modern technology, user-friendly interface, and high-level security system, 789WIN delivers a premium, fair, and transparent betting experience.
The platform also features regularly updated promotions and 24/7 customer support, ensuring players can enjoy worry-free gaming while maximizing their chances of winning big every day.
Tadalify: Tadalify – Tadalify
Saudaratoto
Howdy! This article could not be written any better! Going through this post reminds me of my previous roommate! He continually kept preaching about this. I most certainly will send this article to him. Pretty sure he’ll have a great read. I appreciate you for sharing!
Kamagra reviews from US customers: Non-prescription ED tablets discreetly shipped – Sildenafil oral jelly fast absorption effect
I’d like to find out more? I’d care to find out more details.
SildenaPeak: female viagra otc – SildenaPeak
SildenaPeak online pharmacy viagra sildenafil tablet usa
Can I just say what a relief to find someone who actually knows what theyre talking about on the internet. You definitely know how to bring an issue to light and make it important. More people need to read this and understand this side of the story. I cant believe youre not more popular because you definitely have the gift.
SildenaPeak: cheap viagra for sale canada – sildenafil online singapore
SildenaPeak: compare viagra prices online – SildenaPeak
https://kamameds.shop/# Kamagra oral jelly USA availability
Fast-acting ED solution with discreet packaging ED treatment without doctor visits Safe access to generic ED medication
buy viagra online cheap india: SildenaPeak – SildenaPeak
Non-prescription ED tablets discreetly shipped: Compare Kamagra with branded alternatives – Non-prescription ED tablets discreetly shipped
Safe access to generic ED medication: Safe access to generic ED medication – KamaMeds
Keep on working, great job!
24/7 limo near me
Tadalify Tadalify cialis milligrams
NOHU90 – “Vũ trụ giải trí đa tầng” dành riêng cho giới cược thủ thời đại số, nơi quy tụ loạt minigame crypto-spin và jackpot xuyên không đậm chất tương lai. Gia nhập ngay để trải nghiệm sảnh chơi HyperWin Arena, nơi mỗi cú click có thể mở ra cả kho báu số tại https://nohu90giay.com/
Men’s sexual health solutions online: Men’s sexual health solutions online – Men’s sexual health solutions online
Fast-acting ED solution with discreet packaging: ED treatment without doctor visits – Non-prescription ED tablets discreetly shipped
Kamagra reviews from US customers: Non-prescription ED tablets discreetly shipped – Online sources for Kamagra in the United States
https://tadalify.com/# Tadalify
Men’s sexual health solutions online: KamaMeds – ED treatment without doctor visits
Tadalify: cialis 5 mg price – Tadalify
Tadalify buying cialis online safe cialis tadalafil & dapoxetine
SildenaPeak: SildenaPeak – SildenaPeak
Men’s sexual health solutions online: Affordable sildenafil citrate tablets for men – Kamagra oral jelly USA availability
Online sources for Kamagra in the United States: Non-prescription ED tablets discreetly shipped – Compare Kamagra with branded alternatives
ED treatment without doctor visits: Kamagra oral jelly USA availability – ED treatment without doctor visits
https://kamameds.shop/# KamaMeds
ED treatment without doctor visits Compare Kamagra with branded alternatives Kamagra reviews from US customers
reading this weblog’s post to be updated daily.
Tak skal du have!|Olá, creio que este é um excelente blogue. Tropecei nele;
SildenaPeak: buy viagra online with prescription – SildenaPeak
cheap t jet 60 cialis online: Tadalify – Tadalify
cialis slogan: Tadalify – Tadalify
KamaMeds Men’s sexual health solutions online ED treatment without doctor visits
Well I sincerely liked reading it. This tip offered by you is very useful for good planning.
Pokerace99
What’s up, after reading this remarkable paragraph i am also glad to share my experience here with friends.
http://smotri.com.ua/hermetyk-dlya-skleyuvannya-bez-pistoleta.html
cialis and high blood pressure: Tadalify – Tadalify
SildenaPeak: SildenaPeak – SildenaPeak
http://kamameds.com/# Affordable sildenafil citrate tablets for men
generic sildenafil usa: order sildenafil citrate online – can i order viagra online
Men’s sexual health solutions online KamaMeds Online sources for Kamagra in the United States
Compare Kamagra with branded alternatives: Men’s sexual health solutions online – Fast-acting ED solution with discreet packaging
Tadalify: Tadalify – is there a generic cialis available?
) سأعيد زيارتها مرة أخرى لأنني قمت بوضع علامة كتاب عليها. المال والحرية هي أفضل طريقة للتغيير، أتمنى أن تكون غنيًا و
Kamagra oral jelly USA availability: Non-prescription ED tablets discreetly shipped – Affordable sildenafil citrate tablets for men
Linetogel
It contains fastidious material.|I think the admin of this website is actually working hard in favor of his site,
Kamagra reviews from US customers: Compare Kamagra with branded alternatives – Kamagra reviews from US customers
Howdy I am so glad I found your blog page, I really found you by mistake, while I was researching on Bing for something else, Regardless I am here now and would just like to say many thanks for a incredible post and a all round thrilling blog (I also love the theme/design), I don’t have time to read it all at the moment but I have saved it and also added in your RSS feeds, so when I have time I will be back to read more, Please do keep up the awesome work.
http://i-medic.com.ua/yak-pravylno-dohlyadaty-za-korpusom-fary.html
sildenafil 50 mg tablet SildenaPeak SildenaPeak
Danatoto
Men’s sexual health solutions online: Compare Kamagra with branded alternatives – Affordable sildenafil citrate tablets for men
https://kamameds.com/# Kamagra oral jelly USA availability
Asian4d
SildenaPeak: how to get generic viagra online – canadian pharmacy viagra pills
Compare Kamagra with branded alternatives: Compare Kamagra with branded alternatives – Sildenafil oral jelly fast absorption effect
Linetogel
canada generic viagra price: where to buy viagra without prescription – SildenaPeak
Tadalify cialis and melanoma Tadalify
Hello there, You have done a great job. I will certainly digg it and personally suggest to my friends. I am sure they will be benefited from this website.
https://runflor.com.ua/fary-z-linzyamy-dlya-avto
tadalafil generic headache nausea: cialis pills pictures – Tadalify
KamaMeds: Online sources for Kamagra in the United States – Sildenafil oral jelly fast absorption effect
Fast-acting ED solution with discreet packaging: Kamagra oral jelly USA availability – Safe access to generic ED medication
https://kamameds.shop/# Affordable sildenafil citrate tablets for men
ED treatment without doctor visits KamaMeds Safe access to generic ED medication
cialis for sale online: Tadalify – is generic cialis available in canada
preГ§o viagra 50mg: SildenaPeak – SildenaPeak
I think that everything said made a bunch of sense. However, think on this, suppose you added a little content? I mean, I don’t wish to tell you how to run your blog, but suppose you added something that makes people desire more? I mean %BLOG_TITLE% is kinda vanilla. You might look at Yahoo’s front page and note how they create article titles to get viewers interested. You might try adding a video or a pic or two to get readers excited about everything’ve written. In my opinion, it would bring your website a little livelier.
http://davinci-design.com.ua/chy-vytrymuye-faru-butyl-pislya-kilkokh-tsykl.html
Kamagra reviews from US customers: KamaMeds – Fast-acting ED solution with discreet packaging
SildenaPeak: SildenaPeak – indian viagra
Affordable sildenafil citrate tablets for men Compare Kamagra with branded alternatives Safe access to generic ED medication
generic viagra from india online: SildenaPeak – SildenaPeak
https://sildenapeak.shop/# SildenaPeak
Men’s sexual health solutions online: Non-prescription ED tablets discreetly shipped – Online sources for Kamagra in the United States
Very shortly this web site will be famous amid all blog viewers, dueto it’s nice content
Men’s sexual health solutions online: Men’s sexual health solutions online – Compare Kamagra with branded alternatives
I really glad to find this website on bing, just what I was looking for : D besides saved to my bookmarks.
Tadalify: Tadalify – Tadalify
You got a very great website, Glad I observed it through yahoo.
cialis manufacturer coupon cialis precio cialis online aust
togelon login
almanya medyum
ED treatment without doctor visits: Safe access to generic ED medication – Kamagra reviews from US customers
Koitoto
Sildenafil oral jelly fast absorption effect: Online sources for Kamagra in the United States – Online sources for Kamagra in the United States
Affordable sildenafil citrate tablets for men: Men’s sexual health solutions online – Kamagra oral jelly USA availability
dingdongtogel
Safe access to generic ED medication ED treatment without doctor visits Online sources for Kamagra in the United States
almanya medyum
https://tadalify.com/# cialis online without a prescription
exchange USDT ERC20 in California
Safe access to generic ED medication: Kamagra oral jelly USA availability – Fast-acting ED solution with discreet packaging
SildenaPeak: female viagra for sale – viagra generic online canada
SildenaPeak: SildenaPeak – cheap viagra online canadian pharmacy
buď vytvořil sám, nebo zadal externí firmě, ale vypadá to.
FertiCare Online: buying clomid without rx – buying generic clomid without dr prescription
O conteúdo existente nesta página é realmente notável para a experiência das pessoas,
where can i buy generic clomid without dr prescription cost generic clomid for sale FertiCare Online
TrustedMeds Direct: TrustedMeds Direct – TrustedMeds Direct
prednisone without prescription 10mg: SteroidCare Pharmacy – otc prednisone cream
dingdongtogel login
IverGrove: ivermectin over the counter uk – ivermectin head lice
AML/CTF crypto Australia
FertiCare Online: where to get generic clomid without rx – FertiCare Online
stromectol 6 mg dosage: IverGrove – ivermectin buy
lasix 100 mg furosemida 40 mg lasix 100 mg
Ziatogel
ivermectin for people: IverGrove – ivermectin pour-on for cattle label
SteroidCare Pharmacy: SteroidCare Pharmacy – buy prednisone 5mg canada
SteroidCare Pharmacy: SteroidCare Pharmacy – SteroidCare Pharmacy
перила из нержавейки Купить перила для лестницы из дерева – это сделать выбор в пользу экологичности и природной красоты.
best ontario online casinos
http://steroidcarepharmacy.com/# SteroidCare Pharmacy
https://www.med2.ru/story.php?id=147093
Ziatogel
tripscan top Tripskan – это ваш персональный гид по миру, готовый ответить на любые вопросы и помочь в любой ситуации.
can i get clomid prices: how to get clomid without prescription – FertiCare Online
how to buy cheap clomid: how to get generic clomid without a prescription – FertiCare Online
buy amoxicillin without prescription: where can i buy amoxicillin over the counter – TrustedMeds Direct
https://sonturkhaber.com/
IverGrove: IverGrove – ivermectin 12mg price
SteroidCare Pharmacy: SteroidCare Pharmacy – SteroidCare Pharmacy
TrustedMeds Direct: amoxicillin for sale – rexall pharmacy amoxicillin 500mg
swap USDT in Aberdeen
Tether to EUR
https://cardiomedsexpress.com/# CardioMeds Express
CardioMeds Express: lasix tablet – lasix generic name
CardioMeds Express: CardioMeds Express – buy lasix online
prednisone oral: SteroidCare Pharmacy – prednisone canada pharmacy
sell Tether in Egypt
IverGrove IverGrove ivermectin 18mg
Tak skal du have!|Olá, creio que este é um excelente blogue. Tropecei nele;
lasix tablet: CardioMeds Express – generic lasix
buy amoxicillin 500mg canada: TrustedMeds Direct – TrustedMeds Direct
Your point of view caught my eye and was very interesting. Thanks. I have a question for you.
amoxicillin where to get: amoxicillin 500 mg without prescription – TrustedMeds Direct
http://pravo-med.ru/articles/18547/
https://ivergrove.com/# stromectol tab
FertiCare Online FertiCare Online FertiCare Online
Оптом подшипник цена Оптовая закупка подшипников – выгодное решение для крупных предприятий, позволяющее существенно снизить затраты на обслуживание и ремонт оборудования.
AI crypto trading success stories
CardioMeds Express: CardioMeds Express – furosemide 100 mg
p2p USDT Los Angeles
SteroidCare Pharmacy: prednisone 20mg online – prednisone 20 mg tablets coupon
exchange USDT in Houston
viagra pfizer 25mg prezzo: miglior sito dove acquistare viagra – cialis farmacia senza ricetta
farmacie online affidabili kamagra oral jelly spedizione discreta acquisto farmaci con ricetta
Farmacia online miglior prezzo: tadalafil senza ricetta – Farmacie on line spedizione gratuita
https://forzaintima.shop/# kamagra oral jelly spedizione discreta
Tron Staking
Retrograde evaluation issues: such problems, often additionally known as retros, usually current the solver with a diagram place and a question.
farmacie online autorizzate elenco: farmacia italiana affidabile online – farmacia online senza ricetta
best crypto AI projects
farmaci senza ricetta elenco: FarmaciDiretti – farmacie online autorizzate elenco
1вин официальный сайт мобильная 1win39.com.kg .
comprare farmaci online con ricetta medicinali senza prescrizione medica comprare farmaci online all’estero
Nice post. I be taught one thing tougher on totally different blogs everyday. It would at all times be stimulating to learn content material from different writers and follow slightly something from their store. I’d favor to use some with the content on my weblog whether or not you don’t mind. Natually I’ll provide you with a link in your internet blog. Thanks for sharing.
Где купить подшипники “Космические новости” переносят нас за пределы нашей планеты, рассказывая об исследованиях космоса, новых открытиях и планах на будущее.
farmacia online senza ricetta: Farmaci Diretti – farmacia online senza ricetta
Cryptohopper review
how to get xBOO
Farmacie on line spedizione gratuita: farmaci senza ricetta online – Farmacia online miglior prezzo
https://farmacidiretti.shop/# farmacia online senza ricetta
игровой компьютер для сталкер 2 Конфигуратор ПК: Соберите свой идеальный компьютер онлайн.
трип скан Трипскан: Легкость и удобство в каждой детали
miglior sito per comprare viagra online: sildenafil senza ricetta – viagra prezzo farmacia 2023
farmacia online piГ№ conveniente soluzioni rapide per la potenza maschile farmacia online piГ№ conveniente
But wanna say that this is invaluable, Thanks for taking your time to write this.
esiste il viagra generico in farmacia: Potenza Facile – viagra consegna in 24 ore pagamento alla consegna
Wow, incredible weblog format! How long have you ever been running a blog for? you made running a blog glance easy. The whole look of your site is great, as well as the content material!
Seattle Limo Service
Tron Staking
Tron Staking
farmacia online piГ№ conveniente: PilloleSubito – farmacia online piГ№ conveniente
migliori farmacie online 2024 kamagra originale e generico online farmacia online piГ№ conveniente
As I web-site possessor I believe the content material here is rattling magnificent , appreciate it for your hard work. You should keep it up forever! Good Luck.
top farmacia online: acquistare kamagra gel online – farmacia online
Iran Charter ( ایران چارتر ) is Iran’s first online charter and flight ticket purchase system Charter,as the first comprehensive online ticket service provider of charter airline tickets,seeks to provide easy and convenient services to customers for easy purchase of airline tickets,so we believe that the first principle of e-commerce is the ease of operation, with a contract As a ticket supplier,We have made it easy for you with charter companies and different airlines.
Новости Переговоры между Путиным и Зеленским — это не просто диалог двух лидеров. Это столкновение мировоззрений, стратегий и исторических нарративов. Политика, как искусство лавирования между интересами, требует от обеих сторон готовности к компромиссам. Финансовая нестабильность, вызванная СВО, затронула все регионы мира. Стратегии выживания и адаптации к новым экономическим реалиям стали приоритетом для многих стран. Европа ищет альтернативные источники энергии, Азия перестраивает логистические цепочки, а Америка сталкивается с растущей инфляцией. Безопасность и оборона диктуют необходимость увеличения военных расходов и укрепления альянсов. Новости и аналитика позволяют отслеживать развитие событий и формировать объективное представление о происходящем.
Farmacia online piГ№ conveniente: PilloleSubito – Farmacia online miglior prezzo
¡Mis más cordiales saludos a todos los visitantes habituales del casino !
Si quieres sentir la verdadera emociГіn, casino sin registro es el camino que no te decepcionarГЎ. La experiencia de jugar en casino sin registro es Гєnica, llena de adrenalina y sin restricciones molestas. casino sin registro Cada dГa mГЎs personas confГan en casino sin registro para disfrutar de apuestas rГЎpidas y seguras.
Los apostadores expertos saben que casinos sin licencia en EspaГ±ola ofrece cuotas mejores que los regulados. La diferencia de casinos sin licencia en EspaГ±ola estГЎ en que no tienes que esperar, solo juegas y disfrutas. Si quieres sentir la verdadera emociГіn, casinos sin licencia en EspaГ±ola es el camino que no te decepcionarГЎ.
Apuestas deportivas y casino vivo en casino online sin registro – п»їhttps://casinossinlicencia.xyz/
¡Que aproveches magníficas botes acumulados!
https://forzaintima.com/# kamagra oral jelly spedizione discreta
farmacia senza ricetta recensioni: PotenzaFacile – viagra acquisto in contrassegno in italia
) Vou voltar a visitá-lo uma vez que o marquei no livro. O dinheiro e a liberdade são a melhor forma de mudar, que sejas rico e continues a orientar os outros.
swap USDT in Nagoya
Tron Staking
acquisto farmaci con ricetta PilloleSubito farmacie online autorizzate elenco
farmacia online senza ricetta: accesso rapido a cialis generico online – acquisto farmaci con ricetta
Farmacia online miglior prezzo: farmacia italiana affidabile online – top farmacia online
I have been exploring for a bit for any high quality articles or blog posts on this sort of area . Exploring in Yahoo I at last stumbled upon this website. Reading this info So i am happy to convey that I have an incredibly good uncanny feeling I discovered exactly what I needed. I most certainly will make sure to do not forget this website and give it a look regularly.
reputable indian pharmacies: BharatMeds Direct – BharatMeds Direct
BorderMeds Express BorderMeds Express BorderMeds Express
Pretty! This was an incredibly wonderful article. Thanks for supplying this info.
https://bordermedsexpress.com/# mexican online pharmacies prescription drugs
buy meds from mexican pharmacy: BorderMeds Express – best prices on finasteride in mexico
BorderMeds Express: medication from mexico pharmacy – mexican mail order pharmacies
Your article helped me a lot, is there any more related content? Thanks!
обычные люди история Удивительные истории обычных людей В каждом из нас скрыт потенциал для невероятных свершений. Истории о людях, преодолевших себя, добившихся успеха вопреки обстоятельствам или совершивших героические поступки, вдохновляют нас и доказывают, что нет ничего невозможного. Они вселяют веру в свои силы и мотивируют на новые свершения.
Fantom ecosystem DEX
отдых на кавказе с детьми Отдых в Дагестане летом
чтение Обсуждение, как расширение кругозора
online mexico pharmacy USA: BorderMeds Express – safe mexican online pharmacy
MapleMeds Direct MapleMeds Direct texas online pharmacy
guardian pharmacy viagra: MapleMeds Direct – MapleMeds Direct
online pharmacy india: BharatMeds Direct – top 10 online pharmacy in india
https://bordermedsexpress.com/# BorderMeds Express
mail order pharmacy india: BharatMeds Direct – Online medicine order
п»їmexican pharmacy buy neurontin in mexico BorderMeds Express
the pharmacy store: savon pharmacy – MapleMeds Direct
Jozz casino известный бренд для ценителей азартных игр. Площадка предлагает акции, включая бездепы. Каталог слотов актуальный, проверенные бренды дают контент. Создать аккаунт легко, и сразу можно активировать промо. Стоит контролировать банкролл, для удовольствия. Подробнее: jozz casino регистрация
buying from online mexican pharmacy: buying prescription drugs in mexico – mexico drug stores pharmacies
cost of staining fence Wood Picket Fence Price Calculate the length you need to be installed.
buy antibiotics over the counter in mexico: isotretinoin from mexico – BorderMeds Express
online shopping pharmacy india: top 10 online pharmacy in india – india pharmacy mail order
clozapine pharmacy directory indian pharmacy online worldwide pharmacy online
Hello there! I know this is kinda off topic however I’d figured I’d ask. Would you be interested in trading links or maybe guest authoring a blog post or vice-versa? My site covers a lot of the same topics as yours and I feel we could greatly benefit from each other. If you’re interested feel free to send me an e-mail. I look forward to hearing from you! Superb blog by the way!
https://http-kra38.cc/
Your point of view caught my eye and was very interesting. Thanks. I have a question for you.
ton staking
обучение кайтсёрфингу
Most gadgets which are near or offshore are anchored to the sea ground.
https://maplemedsdirect.com/# mdma online pharmacy
BharatMeds Direct: buy medicines online in india – pharmacy website india
modafinil mexico online: gabapentin mexican pharmacy – tadalafil mexico pharmacy
BorderMeds Express: buy meds from mexican pharmacy – get viagra without prescription from mexico
top 10 pharmacies in india BharatMeds Direct п»їlegitimate online pharmacies india
ton staking
MapleMeds Direct: help rx pharmacy discount card – MapleMeds Direct
BharatMeds Direct: world pharmacy india – cheapest online pharmacy india
cheapest viagra online pharmacy: MapleMeds Direct – MapleMeds Direct
mail order pharmacy india BharatMeds Direct BharatMeds Direct
ton staking
BharatMeds Direct: BharatMeds Direct – BharatMeds Direct
http://bharatmedsdirect.com/# indian pharmacies safe
MapleMeds Direct: MapleMeds Direct – Aristocort
sildenafil mexico online: cheap mexican pharmacy – BorderMeds Express
best india pharmacy BharatMeds Direct BharatMeds Direct
porno cartoon kids
https://doc.clickup.com/90181218668/d/h/2kzkgcbc-1838/9e595111928abe1
CNP SJ150-4-1SWSP8SV Многоступенчатый погружной насос из нержавеющей стали SS304
программы для учета данных Специализированные решения для учета автотранспорта и спецтехники обеспечивают контроль за техническим состоянием, расходом топлива и работой водителей. Это позволяет снизить издержки и повысить эффективность использования техники.
BharatMeds Direct: BharatMeds Direct – BharatMeds Direct
pharmacy store online: MapleMeds Direct – MapleMeds Direct
Tron Staking
MapleMeds Direct: MapleMeds Direct – MapleMeds Direct
MapleMeds Direct MapleMeds Direct nexium pharmacy prices
BorderMeds Express: BorderMeds Express – BorderMeds Express
mexico pharmacies prescription drugs: mexican online pharmacies prescription drugs – BorderMeds Express
http://maplemedsdirect.com/# MapleMeds Direct
indianpharmacy com: buy medicines online in india – BharatMeds Direct
BorderMeds Express BorderMeds Express online mexico pharmacy USA
jackpot e vincite su Starburst Italia: bonus di benvenuto per Starburst – starburst
https://github.com/msrds/Microsoft-Remote-Desktop/releases
garuda888 game slot RTP tinggi: agen garuda888 bonus new member – garuda888
bonaslot situs bonus terbesar Indonesia bonaslot login bonaslot link resmi mudah diakses
garuda888 game slot RTP tinggi: garuda888 game slot RTP tinggi – garuda888 slot online terpercaya
http://1wstarburst.com/# migliori casino online con Starburst
Book of Ra Deluxe soldi veri: Book of Ra Deluxe slot online Italia – recensioni Book of Ra Deluxe slot
1win69 promosi dan bonus harian preman69 preman69 situs judi online 24 jam
giocare a Starburst gratis senza registrazione: bonus di benvenuto per Starburst – casino online sicuri con Starburst
daftar garuda888 mudah dan cepat: garuda888 login resmi tanpa ribet – garuda888 login resmi tanpa ribet
bonus di benvenuto per Starburst: jackpot e vincite su Starburst Italia – giocare da mobile a Starburst
book of ra deluxe Book of Ra Deluxe soldi veri recensioni Book of Ra Deluxe slot
https://1wbona.shop/# bonaslot